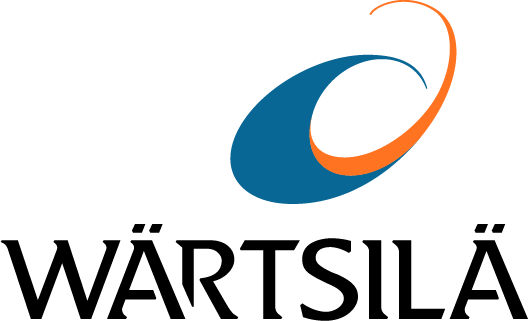
Amidst the coronavirus pandemic, Wärtsilä’s remote support was called upon to perform like never before, and it has come through with flying colours.
Being able to support and serve power plant operators remotely is now more important than ever. The flow of operating data is being harnessed effectively, meaning new, exciting opportunities. Remote excellence will likely kick off, unmanned power plants, and, eventually, autonomous ones.
Remote support solutions help reduce operating costs through optimisation of data and infrastructure, and, perhaps more importantly, they also help prevent problems before they even occur. This way, there are no unscheduled breaks in production and no dips in performance level.
Wärtsilä’s track record with remote support for its energy customers is superb. In 2020 – a pandemic year – the company’s experts were able to remotely solve 92% of requests coming through Wärtsilä Expertise Centres, even though the cases almost doubled compared to 2019. 88% of those requests were handled satisfactorily on the same day.
Kim Lindqvist, Director, Lifecycle Offering Development, says that remote support has been a strong area for development at Wärtsilä recently. While previously, Wärtsilä experts sometimes hopped on a plane and arrived on site perhaps two days after the initial request for assistance, the overall process has now been digitally fast-tracked.
“In many cases, we can solve the problem within an hour,” says Lindqvist.
Increased efforts are made for getting to the core of the problem as soon as possible, and solving it without delay, so that the customer can get back to running their everyday operations.
“If you’re dealing with a power plant, dependability is the key - if I take this to a personal level, I prefer my home to be warm when it's freezing cold in the middle of winter season where I live on the western coast of Finland - hours to wait for the electricity to turn on can feel long in the darkness!”
The evolution of remote support really started in early 2000s with condition monitoring which was still pretty reactionary in its nature – tackling challenges wherever they may arise. The next – and current – phase is performance enhancement.
“Our remote support enhances the performance of the customer plant, helping the customer be successful – even as business models are changing,” says Lindqvist.
Jonatan Rösgren, General Manager, Intelligent Controls, says that Wärtsilä has really zeroed in on ‘deep support’, where the customer can always have access to the best possible expert on that specific problem.
“When you’re talking about automation knowledge at this level, it’s a rare resource indeed. Working remotely from our Expertise Centre, we can use that expert as effectively as possible,” says Rösgren.
Wärtsilä’s global service network and local presence close to the customer in 70 countries complement each other very well; the global service network is a key part of the company’s global competitive advantage, and its local presence has been an anchor for operations throughout the pandemic.
The Trieste Expertise Centre for Africa & Europe is a prime example of remote support today. Having started in 2016, the Italian centre – one of six Wärtsilä Expertise Centres around the globe serving customers in the energy industry – has quickly made a name for itself as a fast and reliable problem-solver.
Expertise Centre Manager Emanuela Rusconi credits her troops for always going that extra mile for the customer.“Our team shares the same mission and the same goals – and has the competence and knowledge to deliver the results,” says Rusconi.
Presently, Trieste is supporting almost 90 installations across Europe and Africa, with engines numbering over 420 and the total power output hitting 4,000 MW. “Among supported installations, on top of traditional engine power plants, we can see that new energy storage sites are now increasing.”
According to Rusconi, the key to keeping our remote support expertise at such a great level is successful integration: taking people with different skillsets and integrating them into the team for maximum performance.
“This way, we’re able to work so much faster, allowing us to help more customers.”
Teams in Expertise Centres features remote support technicians, maintenance planners and data analysts, giving the customer expertise that runs deep and reaches wide.
“Working very closely together, we’ve achieved great things, and we’re going to keep broadening our knowledge base.”
Instead of providing spare parts for the customer, the Centres offer structured knowledge and support based on deep insights in installation lifecycle. Its trouble-shooting prowess is legendary, handling hundreds of cases every year, and the pace keeps increasing.
“In the last past two years, there’s been a big ramp-up in requests for support due to growth in our services and the very possibility of supporting remotely. We’ve been able to handle growing demand very well,” says Rusconi.
Growth in solved cases is certainly remarkable: by July this year, for example the Trieste team was already over the total number of cases solved in 2020. “And the growth in 2020 was also 50% higher than the previous year,” says Rusconi.
Looking to the future, Rusconi believes that the role of data will become even more crucial.
“The more data you have, the better the service you can provide. Having data integrated into your system in the right format can bring a considerable competitive edge,” she says, believing that “data scientists of the future” will have a hand to play in the success of the industry.
Wärtsilä has already unleashed the power of artificial intelligence to make the most of that data. Expert Insight, the company’s next-generation predictive maintenance platform, uses artificial intelligence that learns more and more as it keeps accumulating data. Expert Insight is a key tool in Wärtsilä’s remote support portfolio for power plant customers with a long-term service agreement based on Wärtsilä’s Lifecycle Solutions offering.
The AI is able to detect, for instance, erratic behaviour in power plant operations based on observation of baseline functionality. The platform also includes a built-in collaboration function that lets the Wärtsilä experts discuss any issues directly with the customer, which does come handy in a tight spot.
AI and next-level automation also work into the company’s long-term plans for autonomous power plants. Thanks to remote support, lean-manned plants are already viable, says Jonatan Rösgren. “The next steps towards the autonomous plant are remote and unmanned operation.”
There’s also the ‘health and safety’ angle to consider here. With no international travel involved, viruses and other bugs won’t spread. But how about digital viruses? Isn’t remote support vulnerable to cyber hacking or even hijacking? Rösgren says that all of Wärtsilä’s remote support systems have been built with robust cybersecurity in mind, from day one.
“We follow strict cybersecurity protocols to safeguard the customer’s operations at all times. As remote support is becoming more and more popular, we will continue to place great emphasis on safety issues,” says Rösgren.
According to Lindqvist and Rösgren, the big game-changer – at least in customer attitudes – was the coronavirus pandemic. Before the pandemic hit, customers were often quite keen on having “boots on the ground” and bringing in a Wärtsilä technician in person when faced with an issue that needed additional expertise. Embracing remote working due to the pandemic opened up new possibilities for remote support.
“Our customers have been trying new ways of running their operations during the pandemic, and we’ve been able to offer them great tools for that,” says Lindqvist, adding that the demand for remote support has skyrocketed during the pandemic.
“Remote support is clearly here to stay. Now, it’s about developing our offering even more and branching out to the hybrid world. As technology develops, there are many more things that we can keep an eye on remotely and make sure that everything runs smoothly.”
Tapping into the operations and performance data stream also gives room to steer the production into a more sustainable direction. With the rise of renewables, industry runs into new kinds of challenges. Wärtsilä’s experts can help find ways to make operations greener:
“We can pursue decarbonisation on a system level and achieve this through superior energy management systems supported by our Expertise Centres, ensuring system reliability,” concludes Lindqvist.