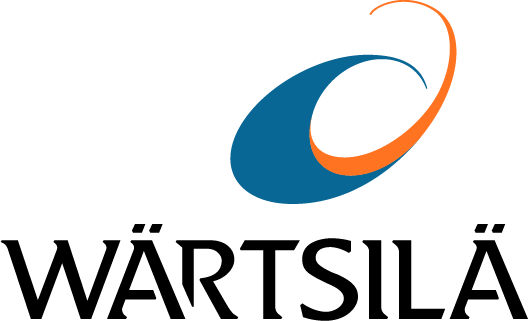
Updated 15.2.2024
Operational risk management is part of the daily work of the businesses. Opportunities and risks are identified, assessed, and managed daily and reported to the appropriate management level. The status of these opportunities and threats is reviewed periodically, and appropriate further actions are taken.
Manufacturing risk
Wärtsilä constantly analyses its manufacturing cost and the associated supply cost of raw materials and components while maintaining a suitable manufacturing footprint with adequate capacity. Manufacturing risk is mitigated by subcontracting and having smaller scope for in-house manufacturing. Wärtsilä’s Sustainable Technology Hub in Vaasa, Finland, is a modern, state-of-the-art R&D and manufacturing facility with a high level of flexibility and automated logistics. It also provides a partnering campus for collaboration and innovation. Whilst the transfer of activities from the old Vaasa facility to the Sustainable Technology Hub has been completed, the process of closing manufacturing in Trieste continues in 2024.
Regular risk assessments have been made for all the main delivery centres, and significant safety, environmental impact, and risk mitigation investments have been completed. Risk identification, assessment, and mitigation actions are executed regularly as part of operational management. Management systems for quality, environmental, occupational health and safety, and other systems are utilised to improve productivity, while safety and business continuity plans have been implemented for the key delivery centres.
Organisational capability
Wärtsilä’s target position is to shape the decarbonisation of marine and energy. Reaching the target position requires the right organizational capabilities and competencies. Accelerating the energy transition generates interesting job opportunities globally, both internally and outside Wärtsilä. An inability to attract and retain skilled and experienced staff will hamper the execution and timeline of the company’s strategic priorities. With various actions, Wärtsilä aims to be a preferred employer, able to recruit and retain qualified talent that matches the business needs and that is committed to the values, goals and objectives of the company.
Cost inflation and supply risk
Wärtsilä’s profitability during 2023 was still burdened by cost inflation, particularly due to projects taken before the acceleration of cost inflation. Projects that the company initiated before the acceleration of cost inflation, and which burdened profitability in 2022 and for the first three quarters of 2023, are now delivered and out of the orderbook. Over the course of the year, constraints in global supply chains have eased considerably and certain material costs have been reduced. However, the cost of energy and labour continues to maintain a high overall cost level.
To mitigate the impact of cost inflation, the company has, to the extent possible, implemented raw material indexation and other cost-related indices into the pricing of contracts. Furthermore, Wärtsilä is ready to execute price realisation in its transactional business and services, if needed. In addition, continuous improvement measures are taken to improve profitability. There is close monitoring and co-operation between the supply management and the sell-side pricing departments in the businesses to react to cost increases.
It is noteworthy that the ongoing war in Ukraine, the conflict in the Middle East, and any new geopolitical crisis, together with potential sanctions and regulative limitations, may pose additional disruption to trade flows and routes, thereby hampering the supply of key materials. In addition, the accelerating green transition may cause growing capacity issues and cost increases if the production capacity of critical key materials is not ramped up in parallel.
Also, regulatory development may impact Wärtsilä’s material costs through, for example, the Carbon Border Adjustment Mechanism (CBAM) initiated by the EU. Wärtsilä’s supply management is integrated into the businesses and works in partnership with the supplier base to create value for Wärtsilä’s customers by ensuring quality, on-time delivery, and the lowest total cost of ownership. Category management is applied to ensure coordinated interfaces and synergies for the cross-business supplier base. Indirect Procurement is a centralised function responsible for managing strategic sourcing activities for indirect materials and services in all businesses and support functions.
Wärtsilä has a process for managing and controlling its supplier network and for verifying that the suppliers’ performance meets expectations. Regular assessment of business interruption risk is a key activity in maintaining business continuity plans. This includes risk audits to the sites of the critical suppliers.
