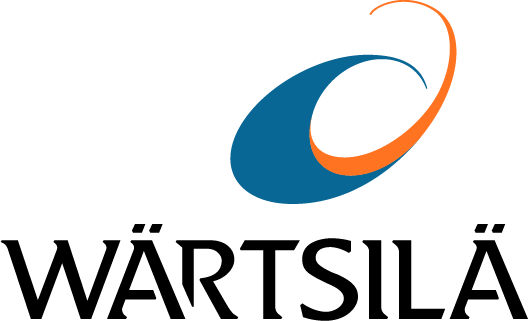
A new form of waste heat recovery plant for ships has successfully confirmed its benefits as an environmentally-clean solution to reducing ships’ fuel consumption. The plant is installed in the 7000 TEU containership “Gudrun Mærsk” which entered service in June 2005. During seatrials and in operation, the performance of the plant has exceeded expectations.
The waste heat recovery plant has been developed in a joint effort headed and integrated by Odense Steel Shipyard Ltd in cooperation with Wärtsilä Corporation, Siemens AG, Peter Brotherhood Ltd and Aalborg Industries Ltd.
The waste heat recovery plant follows the well-established concept of passing the exhaust gases of the ship’s main engine through an exhaust-gas economiser to generate steam for a turbine-driven generator.
This concept has been developed further by maximising the quantity of energy that can be recovered from the exhaust gases. This is achieved by adapting the engine to the lower air intake temperatures that are available by drawing intake air from outside the ship (ambient air) instead of from the ship’s engine room. The engine turbochargers are matched for the lower air intake temperatures thereby increasing the exhaust energy.
At the same time, today’s high-efficiency turbochargers have surplus capacity at the engine’s upper load range when matched for ambient air intake. Thus about 10% of the engine’s exhaust gas flow can be branched off to drive a power turbine which is incorporated in the turbogenerator package.
The overall result of the new concept is that the quantity of energy recoverable in an exhaust-gas economiser and in the power turbine is increased without affecting the air flow through the engine. There is thus no increase in the thermal loading of the engine and there is no adverse effect on engine reliability.
Heat is also recovered from the engine’s scavenge air and jacket cooling water for feedwater heating. The scavenge air coolers are designed in such a way that the boiler feed water can be heated close to the evaporation temperature.
The generated electrical power is employed to assist ship propulsion or for supplying shipboard services. Such waste heat recovery plants can provide electrical outputs up to about 12% of the engine power.
The generated power thus contributes significant savings in both fuel costs and overall exhaust-gas emissions, such as CO2, NOX, SOX, etc. It is the only technology commercially available today that reduces both fuel consumption and exhaust emissions at the same time.
The payback time would depend upon the installation design and bunker fuel prices, but should in general be less than five years. The increasing fuel prices make the plant more attractive.
The main parts of the waste heat recovery plant were supplied by Siemens AG, Peter Brotherhood Ltd, and Aalborg Industries A/S while Wärtsilä, as designer and licensor of Sulzer low-speed engines, co-operated in engineering and developing the waste heat recovery plant.
The vessel is propelled by a Sulzer 12RT-flex96C low-speed common-rail engine with a maximum continuous power output of 68,640 kW at 102 rpm. Exhaust gases pass through an
The vessel is also equipped with three eight-cylinder Wärtsilä 32 generating sets with a combined electrical output of 11.2 MWe.
The calculated output of the turbogenerator set was based upon ISO standard reference conditions which include an ambient temperature of 25°C. During the sea trials, this performance was exceeded as such output was already achieved at the ambient temperature of 14°C.
Since delivery the waste heat recovery plant has operated fully satisfactorily.
Media contacts:
Marit Holmlund-Sund
Public Relations Manager
Wärtsilä Corporation
Direct tel: +358 10 709 1439
e-mail: marit.holmlund-sund@wartsila.com
Internet: www.wartsila.com
Heinrich Schmid
General Manager, Application Development
Wärtsilä Switzerland Ltd
Direct tel: +41 52 262 44 74
e-mail: heinrich.schmid@wartsila.com
Internet: www.wartsila.com
Kay Tigges
Marine Solutions
Siemens AG
Direct tel: +49 40 2889-3263
e-mail: kay.tigges@siemens.com
Internet: www.industry.siemens.com/marine/
Peter Brotherhood Ltd
Direct tel: +44 17 33 29 23 30
e-mail: calake@peterbrotherhood.co.uk
Internet: www.peterbrotherhood.co.uk
Ole
General Manager
Marine Boilers Industries A/S
Direct tel: +45 99 30 44 75
Visit Wärtsilä at NEVA exhibition in