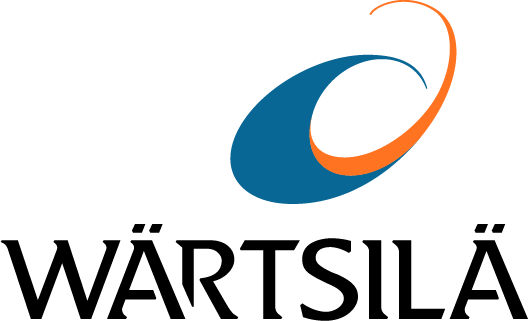
Managing the lifecycle of your vessels and other assets is the key to your competitiveness. And you won’t have to do that alone. Wärtsilä can help you in different ways – for example if you have these questions:
A service agreement with Wärtsilä is called a Lifecycle Agreement, and it means that you will have a reliable partner with special expertise. Think of the benefits you can get:
Reduced downtime
Lower risk of unplanned maintenance and costly downtime.
Fuel savings
Save fuel and reduce OPEX. Know your maintenance costs years ahead.
Lower emissions
Cut CO2 emissions and ensure compliance on your decarbonisation journey.
While much of the discussion around decarbonisation leads with fuel-saving hardware and software, one should not overlook the effect of maintenance.
If your vessel is well maintained and has a clean hull, you’re going to save on fuel and generate less emissions. Simple maintenance practices can have a surprisingly big impact on the efficiency of vessels.
And though some improvements may be small, make enough of them and they will add up to substantial fuel savings – and therefore a significant reduction in emissions.
Learn more about the effect of maintenance practices on your decarbonisation success:
One simple secret that will make your emissions reduction strategy look awesome
How has the guaranteed asset performance service helped Carnival decarbonise? This case study on a win-win partnership between Carnival and Wärtsilä has the answer
Take Wärtsilä as your partner for managing the lifecycle of your vessels. Start from there and you can take five surprising steps to get ahead of your competition. This infographic shows you how.
With performance guarantees, you can have a partnership that is set on common goals. Quantifiable performance targets are mutually agreed based on your business needs, and we guarantee that these targets will be reached and maintained.
The agreed common targets can include, for example, uptime, reliability, fuel consumption, emissions, and overhaul duration. With outcome-based partnership models risk and reward can be shared forming a true partnership.
Not sure if an outcome-based service agreement could meet your needs? Download this white paper for more in-depth information. You will also learn the seven signs that you might benefit from an outcome-based service agreement:How a service agreement could give your maritime business a competitive edge.
Learn more about performance guarantees:
How to get vessel uptime, fuel savings or reduced emissions – guaranteed
When your top requirement is the reliability of your vessels, you should sign up for the Expert Insight predictive maintenance service. It means that the Wärtsilä experts will monitor and analyse your vessels’ operational data and alert you if something looks suspicious. You will get the alert before things would go wrong.
Predictive maintenance is based on Artificial Intelligence and advanced diagnostics, which will detect even the smallest anomalies that may indicate a potential problem in the future.
The Expertise Centre will be like your extended crew member who will safeguard the reliability of your vessels. You will get more uptime and less unscheduled downtime leading to lost revenue, and you can also save big money on repairs.
Learn more about Expert Insight and the benefits it can provide:
Picture the scene: Your cruise ship is set to leave port with thousands of guest onboard. But there’s a problem which means your ship leaves port a day later than it should. What is the true cost of a day’s delay for a cruise operator? And how could you avoid such expensive problems?
Open the infographic
When the connectivity is already in place, Expertise Centres can provide you with remote Operational Support when you need it. In other words, you will have dedicated experts whom to call round the clock to get faster and better technical support and troubleshooting.
The Expertise Centre will be like your extended crew member who can give actionable advice and help solve issues no matter when they might occur.
According to statistics, 90% of issues can be solved remotely and 80% during the same day.
Wärtsilä’s digital remote support capabilities have proven to be of great value for us, saving both time and costs by often eliminating the need to have service people sent onboard in person.
One of the Wärtsilä services is called Data-driven Dynamic Maintenance Planning. When you choose it, our experts get access to your vessels’ operational data and can make the optimal maintenance plan.
Because the plan is based on the true condition of the assets, you won’t have to change engine parts only because a manual says so. Instead, they can be changed when it makes the best sense.
Thanks to actual data, maintenance plans can be more flexible. It may also be possible to extend overhaul intervals so that maintenance can take place when it’s most convenient for you.
A service agreement will give you cost predictability and it will be your assurance that your assets are maintained with the best OEM quality. Knowing the fixed, monthly fee makes budgeting easy for you.
Take a look at this case study: A Canadian ferry operator Société des Traversiers du Quebec chooses to delegate maintenance to a trusted partner
Data and digital solutions give you the possibility to make smarter maintenance decisions. For example, you can get cyber-secure connectivity and track the performance of your assets in real time. You can have fast and easy access to operational data such as trends, event logs, dashboards, and visualised engine performance.
With Wärtsilä, you can benefit from Data Insight whether you are on board or on shore.
You will of course want to keep your engines in top condition, and Wärtsilä can help you with that. Partner with us with a lifecycle agreement, and our experts will help you plan, prepare, and execute the maintenance.
Dedicated experts will make sure that things go smoothly, starting with the maintenance planning, then coordinating the spare parts, and finally making sure that a skilled maintenance workforce will be available to do the work with top quality.
Discover the benefits others have already gained from choosing a Lifecycle agreement with Wärtsilä:
Discover these insightful articles - learn more about lifecycle agreements and build your knowledge about managing the lifecycle of your vessel:
Wärtsilä’s expertise covers the full spectrum of lifecycle services. Take advantage of this expertise. You can ensure your competitiveness while you manage the lifecycle of your vessels and other assets.
Get in touch and let’s discuss what you need! We can tailor a support solution that meets your specific needs.