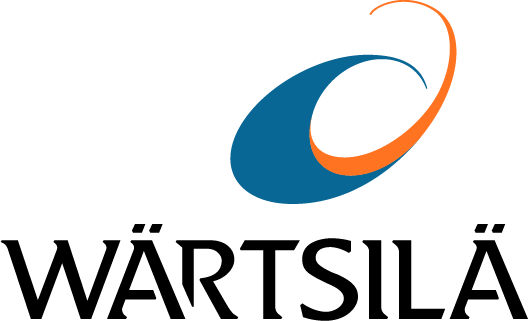
Electric marine propulsion is your flexible, future-proof choice. Flexibility is a must for your propulsion system because so many things in shipping are uncertain. Flexibility safeguards you from the uncertainty about the availability and cost of sustainable fuels, for example. If you are not sure about the additional power sources that will support your combustion engines, you will need flexibility. And you need it also if you do not know exactly which operational profiles will be sailed.
The classical diesel-electric propulsion systems are so flexible because of their one major advantage. The power generating units (gensets) are only electrically connected to the electric propulsion system. This makes it easier to replace the units with a new power source – such as a future-fuel operated engine, a battery, or a fuel cell.
The following is an example configuration of a diesel-electric propulsion system on a vessel:
Diesel-electric propulsion systems continue to be a solid choice for ships that
The current decarbonisation requirements mean that many more types of vessels are considering to adopt electric propulsion.
Wärtsilä has delivered electric propulsion systems to more than 350 vessels – to tugs, offshore vessels, research and special vessels, and to large cruise ships.
The electrical propulsion system is and environment-friendly choice – even with diesel generators. This is because the electrical propulsion system makes it possible to operate the generators within their optimal operational range even when the load from propulsion varies. Therefore, adopting electrical propulsion for a ship will significantly reduce the emissions of NOx/NO, CO, CO2, and soot.
At lower propeller speeds, the number of generators that are online can be adjusted according to the power demand. The engines will run more efficiently, which saves fuel.
Electric propulsion drives are unsurpassed for their quietness of operation.
The propulsion system on the ship can be configured for better redundancy. This makes the system more reliable.
The torque-speed of the motor makes it possible to high-over torque at propeller standstill. The propeller can be driven at all speeds and torques within design limits – there are no other limitations.
The electric propulsion system has excellent dynamic characteristics. Changes in propeller speed and propeller reversals during manoeuvring and positioning can be carried out at optimum acceleration rates.
The electric propulsion system generates only minimal harmonics or voltage drops, which means that the interference to mains is also minimal.
A ship navigation and command system can control the electric propulsion drives automatically, and manually from any control console. The functions and operating states are monitored, which will prevent operating mistakes and overloads.
Choosing an electric propulsion system for a ship instead of a diesel mechanical one means that there are fewer diesel motors and cylinders. The system also allows the motors to operate at constant speed, which reduces wear and tear. The result: lower costs of maintenance and less frequent demand for spare parts, which saves money.
Marine electric propulsion does have one drawback when compared to mechanical propulsion: electric losses. However, the losses are usually smaller than people think, and this article explains why the high losses are a myth.
Even so, electric propulsion is a superior choice because it is so flexible. After all, you can change the type of the propulsion power source, and the rest of the propulsion system can remain as it is.
There are three basic topologies for an electric marine propulsion system: AC system, DC system, and Wärtsilä’s patented Low Loss Solution. Wärtsilä will consider your vessel’s needs and propose the optimal topology, which may be a smart combination of the basic topologies.
AC system
Alternating Current (AC) systems are the most common diesel-electric propulsion solution, in Low Voltage (440 / 690V) or Medium Voltage (6.6 / 11 kV) settings. AC systems combine a switchboard with transformers and AFE (Active Front End) or DFE (Diode Front End) converters for each propulsor.
DC system
The Direct Current (DC) system is gaining popularity. A DC system is always in Low Voltage (1000V) setting. It has the advantage that it can connect variable speed gensets and batteries (which are always DC).
A DC Hub is a combined DC switchboard with converter modules. It is not always smaller or more light weight than the AC equivalent. It is important to weigh the possible advantages of a DC system, especially for a hybrid propulsion system.
Learn more from the article “DC or not DC, that is the question”.
Low Loss Solution
The patented Low Loss Solution from Wärtsilä reduces the number of transformers needed and reduces the electric losses. At the same time, it increases the redundancy of the propulsion system.
With its 200+ installations, the Low Loss Solution is the market standard for DP (Dynamic Positioning) / offshore vessels.
An electric propulsion system is the ideal choice for owners who feel uncertain about the future of propulsion solutions. The benefits become even more attractive when the vessel will be operating at varying speeds and have a high hotel load. Merchant vessels such as feeders, RoRos, short-sea PCTCs (pure car and truck carriers), and small tankers will gain significant benefits from an electric propulsion system.
Most modern cruise liners and ferries are designed with diesel-electric propulsion systems. These offer numerous advantages in terms of low noise and vibration-free operation, maximized cabin related loading capacity, more economic operation - especially the improved efficiency in partial propulsion power mode, a high degree of reliability, availability and redundancy, lower emission levels, and reduced wear and tear.
Electric propulsion for large LNG carriers
Electric propulsion can make it possible for LNG carriers to enter a new era of decarbonisation – and increase their cargo capacity at the same time. The next generation hybrid electric LNG carrier design features an impressive 185kcbm cargo capacity within the standard dimensions and displacement of a 174kcbm vessel design.
The design is the result of broad industry collaboration. Its five Wärtsilä 31 Spark Gas and Dual Fuel generating sets offer best efficiency and lowest emissions in this segment.
Offshore vessels, pipe and cable laying vessels, and heavy lift jack-up vessels have a long operations time at zero or slow speed and they are often required to change their speed rapidly. Therefore, they need a propulsion system with excellent dynamic characteristics to support their manoeuvring and positioning moves and reversals.
The ideal propulsion system for special vessels is based on speed-controlled DC or AC motors which drive the propeller either directly or via gears. Research and survey ships and fishery supervision vessels often choose the direct drive option because it is the most reliable and low noise design.
Multi-purpose vessels and icebreakers require propulsion systems with excellent dynamics to permit the flexible use of the torque speed characteristic, up to high-over torques and propeller standstill.
Discover the benefits others have already gained. Marine electric propulsion systems in offshore vessels, cruise ships, tankers, ferries, research vessels, tugs, yachts.
Discover these hand-picked articles to learn more about electric propulsion for ships.