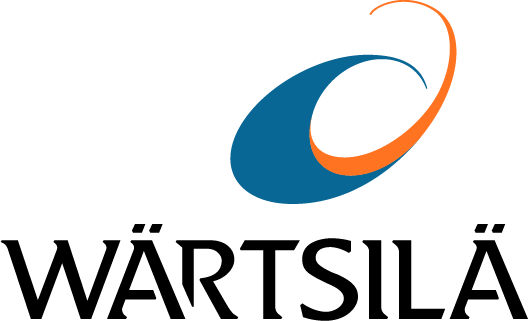
Horizontal and vertical conveyor systems used to discharge bulk cargoes. Originally developed to allow ships to handle cargoes at ports not equipped with their own gear, they are also used to reduce handling costs by minimising the need for stevedores.
- Bulklift system – The environmentally-friendly system which can be used to discharge most types of bulk cargoes with the hatches closed. Each hold is provided with a bucket elevator mounted on a moveable gantry. Cargo is discharged from the top and delivered to a conveyor system under the trunk deck from where it is delivered ashore through an elevator and slewing boom conveyor. A maximum discharge rate of 750 tonnes/h is possible and can be achieved with the ship at list of 2.5deg and with a trim of 1.5deg. The Bulklift system has its own diesel generator and is therefore independent of ship or shoreside power supplies.
- Cargo Scooper system – The system developed by Kvaerner. Cargo Scoopers are particularly suited for small vessels and use scrapers on the surface of the cargo to feed a system of conveyors and elevators. Cargo handling can be carried out with the hatches closed, which means that there are no delays because of bad weather.
- Consilium system – The gravity-fed, continuous belt type capable of discharge rates of up to 4500 tonnes/h or 100,000 tonnes/d, a rate far in excess of other conventional unloading systems. The cargo holds are V-shaped and cargo is fed by gravity from each hold onto three conveyor belts running beneath them. The cargo is then elevated from the tunnel area to the main deck level by an inward loading, vertical pocket-belt system onto an articulated unloading boom. The double-articulated boom and specially strengthened bucket tower is an essential feature of the system.