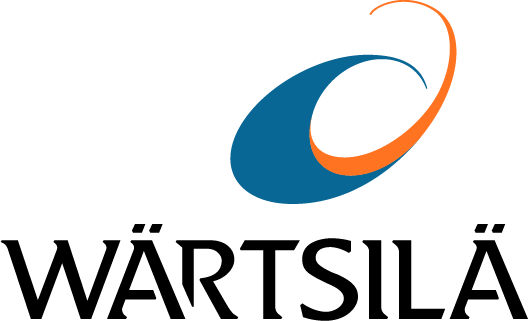
With more people than ever working remotely, options for troubleshooting from a distance have become a critical part of service offerings.
Demand for energy is changing as more and more people around the world are choosing to work away from a traditional office or factory setting. Research from the World Economic Forum indicates that weekday electricity demand in the U.S. and the UK in March and April, this year, has been closer to that of a typical weekend – off between 5-10% from usual demand. This research is reinforced with data from the Wärtsilä Energy Transition Lab, which shows that in Europe, demand for electricity fell by 10% in March and April 2020 compared with the same two-month period a year ago. These changes are putting pressure on utilities to maximise efficiency and reduce costs.
With uncertainty likely to be the new normal in the global economy for months to come, energy providers need reliable partners to support their operations. And, in an era of travel restrictions, the ability to solve problems remotely is especially valuable. Wärtsilä’s unique remote support solutions ensure power plant performance, operational efficiency, and optimised maintenance, tailored to a customer’s needs.
“Having the ability to support our customers remotely offers advantages in terms of availability and reliability, as well as, cost advantages,” says Markus Ljungkvist, Vice President of Energy Services at Wärtsilä.
Remote support solutions help reduce operating costs through optimisation of data and infrastructure and also help prevent problems before they occur. Wärtsilä’s next-generation predictive maintenance platform, Expert Insight, uses artificial intelligence that learns as it accumulates data, allowing it to detect anomalous behaviour in power plant operations based on observation of baseline functionality. The platform also includes a built-in collaboration function that allows Wärtsilä experts to discuss any issues directly with the customer.
“There are third-party companies that use machine learning techniques for anomaly detection. However, making the actual diagnosis requires deep subject matter equipment expertise, and this is what the third parties lack,” says Patrik Strand, General Manager, Product Management, Digital Product Development at Wärtsilä. “This is how Wärtsilä Expert Insight differs from competition – we know our equipment. There is always a Wärtsilä expert evaluating the deviations and supporting the customer by making the diagnosis and giving the recommendations. By combining advanced diagnostics, artificial intelligence and our in-house expertise, the true condition of equipment and systems can be defined.”
Expert Insight is one tool in Wärtsilä’s remote support portfolio for power plant customers with a long-term service agreement. Other solutions involve even more collaboration between Wärtsilä experts and on-site personnel.
“One of the solutions we offer is the remote guidance,” says Ljungkvist. “This is a solution with expert advice and guidance on technical issues related to site operations. Its primary purpose is to examine the operating conditions of an asset and determine the best course of action to optimise them.”
With remote guidance, a local engineer or operator can discuss questions with a Wärtsilä expert via a video collaboration app. The cyber secure app can be used with a personal smartphone or tablet and doesn’t require any specialised equipment.
Another solution is remote troubleshooting. The goal of this service according to Ljungkvist, is to identify the cause of technical issues related to site operations. It involves an analysis of power plant operational data, a diagnostic report of the operating condition, and actionable advice to return the equipment to optimal functionality.
This solution also requires only power plant connectivity to operate and offers a higher level of collaboration.
Customers who have long-term service agreements that include these services have ready access to experts at a Wärtsilä Expertise Centre they can contact for advice and assistance. The 10 Expertise Centres located around the world are key to Wärtsilä’s remote support.
“Instead of arranging for an engineer to travel to a power plant site for troubleshooting, we can instead review power plant performance parameters from our Expertise Centres and provide instant support and enables fast case resolution,” Ljungkvist says.
One example from the Wärtsilä Expertise Centre in Trieste is indicative of the kind of support that is regularly available. A customer had an engine shut down overnight and on-site personnel were unable to restart it, risking significant loss of production availability. Expertise Centre employees used the Wärtsilä Operating Interface System to check performance data against an alarm list, and a potential cause for the shutdown was identified. The on-site personnel were advised remotely about the solution, and the engine was restarted successfully with minimal production loss. Using remote troubleshooting, the problem was solved in approximately two hours. Had it been necessary to rely on a technician to be sent to the site to evaluate the situation, the problem would have taken 2-3 days to solve.
Out of the operational cases received by Expertise Centres in 2019, 62% were solved remotely and 67% were solved the same day.
Wärtsilä Expertise Centres optimise performance of power plant assets by taking a holistic view of plant operations. Using a broad spectrum of data collected by sensors at the power plant, Wärtsilä can evaluate the condition of equipment in real time.
“Having the ability to support our customers remotely brings an availability and reliability as well as a cost advantage to our customers. This is especially important for supporting plant operations in these times,” Ljungkvist says.