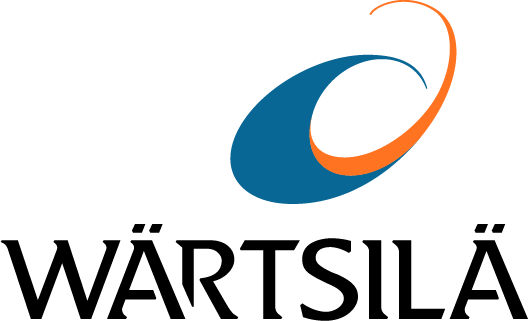
What was the last thing you printed? While for many of us it’s likely to be a work document or a pile of handouts, the research engineers at the Wärtsilä Hub for Additive Manufacturing (WHAM) has moved into another dimension – printing critical engine components and leading the way in 3D printing utilisation.
3D printing, the more well-known name for the additive manufacturing process, promises to revolutionise component production. It is already being used in industries as diverse as aerospace and healthcare and is a key element of the on-demand economy, where components are manufactured only when needed, reducing warehousing costs and cutting down delivery times. It can also make manufacturing easier, cheaper and faster, opening up the opportunity to produce components on-site, eliminating the need for transportation and therefore reducing transport-based emissions.
Additive manufacturing gains its name from the fact objects are created through the addition of material, unlike in traditional manufacturing where material is removed in milling, machining, carving or shaping processes. In 3D printing, objects are created in ultra-fine layers based on a 3D model generated using computer-aided design (CAD) or with a 3D object scanner. Each layer of plastic, carbon fibre or metal is deposited accurately by the printer in the exact shape the design requires, with the next layer fusing with the preceding one as it’s applied. One primary benefit is this allows items to be customised as needed, with 1000 variously modified components costing the same to print as 1000 identical ones.
The early adopters of 3D printing sought to benefit from lighter components, quicker production or tailored parts, but the marine industry had less need for those benefits while the price of 3D printing remained high. Now the costs are coming down and benefit more attractive to the marine sector are becoming apparent, including better-performing components, part consolidation and digitalised spare parts.
The Wärtsilä Hub for Additive Manufacturing (WHAM) has been using 3D printing on a small scale for some years now, making it a pioneer in the marine industry’s 3D printing trend. The team has plastic, carbon and metal printers in its facilities and they’re available to anyone in the company that can make use of them, widening the potential for innovation. Recognising the extensive opportunities that 3D printing offers, in 2018 WHAM began developing a regional ecosystem by cooperating with local universities. This collaboration led to a series of lectures and visits that introduced basic 3D printing technology to students, inspiring undergraduates with the goal of bringing new talent and growth to the industry. The long-term aim was to make Vaasa, where the majority of Wärtsilä’s engine design takes place, a world-class 3D printing centre, combining the skills of the industry with new academic excellence. Having 3D printing expertise in close proximity with engine design expertise also promises to accelerate innovation. “When you’re looking at a new component for an engine and trying to figure out if 3D metal printing could be the ticket, you can just go next door and push the boundaries of what is possible,” Juho Raukola, Innovation Expert at Wärtsilä explains.
The first notable success of WHAM came in 2019, with the 3D redesign of a composite lifting tool for heavy engine parts. Traditionally lifting tools are manufactured from solid steel, which is expensive and time-consuming to work with, not to mention heavy and difficult to transport. “There was some scepticism in the marketplace as to whether 3D printing could ever produce components that would be strong enough for heavy-duty engine parts,” points out Andreas Hjort, General Manager, Smart Design. “But our research and testing proved beyond a shadow of a doubt that the material is not an obstacle – in fact, 3D printing offers far more opportunities than restrictions.”
The new 3D-printed lifting tool was lighter, more compact and easier to use – and also saved up to 100,000 euros in tooling costs. It also performed perfectly, lifting a 240-kilogram engine piston on the first attempt and offering a staggering maximum capacity of 960 kilograms without deformation. Testing was carried out with the help of international certification agency Bureau Veritas, resulting in it becoming the world’s first 3D-printed CE-certified lifting tool. Local production of the tool replaced logistics chains and factory production, reducing waste and pollution and removing the wait while tools are fabricated by third-party suppliers.
The latest success for WHAM is the use of 3D printing to create a critical metal component for Wärtsilä engines that has been successfully tested at full output. Work has been done in partnership with global engineering company Etteplan, and the success of the testing clearly demonstrates that 3D printing is ready for a wider range of applications in the marine industry. “We were confident enough to put the part in the engine and the results spoke for themselves – the engine always tells the truth,” smiles Hjort. “The design freedom of 3D printing is opening up a number of opportunities to add value, in terms of both new products and improving the performance of existing ones.”
“This project has proved the power of network thinking and an ecosystem approach,” explains Giuseppe Saragò, Director in STH Manufacturing Excellence at Wärtsilä. ”Resources from different countries, 3D printer assets in our network (EOS in Finland, AMEXCI in Sweden and Additive FVG in Italy) and partners like Etteplan all had different roles and involvement at various stages of the journey, but we were all committed to the final goal. Transparency has been crucial and partnering with a network has enabled us to make quantum leaps in leveraging 3D printing. This work has also triggered some interesting and innovative new R&D projects that will once again benefit from our network, connecting several universities in Europe, partners like Etteplan and our internal resources so that expertise is shared both within our company and at an ecosystem level.”
In addition to their multinational cooperation, Etteplan and Wärtsilä are both parts of a new industrial ecosystem focusing on bringing together Finnish players in the 3D printing field. The Finnish Additive Manufacturing Ecosystem (FAME) is made up of more than 20 companies as founding members, with the aim of supporting Finland’s trajectory to becoming a world-leading country for 3D printing utilisation, sales and know-how, with 5% of the global printing market by 2030.
“Increasing the amount of 3D printing will reduce energy use and emissions, taking global manufacturing in a far more sustainable direction,” says Raukola. “WHAM has been at the forefront of this trend and it is our aim to continue to bring our customers ground-breaking, customised 3D-printed parts that save money, reduce lead times and remove the requirements for warehousing and transport. If this sounds like something you could benefit from, do not hesitate to get in touch with us.”