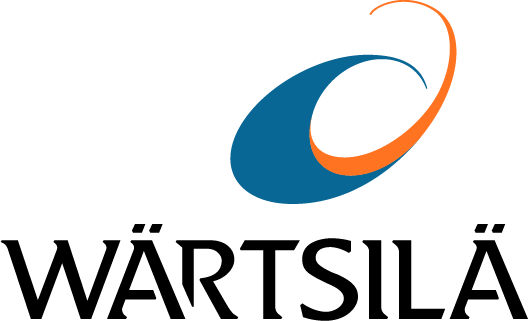
Fishing vessels can be designed to minimize both their fuel consumption and their environmental footprint. One method used to achieve this is to analyse the vessel’s sailing pattern and incorporate the results into the hull, propeller and nozzle design.
Traditionally, hydrodynamic tests are performed in a tank using a small scale model of a ship. The behaviour and performance of the model predict the performance of the real vessel. By analysing the interaction between the hull, propeller and nozzle, an estimate is made regarding the overall efficiency and environmental impact. This model-scale testing takes time and, in the case of nozzles, is never completely accurate.
With the recent development of the Computational Fluid Dynamics (CFD) science, it is now possible to predict the overall propulsion performance of the vessel and to recommend potential areas for efficiency improvements. Wärtsilä's expertise in hydrodynamics is the product of decades of experience working alongside ship designers. With our in-house knowledge and skills in hydrodynamics and CFD simulations, we can offer hydrodynamic insights that cost less and are available faster than what is possible with model testing.
The use of numerical flow simulations (based on CFD) in maritime industry applications has become increasingly relevant in recent years. Thanks to accurate calculations of the flow field, the propeller design can be fine-tuned to achieve optimum efficiency. The CFD analysis can be extended to include the actual hull geometry, thereby replacing conventional model scale testing. Nowadays this can be carried out within commercially acceptable time and cost limitations.
CFD simulations require an accurate methodology for calculating the bare hull resistance, the open water performance of the propeller, and the self-propulsion condition. The method is sufficiently robust to handle a large range of vessel types, including fishing vessels.
Wärtsilä carried out numerical simulations of the propeller performance for a new fishing vessel built at the MacDuff Shipyard in Scotland. The accuracy of the method has been established during the validation process, where the CFD results were compared with the available experimental data. The analysis helped to secure the compatibility of the hull resistance and the propeller performance, for a range of different hull and propeller designs.
Numerical flow simulations make it possible to ‘dive’ into the virtual world and obtain a more detailed analysis of the occurring flow phenomena. This helps in identifying those areas where the largest improvements can be made in order to reach optimal performance.