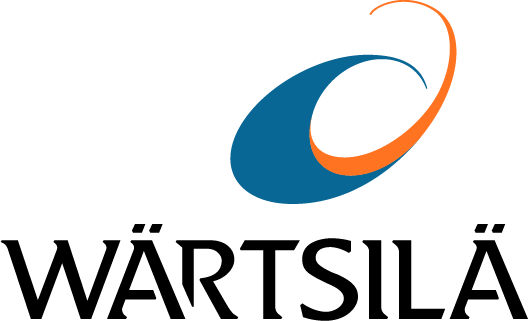
The diesel engine, named after Rudolf Diesel, is an internal combustion engine in which ignition of the fuel is caused by the elevated temperature of the air in the cylinder due to the mechanical compression; thus, the diesel engine is a so-called compression-ignition engine.