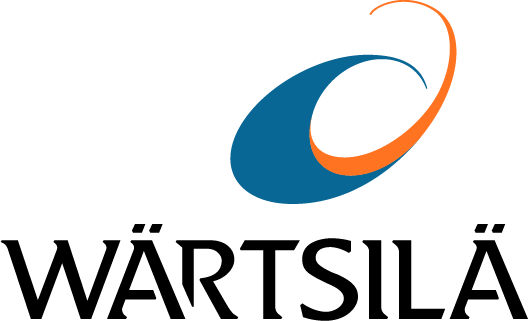
LNG carriers have, up to 2006, mainly been driven by steam turbines. The boil-off gas (BOG) from the LNG cargo has so far been used as fuel. Instead of previous practice using BOG as fuel, the Wärtsilä Hamworthy reliquefaction system establishes a solution to liquefy the BOG and return the LNG back to the cargo tanks.
BOG is removed from the cargo tanks by means of a two stage centrifugal compressor. The BOG is cooled and condensed to LNG in a cryogenic heat exchanger (cold box). Non-condensable items, mainly nitrogen, are removed in a separator vessel. From the separator, the LNG is returned to the cargo tanks by the differential pressure in the system. The cryogenic temperature inside the cold box is produced by means of a nitrogen compression-expansion cycle. The boil-off gas compressor capacity is adjusted automatically in accordance with the boil-off rate. Increasing and decreasing the nitrogen filling - and thus the compressor mass flow - is the basic control mechanism for the cooling capacity of the nitrogen cycle. Sensors and transmitters provide the required input signals to a programmable logic controller which will be part of the main vessel control system and enables 0-100% capacity control.
The main difference compared with the first generation is that the compressor unit has an additional compressor stage and inter-stage cooling. Heat is added to the boil-off gas before it enters the main cooling circuit so that the heat of compression can be removed at high temperatures in the cooling arrangement. The additional compressor stage allows the process to condense the boil-off gas at high pressure and temperature. This effect and that the heat of compression is removed early in the process is the main reason whereby the power consumption is reduced by some 15%.
For further information please visit www.wartsila.com