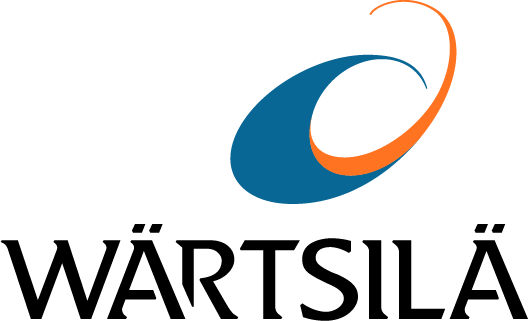
Ship and engine maintenance has evolved. From waiting until equipment breaks down to fix it, to scheduling maintenance according to the calendar, smart shipowners are always looking for ways to improve their maintenance processes to get ahead. The smartest way of all can save money, increase reliability and improve safety onboard – among a host of other benefits.
A smarter ship maintenance programme can deliver the following benefits:
The insight to control or reduce fuel consumption and emissions To achieve these benefits, first consider how you normally maintain your vessel. Is your maintenance reactive or scheduled?
Reactive maintenance is when you react to a problem – something breaks or is malfunctioning so you fix it. This is usually unscheduled maintenance and it can be the most expensive and inconvenient kind of maintenance.
Scheduled maintenance is also known as calendar-based maintenance. This is where you plan maintenance activities based on typical lifespans for equipment or on how much the equipment has been used. This might mean you’re replacing a part that doesn’t really need replacing, but by avoiding unscheduled downtime it can save you money in the long run.
Both reactive and scheduled maintenance are valid maintenance practices – but they won’t bring about all the benefits in our checklist above. So, if reactive maintenance or scheduled maintenance are not the smartest way to go, what is?
The number one thing you can do for smarter ship maintenance is to take full advantage of your ship’s data by combining it with cutting-edge AI and OEM expertise. There are three pieces in the puzzle.
Your vessel data is a key ingredient in the quest for smarter maintenance. Data can come from multiple sources:
Gathering data onboard helps you to monitor performance, ensure safety – and of course optimise maintenance. Gaining the knowledge is the first step towards understanding it.
The data you collect will give you insights into your vessel’s condition and potential faults – but it won’t improve your maintenance practices on its own. Continuous real-time analysis with cutting-edge AI will tell you when there are tiny changes to equipment parameters such as temperature, pressure or vibration – before they’d be apparent to crew onboard.
By monitoring trends and changes – and comparing them with historical data from thousands of vessels – it’s possible to recognise problems before they happen and act accordingly.
The final piece of the puzzle is human expertise to tell us what to do about the situation. Original equipment manufacturer (OEM) experts know equipment inside out and understand how equipment works in relation to the rest of the vessel. An OEM expert continuously monitoring your ship’s performance will help you with recommended maintenance actions and remote troubleshooting. Expert understanding of your equipment and operational conditions ensure that recommendations are uniquely tailored to your vessel, resulting in increased safety, reliability and efficiency.
These three elements – vessel data, AI and human expertise – together make smarter maintenance possible.
Smarter maintenance isn’t just about gathering data; it’s about using data to extract actionable insights that will enhance your ship’s performance and maximise your maintenance efficiency. Using ship data, AI and human expertise means you can switch from scheduled or reactive maintenance to a condition-based approach, using real-time data to trigger maintenance actions.
Combining ship data with artificial intelligence and human expertise is a smarter, more optimal approach to maintenance. Let’s look at our smarter maintenance programme checklist and see how a combination of ship data, AI and human expertise delivers the benefits:
If you’ve seen the benefits and want them for your vessel, Wärtsilä Expert Insight is a predictive maintenance service that combines cutting-edge artificial intelligence and advanced diagnostics with human expertise. The service monitors engine systems to proactively identify and address smaller problems before they lead to costly downtime – helping you to improve asset efficiency and reduce both operating costs and emissions. Crews on nearly 300 vessels already get invaluable support and peace of mind from Expert Insight.
Handpicked related content: Looking for more ways to cut your vessel’s greenhouse gas emissions? Here are 50 ways in one eBook: 50 great ways the maritime industry could reduce its greenhouse gas emissions.
Expert Insight recognises very early indications of equipment deterioration that cause vessels to run less efficiently. The service constantly learns and develops over time as it gathers more data, making it better at spotting potential problems every day. The rule-based algorithms are based on decades of OEM expertise from thousands of installations – even the smallest deviations from normal values can be identified and understood long before an alarm would be triggered. This helps to keep your equipment running optimally over its lifetime.
But it’s not just about advanced computing. While AI might be fast at processing data, Wärtsilä experts are still a vital part of the equation. Whenever an anomaly is detected, someone with expert knowledge of your equipment will interpret what the change means and give proactive maintenance advice and recommendations to your crew. These recommendations are based on forward-looking predictions rather than historical data and will be unique to your equipment.
Watch the video to find out how Expert Insight can help prevent problems before they happen – making your maintenance activities more predictable.
The solution is clear: gathering real-time vessel data is your first step. Combining the data with cutting-edge AI and human expertise is all you need for a smarter maintenance programme.
Resolving minor symptoms before they become major issues means you’ll have a more efficient and reliable vessel, with less unscheduled downtime and fewer costly repairs. Take advantage of vessel data, expert knowledge and advanced AI today.