Wärtsilä has established close collaboration and long-term relationships with its main suppliers and follows their credit worthiness and financial condition. Wärtsilä uses an online solution for supply chain risk identification, assessment, and monitoring. Sourcing risks around the key components and materials are mitigated through diversification and dual- or multi-sourcing where possible.
Lifecycle quality of products and product liability risk
Wärtsilä’s quality framework focuses on preventive and proactive actions to deliver increased customer satisfaction, shorter lead times, and a reduced number of non-conformity claims. This is delivered by effective project risk management and strengthened awareness and ownership, supported by a streamlined product improvement process.
Several risk management techniques are applied in R&D, including the risk elimination tool FMEA (Failure Modes and Effects Analysis) and in-house validation testing. Wärtsilä seeks to control quality risks by monitoring the incoming quality of the supply chain, and by designing and manufacturing its products with all due care. A non-destructive robotic ultrasonic data analysis procedure enhances the probability of detecting imperfections in key components with a complex geometry.
Wärtsilä applies a GATE model to control the product development process. Initially, only a limited release of new products is allowed, and full release authority is given to the sales organisations only after testing and further validation has been completed.
Wärtsilä controls its manufacturing quality risks by applying several assurance and quality control principles. The level of quality assurance and control requirements are determined based on component criticality and are applied throughout the delivery chain. Requirement management is used to assess components systematically, enabling the allocation of resources and efforts according to component criticality. The ranking criteria indicates the consequence if a component fails. The objective is to improve quality proactively within product development, supply management, and the entire delivery process.
Non-conformity management focuses on developing and improving operations by registering and handling detected nonconformities, and by ensuring that the products and services received by customers are according to the agreed scope and specifications. Efficient handling, monitoring, and reviewing of non-conformities is crucial for proper risk management and mitigation.
Product improvement management (issue resolution) projects are prioritised based on risk and importance. Such a project is initiated when Wärtsilä identifies a technical issue according to claim statistics, customer feedback, or internal analysis, and the case fulfils the risk categorisation for a non-isolated case.
The businesses support customers in all warranty issues. This offers a feedback loop from the field to production and R&D, while taking care of the customers’ installations throughout their lifecycle. Warranty provisions are made to cover any costs that may arise after product delivery. The company’s product liability insurance covers unexpected damages.
Best industry practices and good governance are adopted to continuously improve quality. Each business is responsible for the quality of their products, its way of working, and services. Management at all levels are responsible for the quality output from their organisations and are accountable for ensuring that appropriate review and feedback mechanisms are in place.
Wärtsilä’s business level quality, environmental management, and occupational health and safety systems are ISO 9001:2015, ISO 14001:2015, and ISO 45001:2018 certified, with an emphasis on proactive risk and opportunity management. In addition, Wärtsilä’s GridSolv Quantum battery module qualifies under the 2023 revision of NFPA 855. It is also compliant with NFPA 69 and certified to UL 9540 and UL 9540A unit-level performance requirements.
Contractual risks
Wärtsilä’s equipment business includes projects and deliveries of various sizes requiring extensive coordination, efficient risk management, and seamless integration of all contracted systems and solutions. Energy has EEQ (Engineered Equipment) as the preferred offering, whereas EPC (Engineering, Procurement, and Construction) is only considered in selected markets. Going into 2024, more than 80% of the order book is for equipment orders. This rebalance in risk appetite leads to a stronger order book risk/reward profile for 2024 and onwards.
Wärtsilä provides lifecycle services to its customers in the form of transactional sales of spare parts and field service work, longterm service agreements, and service projects, such as engine upgrades, retrofits, and modifications of the installed base.
Wärtsilä places strong emphasis on having project management competences, proper technical assessment controls, time schedule and cost controls, supplier approval routines, and internal training programmes in place. With these measures, Wärtsilä aims to ensure the quality and performance of its contractual obligations during execution, and the upfront identification of specific risks and opportunities.
Product liability claim risk is reduced through maintaining a high level of lifecycle quality in the company’s products and work. This applies from the initial design and continues through all stages of the production process to the eventual field service activities. In addition, Wärtsilä has adequate insurance in place to cover product liability risk.
