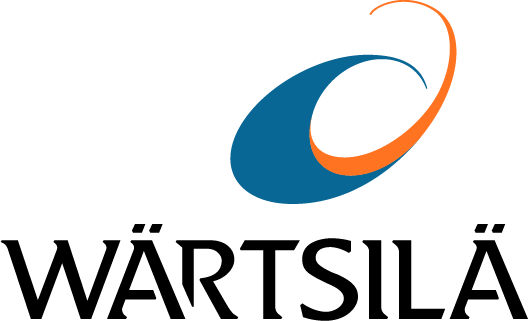
For Maersk Drilling, winning a one-well contract in the Dutch North Sea meant some serious equipment upgrade work would be required to meet an exacting set of environmental standards. The company partnered with Wärtsilä to install NOx reducers
and upgrade the UNIC engine control system on its harsh-environment jack-up rig Maersk Resolute.
Even to a layperson, the name ‘North Sea’ conjures up visions of stormy skies and huge waves. The Maersk Resolute was designed to operate in exactly this kind of harsh environment. Built in 2008, this high-efficiency jack-up rig can operate
in water 350 feet deep and drill to a depth of 30,000 feet.
“This is a highly regulated field,” says Kenneth Bang, Senior Service Account Manager, Offshore Oil & Gas at Wärtsilä Denmark. “Europe has the toughest
environmental standards in the world for offshore work, meaning you can’t operate older rigs in the region without equipment upgrades or running alternative fuels.”
In 2020, a one-well contract in the Dutch North Sea was announced.
In order to secure the contract, the winning bidder would need to demonstrate that their drilling operation could comply with the strict environmental standards set out by the Dutch authorities. A particular requirement was extremely low nitrogen
oxide (NOx) emissions.
Nitrogen oxides (NOx) are greenhouse gases that also contribute to the formation of smog and acid rain. Although they occur naturally, a major source of NOx is burning hydrocarbons as fuel. The International Maritime Organization’s (IMO) Tier III standards on NOx call for a 90% reduction in emissions from 1999 levels. Jack-up rigs also have to comply with the environmental standards that individual countries set out when granting oil companies approval to drill.
In order to comply with the Dutch regulations a significant reduction in NOx emissions was stipulated for the contract Maersk Drilling was bidding for.
“A five per cent reduction doesn’t sound like that much, but when it’s that last five per cent, achieving it is actually a huge challenge,” Bang points out. “Our standard solutions are designed to meet IMO regulations, so for this case we needed to develop something non-standard that would exceed the requirements.”
Maersk Drilling approached Wärtsilä, who suggested their high-efficiency Wärtsilä NOx Reducer. This solution uses proven selective catalytic reduction (SCR) technology, injecting urea into the exhaust gas to convert NOx into harmless
water and nitrogen. The Wärtsilä NOx Reducer is compact and flexible, and can be used with distillate and heavy fuel oils. It can also be combined with silencers and SOx scrubber systems and has been optimised and validated with Wärtsilä
medium-speed engines, such as the four Wärtsilä 8L26 diesel engines onboard the Maersk Resolute.
“One of the challenges we faced was the way engines are used on jack-up rigs,” Bang continues. “A typical
vessel cruises with its engines at a constant moderate speed, which makes using SCR technology straightforward. But a jack-up drilling rig normally has its engines running either at full speed or at very low load – as the drilling operation
results in continuous, rapid load steps. The more you push the engines the more NOx is produced, and it all has to be captured regardless of load. You have to be compliant 100% of the time; if you’re not, the operation can be shut down,”
explains Bang.
And while the engines react quickly to being powered up or down, the speed of the chemical reactions that occur in the SCR reactor is harder to control.
“To speed up the reaction you basically need
to add more urea, but it’s not that simple,” Bang explains. “We had to take ammonia slip into account, which happens when urea passes through the SCR chamber unreacted. This can happen when too much ammonia is added, when temperatures
are too low, or when the catalyst has degraded.”
The project team used computational fluid dynamics modelling to prove the concept was possible before moving forward with laboratory testing in Finland and finally going live onboard
the Resolute.
Maersk Drilling estimate they have reduced NOx emissions by 98%, exceeding even the tough Dutch North Sea requirements.
NOx reducers have to work in perfect harmony with a rig’s engine control system. The system onboard the Maersk Resolute needed to be updated to be able to control the temperature of the exhaust gas entering the SCR system. Wärtsilä performed
an upgrade to its Unified Controls (UNIC) engine control system, which is specially designed for harsh marine applications. This upgrade optimised the whole system to ensure it would run safely, reliably and efficiently.
“This was
a great co-development project to enhance the performance and credentials of what was already a truly world-class rig. Maersk Resolute is one of only a few rigs of this size with such low NOx emissions, and if it can work here, under these demanding
requirements, it has a good head start in terms of being able to operate in other strictly regulated areas,” says Bang. Indeed, when the initial project was completed, the rig moved straight on to a two-well contract with another customer in
the Netherlands. “As more companies strive to improve sustainability throughout their entire supply chains, these kinds of stipulations may well become more common and expanded to other seas around the world,” he concludes.
Find out more about Wärtsilä lifecycle upgrades.