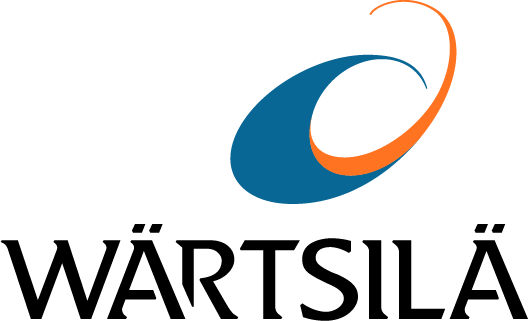
In mid-July 2020 Norwegian shipping group Solvang ASA contacted Wärtsilä about a seawater ingress into the main engine on one of its LPG tankers. The damage was worse than first suspected, and a full overhaul was required – with a turnaround
time of just nine weeks. Wärtsilä’s team worked around the clock to complete the job on schedule, helping Solvang to avoid significant lost earnings in the process.
The LPG tanker, built in 2007, was sailing in the Red Sea towards the Mediterranean Sea when a cracked pipe caused seawater to start leaking into the engine room. When the crew pumped out the water and carried out initial checks, they found that there
was around 10% of seawater inside the lube oil system. The vessel’s owner, Solvang ASA, a leading Norwegian LPG and petrochemical shipping group, contacted Wärtsilä to arrange a more thorough inspection. Mario Brych, Senior Technical
Expert at Wärtsilä, explains that the damage was more extensive than originally expected. “We were able to get someone on board quickly, and our inspection revealed that despite the short time they were exposed to seawater almost all
of the engine’s components had suffered severe corrosion damage; only a complete overhaul could return the engine to its original condition.”
“When we saw the extent of the damage, we recommended that the customer didn’t
start the engine,” says Brych. “Our first major challenge was to find a berth or shipyard that would accommodate a gas tanker in operation so that it would be ready to take a new cargo when the engine was repaired. The closest available
repair yard was in Augusta, Sicily, so it was decided that the ship should be towed there. By the end of the disassembly phase only the crankshaft was left in the engine. We used in-situ machining to remove the rust spots and re-establish its surfaces;
other components were sent to various workshops around Europe to be reconditioned.”
It was vital that the repair was carried out to a strict nine-week schedule as the vessel needed to be operational by mid-September in order to fulfil its existing contracts and avoid substantial losses. As Petter Bodman, Sales Manager at Wärtsilä,
explains, this tight timetable was made even more challenging by the new sulphur regulations that had been introduced in early 2020. “The regulations led to an increase in demand for pistons and liners, which caused delays on orders around that
time. This meant that there was no guarantee that the spare parts we needed would be in stock,” he explains. “It was also difficult to say how severe the corrosion would be on each component and therefore how long it would take to refurbish
them. The more we opened up the more we discovered, so new parts were being ordered all the way through the process. The final parts were still being ordered two or three weeks before completion.”
Bodman says that a number of
Wärtsilä employees voluntarily cancelled their holidays to make sure the refurbishment was completed on time. “Even though I was on vacation when I got the call, we were able to organise everything with the team so that the work could
begin immediately, and then I took over responsibility for the job on my return.” To expedite the process and provide service at the shortest notice possible, Wärtsilä also took a chance by sending staff to the repair site before a
firm order had been placed for the work. Another factor that added to the challenge was the fact that the entire process took place at a time when Italy was particularly hard hit by the coronavirus pandemic. “We had to send a lot of people to
the repair site, and the restrictions obviously made it harder to do the work in a timely manner,” Bodman points out.
Organising the repair was a complex process with lots of uncertainties encountered. “Some parts were purchased in the Netherlands and others from as far afield as Asia, so it was quite involved from a logistics point of view,” says Bodman.
Wärtsilä had a dedicated project manager involved throughout, which helped to keep things running smoothly. “The technical support team was invaluable too,” Bodman adds. “They provided a vital link between our field service
engineer onboard who needed a part and the back-office staff who were in charge of ensuring that exactly the right part was ordered and arrived on time. For example, they helped identify safe, reliable alternative parts for those which wouldn’t
have arrived in time.”
As well as coordinating the entire repair process and providing expertise in logistics, product management, technical support and parts availability, Wärtsilä was also able to advise the customer on preferred vendors for supplementary services
such as cleaning. Having multiple vendors for each of these areas would have made it all but impossible to complete the repair on schedule and would have resulted in a far less seamless process.
One of the most helpful aspects of
the service provided was the streamlined communication between the two parties, as Bodman explains: “We kept the customer informed at all times, maintaining continuous dialogue through daily meetings where they could follow the progress of the
project. We were constantly making judgement calls on whether to recondition existing parts or send for new ones, with every decision backed up by evidence that was presented in daily meetings. We also made detailed daily reports for the insurance
company.” This two-way communication meant that Solvang could get detailed insights and also highlight any concerns, adds Bodman: “They were committed to keeping the process highly collaborative, which helped us to keep things on track.”
“As an innovative company Solvang is committed to finding inventive solutions, so we have that in common. For a big refurbishment job of this kind, it also made sense for them to work with us as the engine OEM,” Bodman emphasises.
Despite how stressful the initial situation was, and the magnitude of the challenges involved, the project has served to strengthen the cooperation between the two organisations. “Our already good relationship has become even stronger as a result
of this project,” he says, adding: “They now tend to call us more frequently for input on smaller issues as they’ve realised that we can help them prevent similar issues arising in the future simply by keeping a watchful eye over
their vessels.”
“The team at Wärtsilä showed why it’s always best to use the original OEM for engine repairs, pulling off a really impressive job in a short space of time. With their dedication, expertise and excellent communication with our people both onboard and in the office, the repair was done within the available time window and therefore helped us mitigate a situation that could easily have had even more serious repercussions for our business operations.
- Tor Øyvind Ask, Fleet Director, Solvang ASA
Find out more about Wärtsilä 2-stroke engine services