From time to time, Wärtsilä may be a defendant in a number of legal cases that have arisen out of, or are incidental to, the ordinary course of its business and, the company receives claims of different amounts and with varying degrees of substantiation. There is currently one unusually sizeable claim. It is Wärtsilä’s policy to provide for amounts related to the claims, as well as for litigation and arbitration matters, when an unfavourable outcome is probable, and the amount of loss can be estimated.
Risk of non-compliance, corruption, and fraud
Wärtsilä complies with the law and its own internal policies and procedures everywhere the company operates. Wärtsilä’s Code of Conduct is the key guideline for all employees globally, demanding high ethical standards and integrity.
Wärtsilä is fully committed to complying with anti-corruption laws and regulations. Wärtsilä acts to prevent corruption and does not accept violations of the principles set forth in the Code of Conduct, or in Wärtsilä’s Anti-Corruption and Compliance Reporting policies. The company forbids any kind of corruption and bribery and has a strict zero tolerance policy. There is a whistle-blowing channel in place for reporting misconduct incidents. Anti-Corruption risk assessments are carried out regularly as part of our continuous anti-corruption improvement efforts. In 2023, no instances of substantiated corruption or bribery were identified.
Compliance processes are embedded in all the businesses, and the responsibility for compliance and awareness of ethics and integrity is that of all Wärtsilä employees. The Compliance function promotes Group-wide compliance and continuously strives to raise awareness of the risk of corruption, bribery, and other misconducts.
While being aware of the risk of being subject to fraud by external business parties, and that the risk of corruption and fraud is heightened in several markets where the company operates, Wärtsilä consistently maintains its highly ethical practices.
Commodity price risk
Oil and gas
Global natural gas prices have decreased from the previous year’s extreme highs but remain above pre-2021 levels. The year witnessed significant gas price volatility, showcasing the market’s continued sensitivity to disruptions in supply and demand.
The direct effect of oil and gas price changes on Wärtsilä’s operations is limited and mostly related to fuel costs for engine testing, R&D activities, and the heating of some premises. In general, higher oil and gas prices represent a risk for global economic growth and increased operating costs, especially in the shipping markets. On the other hand, higher oil and gas prices increase interest in our energy efficiency offering and increase the demand for alternative green fuels as they become more cost-competitive against conventional fuels. Wärtsilä is a global company involved in different shipping and power plant segments where oil and gas price changes can have an opposing impact on demand drivers.
In the marine markets, high gas prices or their volatility are not expected to reduce the appetite for LNG as a fuel in the long run. The demand for LNG remains elevated as many countries in Europe have shifted away from Russian pipeline gas to LNG. Higher demand and supply volumes, and investments in expanding LNG liquefaction capacity, are driving demand for additional LNG carrier capacity. However, shipyards capable of building LNG carriers have few to no slots available in the coming years. Persistent high gas prices may encourage ship operators to switch temporarily from LNG to low-sulphur fuel, which most modern vessels can use in dual-fuel engines.
In the energy markets, gas price volatility and increasing prices can have a negative impact on the competitiveness of our portfolio, especially in thermal baseload plants, and may lead to more running hours of coal and nuclear power plants. Higher fuel prices may have an impact on project viability and customer decision making. However, these are expected to have less of an impact on thermal balancing power plants with fewer running hours.
Metals
Metal prices have an indirect effect on component cost for Wärtsilä’s products. Some key components are sourced with long-term contracts which limits raw material price volatility during the validity of contracts. However, concentrated supply chains of some raw materials, and the tight competitive situation to secure supplies, impose direct risks to the Energy business.
The battery industry has been suffering from price volatility, and the price of lithium has decreased significantly during the year.
Energy and electricity
High electricity prices, in general, support investments in new capacity by utility customers in the energy markets. High volatility, however, may have a negative impact on new investments.
Wärtsilä’s annual total energy consumption in 2023 was 271,429 MWh. This includes the electricity, heat and fuels used in Wärtsilä’s companies. Fuels are used mainly in engine testing and for R&D purposes, as well as in heating, production, and transportation.
Electricity is needed for manufacturing operations, but electricity prices have no substantial direct impact on Wärtsilä’s production capacity costs. In the new Sustainable Technology Hub facility in Vaasa, the heat generated in engine test runs is used for heating, whereas any excess electricity produced is sold to the grid at prevailing market prices. The discontinuation of engine manufacturing in Trieste Italy has reduced electricity consumption to some extent.