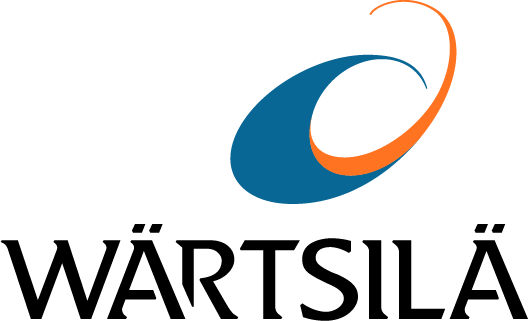
Our comprehensive lifecycle solutions include performance and maintenance management as well as operational expertise, leading to safe and reliable operations. Our solutions are based on the latest digital technologies, such as advanced analytics, artificial intelligence, and machine learning, combined with our vast knowledge and expertise in power generation.
With our remote support solutions, operating costs can be reduced through optimisation of data and infrastructure, and problems can be prevented before they even occur.
of support cases solved remotely in 2022.
of support cases solved during the same day in 2022.
power plants supported globally.
Wärtsilä Expert Insight uses cutting-edge artificial intelligence and advanced diagnostics to help power plant owners improve asset efficiency and reduce both operating costs and emissions. With the help of a Wärtsilä expert, the service spots and addresses smaller problems before they can develop into major issues that result in costly downtime.
Wärtsilä Expert insight takes predictive maintenance to the next level as part of Wärtsilä Lifecycle solutions. This digital service enables customer support to be delivered proactively by Wärtsilä Expertise Centres to ensure long-term accurate insight for predictive maintenance strategies.
Options for remote support and troubleshooting from a distance offers advantages in terms of availability and reliability, as well as cost advantages. Remote support solutions help reduce operating costs through optimisation of data and also help prevent problems before they occur.
To capture the benefits of real-time monitoring and data management and to provide remote support 24/7, our lifecycle solution customers are served with Wärtsilä Expertise Centres. The six centres located around the world provide operational support and maintenance management and analytics. Altogether the services provided by Expertise Centres enable the full potential of assets to be realised, as well as guaranteed performance, operational efficiency and optimised maintenance of the plant.
During a night shift, a Centre got a call to its emergency number from a site operator: an engine had shut down a couple of times during the night and the site personnel was not able to restart it. The customer, operating in the food & brewery industry, was facing potential loss in production availability.
Centre experts started troubleshooting the issue with the UNIC system and speed sensors. A speed sensor cable shield was disconnected and reconnected on the site, but that didn't yet solve the problem. An alarm list was checked remotely with Wärtsilä Operating Interface System (WOIS). The investigation of the list indicated a potential root cause for the engine shut down. Based on that, the Centre experts identified the problem and came up with a solution. The identified connection problem was then fixed by site people and the engine re-started successfully.
Using remote troubleshooting, the problem was solved in approximately two hours, with minimised production losses.
One of our Expertise Centers got a support request from a remote power plant in Africa, to solve pressure fluctuation on an engine feeder pump. If not managed in the long run, this can cause fuel pipes failures with consequent leakages and risk of fire in the engine room. The engineer at the site called to the team at the Expertise Centre through Augmented Reality application.
The technical expert answered the call and was able to see on the laptop the equipment in trouble, as if he were at site. He also received detailed photos, to which he wrote instructions. Thanks to image recognition features, the instructions appeared for the engineer at the site in the right position wherever he pointed at the equipment. The tool facilitated our expert being virtually at site with his full knowledge.
Thanks to this, it took just half an hour to fix the issue and eliminate all the related risks.
Wärtsilä's Houston Expertise Center is supporting and serving power plant operators remotely. Video »