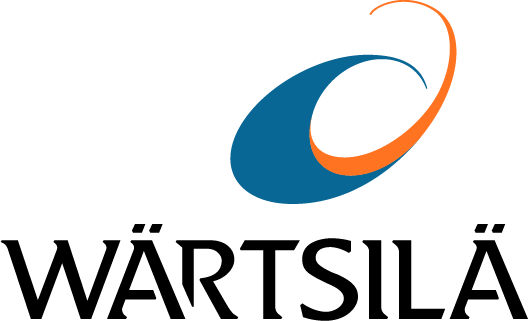
You just spent a lot of money buying a car you care about and now you need to choose a garage to take it for its annual service – do you go for the cheaper option of your local one-man workshop, or do you spend a little extra with the manufacturer’s authorised dealer network to ensure that your expensive investment is properly protected? If you prefer the second option, you probably also recognise the value of spending a little more to have your vessel serviced by a provider that guarantees reliable quality and expertise. Long term you know it’s the most cost-effective way to optimise performance, minimise downtime and maximise equipment lifetime.
Choosing third-party suppliers is a bit like going for the cheaper local mechanic to service the shiny new set of wheels sitting proudly in your driveway – the initial savings can be appealing, but they come with a greater risk of issues occurring in the future, requiring additional outlay and potentially leading to more serious problems such as engine failure or challenges with insurance. On the other hand, choosing Wärtsilä guarantees reliable service with high-quality OEM parts to ensure reliability, the best cost efficiency from a total-cost-of-ownership perspective and peace of mind.
It all starts with the inspection. When looking for signs of wear and tear, OEM experts and superintendents are well aware of how each part behaves and what to look out for. They also have the expertise and qualifications to say when a new part isn’t necessarily needed, to recommend when a part can be reconditioned rather than replaced and to spot issues that can be handled at the same time as the overhaul to minimise costs and downtime. As Henny Steenwinkel, Superintendent (Commissioning) at Wärtsilä says, “Preparation is everything.”
After a Wärtsilä inspection, the expert produces a health-check report that gives clear information on the jobs that will need doing and how urgent they are. Then, together with the customer, they plan the most cost-effective overhaul based on a comprehensive one-stop-shop offer of service and parts. As Account Manager Sebastian Dettmann explains: “Once we’ve carried out a visual inspection, taken measurements and analysed the performance data back at the office, we produce a detailed report with a traffic-light rating – operators see green, yellow and red ratings for each individual item on the front page.”
Based on the inspection, the overhaul is meticulously planned. Thanks to Wärtsilä’s global service network it can be carried out at the most convenient place and time for the vessel’s operations, whereas most third-party providers can only offer parts supply or technical support – and they only offer local coverage. Wärtsilä’s approach minimises the risk of unnecessary parts, incorrect parts, delayed parts ¬and other unwelcome surprises, so everything happens smoothly and on schedule.
On the other hand, a non-OEM provider may provide sub-optimal components such as obsolete parts or those that, although correct for the engine type in question, may be incompatible with the specific engine design and rating. This can cause serious issues that result in even more vessel downtime and significantly increase costs in the long run. “In our reports we see that for 75–80% of cases involving non-Wärtsilä parts, the target lifetime is not reached and another overhaul is needed sooner, or the equipment can even suffer damage. According to our experience, serious engine breakdowns typically happen a couple of running hours after a maintenance break that has not been carried out according to the correct procedures,” says Dettmann. “Operators for whom safety and reliability are absolutely non-negotiable choose OEM service and components without hesitation.”
Wärtsilä’s overhaul service restores the engine to its original condition, ensuring that the operator can honour contracts and reducing the likelihood of costly, time-consuming issues arising later. Because every engine has different requirements due to its service history, it’s important to understand what components it has and when they were last replaced, which is why Wärtsilä uses configuration tracking to record changes from the original design. “After the overhaul another comprehensive report is produced detailing everything – mechanical, electrical and software related – that was carried out,” explains Steenwinkel. “This allows us to maintain an accurate record of your vessel and its service history and means that when you order parts in the future they will be exactly the right ones for your installation.”
As a large company with global operations, Wärtsilä customers benefit from an extensive network of experienced engineers and product experts who are aware of the typical characteristics of different engines. Our experts are continuously trained and updated with details on component upgrades and enhancements as well as the latest service methods to ensure the performance and durability of the engines. Combined with a broad range of field data from thousands of installations, this creates a unique knowledge base that is global, in-depth and always being updated, allowing the company to constantly review and refine parts and services to ensure optimal reliability.
Many service centres employ skilled engineers, and some even ex-Wärtsilä experts, but their OEM expertise is not as up to date as our engineers’. Unable to keep up with the latest product tweaks, software developments and in-house knowledge, this can see them fall short if a product’s design has been upgraded as the parts they’re selling and recommending are no longer suitable and may result in damage and operational issues for their customers. “We’ve seen this happen with piston crowns, for example,” shares Dettmann. “The supplier reconditioned the components but wasn’t aware that the piston design had been slightly updated, meaning the crowns were no longer a perfect match.”
As the OEM, Wärtsilä is the only provider that can offer the latest component designs with unparalleled quality-control standards. While third-party operators may be able to obtain the parts from the same manufacturers, Wärtsilä provides additional value for money by providing quality testing and even modifications such as surface roughness treatments, coatings and heat treatments, meaning than the final product is superior. “Good quality components help customers sleep at night as they know they a premium-quality part that has been rigorously tested and processed before being installed,” explains Steenwinkel. “For example, for cylinder liners we use a highly precise plateau honing method to achieve a perfectly smooth surface. This ensures that the lubrication works optimally and the piston and liner never touch, which obviously extends their lifetime. This kind of additional machining process is extremely important for the durability of the parts and also their relation to fuel and lube oil consumption.”
Although taking advantage of the lower prices promised by third-party providers may seem like a no-brainer on the surface, Wärtsilä maintenance services offer both long and short-term financial advantages – and they come with even more benefits when combined with Wärtsilä Online, training and other support services.
Wärtsilä Online helps customers find exactly the right components for their equipment. “The same engine name might have different parts associated with it as well as a possible adjacent main or auxiliary engine of a similar type but with a different maintenance history. Via our online platform, customers can view their own installation and technical documentation, allowing them to see exactly which parts they need for each engine, making it impossible to order the wrong one,” explains Dettmann. Another area where Wärtsilä adds value for customers is through training, with staff regularly updated on the latest product enhancements and a constant flow of communication ensuring that the knowledge within the company is always developing. This knowledge is passed on to vessel crews by regularly shared technical bulletins and spare part notices as well as ad-hoc information sharing when issues are identified, or during formal training sessions provided by the Wärtsilä Land and Sea Academy.
“Ultimately, there’s only one way to keep a vessel constantly in optimum condition, and that is to use services and components with proven quality. While cheaper options may seem appealing, they are a false economy in the long run,” concludes Dettmann.