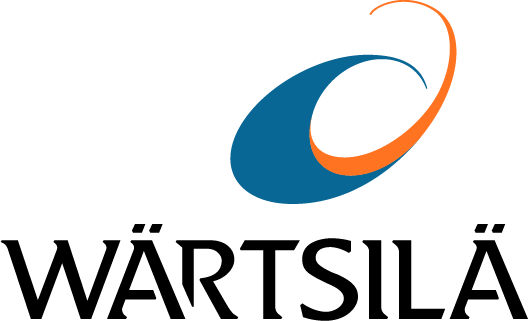
Invasive species devastating the marine environment: we can find dramatic examples all around the world! Unfortunately, ballasting and deballasting practices of the past have contributed to this. At Wärtsilä Water & Waste we believe that the most effective way to stop the spread of ballast water invasive species is to prevent their introduction.
To accomplish this, our team of engineers has developed two lines of Aquarius Ballast Water Management Systems (BWMS) that enable our customers to meet their global ballast water discharge regulatory obligations. Both of our technical solutions - one based on filter UV and the other on filter side stream electro-chlorination (EC) - have achieved IMO and USCG (type) approvals. Both technologies hold several class and hazardous area approvals and guarantee maximum flexibility and choice to our customer.
Keep the ships green and the oceans blue with Wärtsilä Aquarius BWMS
Our simple, six step solution to help meet legislation and reduce your impact on the marine environment. What at first appears to be complex, risky and costly is made feasible by our solution.
Thanks to our engineering capabilities, we work with you from the very first enquiry right through to the successful delivery and installation of the system, providing ongoing product lifecycle support. Our project execution capacity makes us one of few partners offering a complete scope. Our retrofitting options range from equipment only to complete engineering, procurement and construction projects.
As the entire scope is offered by one partner, the quality, efficiency, communication, flexibility and integration are improved. Wärtsilä provides an integrated solution, with extensive experience in project management and delivery execution.
Required by IMO. The International Maritime Organisation (IMO) introduced in 2004 the Ballast Water Code (BWC) to address the Control and Treatment of Ships’ Ballast Water and Sediments for all sea going ships greater than 400 gt using ballast water. The Ballast Water Management Convention (BWMC) entered into force 8 September 2017. Ships are required to manage their ballast tanks to remove or render harmless the ballast water discharge of invasive species.
Our experience and knowledge about ships and marine engineering allow us to have a better understanding of the environment in which the Ballast Water Treatment System is going to be installed. With our technical assessment of BWTS for your specific vessel, we are capable of showing potential equipment locations, installation paths, electrical cabinet locations, and make recommendations for what should be considered during installation. Understanding that equipment operations are essential, and that problems and down time have an effect on the owners bottom line. We believe that a single supplier for the entire design process, equipment supply and installation support is beneficial to the ship owner both in terms of cost and efficiency. Communication across different disciplines is proven more efficient when exchanged within the same company.
Fully ATEX approved: Wärtsilä’s market leading ATEX and hazardous area installation design was custom made to meet the vessel design requirements.
ISO certified ship designer: Management system certificate – Ship design and engineering services for the global maritime industry.
For NEWBUILD & RETROFITS,
please contact +44 1202 662 600 or waw.sales@wartsila.com
For SPARE PARTS, please
e-mail us with the Equipment Serial Number or the name of the vessel at pse@wartsila.com. For urgent support,
contact +44 1202 662 693
For TECHNICAL
SUPPORT & SERVICE, please email us with the Equipment
Serial Number or the name of the vessel at poole.service@wartsila.com. For
urgent support, contact +44 1202 662 693.
Equipment Serial Number is taken from the equipment
nameplate and includes all letters and numbers as given on the equipment
nameplate.