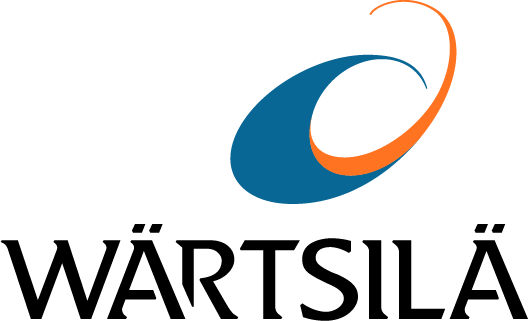
In 2019 Sapura Brazil, a company specialised in subsea services, signed a five-year Optimised Maintenance agreement with Wärtsilä for six pipe-laying support vessels (PLSVs). The aim was to increase the fleet’s availability, efficiency and reliability through a condition-based maintenance concept. Three years into the agreement and the major maintenance interval for the vessels’ thrusters has been extended forward from five to ten years and major maintenance of the engines has been postponed from 24,000 to 36,000 hours.
Minimise downtime and ensure smooth operations for two critical PLSVs
Wärtsilä Optimised Maintenance agreement including condition monitoring for engines and transverse, steerable and retractable thrusters
Improved vessel predictability, availability, reliability and profitability plus reduced risks and maintenance costs
There are few maritime activities as demanding as pipelaying. The vessels need to be in the right place at the right time and with no room for error. One small failure could cause enormous losses, so reliability is key. When Sapura needed a maintenance agreement to ensure minimum downtime and smooth operations for their critical PLSVs, they turned to Wärtsilä.
Wärtsilä’s Optimised Maintenance agreement includes condition monitoring of the Wärtsilä 32 engines as well as the Wärtsilä transverse, steerable and retractable thrusters to increase efficiency, reliability and availability while lowering operating costs.
“We’ve worked with Sapura for a number of years, so we have a good relationship,” says Arturo Cortez, Sales & Business Development, Account Manager, Wärtsilä Marine. “They wanted to make sure they had good-quality equipment and support, and we are very happy they trusted us with this important task.”
Headquartered in Rio de Janeiro, Sapura is a joint venture between Sapura Energy and Seadrill. Their PLSVs – the Diamante, Topázio, Ônix, Jade, Esmeralda and Rubi, all built between 2011 and 2014 – work in support, installation and flexible pipelaying mainly in Brazilian waters. They are responsible for making underwater connections for the offshore industry, which supplies power to millions of homes and businesses. The five largest vessels in the fleet can each hold up to 4,000 tonnes of flexible pipes and umbilicals. Unexpected work stoppages are expensive at best and catastrophic at worst, so every step is taken to avoid them.
“You can’t interrupt pipelaying. You have to know beforehand when the vessels need maintenance,” Cortez explains. “This is a challenging environment where safety, reliability and cost-efficiency are critical.”
Traditional vessel maintenance is based on time or operating hours. After five years or 24,000 hours of operation, for instance, a vessel might need major engine maintenance. The problem with this method is that it assumes the vessel needs maintenance at this particular time, not before or after. But new technological solutions can refine this method so that work is performed according to the actual condition of the equipment, making the process much more reliable and efficient.
Wärtsilä’s Propulsion Condition Monitoring Service (PCMS) keeps a close watch over the vessels’ propulsion equipment, much of which is not easy to monitor since it is underwater. This removes the need to enter drydock to partly dismount selected internal thruster components in order to visually inspect them. Instead, sensors provide real-time information about the condition of the propulsion machinery and this data is sent to the cloud where it is analysed by specialists who assess the condition of the equipment and plan the maintenance accordingly. This improves the predictability, availability, reliability and profitability of the vessels, while cutting risks and maintenance costs.
“For example, if we see a thruster begin to perform less optimally, we can take some action,” says Cortez. “If it is critical to continue operations, maybe we can reduce the load on this thruster so they can continue. This gives us a window to act before a potential breakdown occurs.”
The data provided by the PCMS and Wärtsilä’s Expert Insight service – which uses cutting-edge artificial intelligence models and advanced rule-based diagnostics to detect minor problems and ensuring they are addressed before they become major issues – are the enablers for Wärtsilä’s dynamic maintenance planning (DMP) service. DMP uses data analysis and inspections to safely prolong maintenance intervals. Analysing the data and comparing key parameters helps determine when maintenance should be performed based on the condition of the equipment.
“We were due to go into drydock in five years to overhaul the propulsion system,” says Luis Grotz, Projects and Engineering Sales Manager, Region Americas, Wärtsilä Marine. “But we created a detailed report on the condition of the equipment for the customer so that they could communicate with the classification society which maintains the technical standards for the construction and operation of vessels in this industry. Based on this information they then gave Sapura the approval to extend the interval for major thruster maintenance to ten years.” If this pattern is repeated over the vessels’ lifetime, Sapura will be spared the downtime and costs of longer drydockings.
We showed our data to the classification society which maintains the technical standards for the construction and operation of vessels in this industry, and they gave Sapura the approval to extend the interval for major thruster maintenance to ten years.
But, of course, there is more to maintenance than monitoring and planning: maintenance also needs to be carried out. Condition-based maintenance and real-time monitoring increase the safety of operations and provide the flexibility to schedule maintenance according to the actual condition of the equipment and so that it does not negatively impact a vessel’s availability. Furthermore, only necessary work is carried out and only necessary spare parts are used, saving both time and costs.
“Due to the nature of the projects our PLSVs are engaged in, any unexpected downtime is simply not an option. With Wärtsilä's expert support, we can continue to maintain our vessels to the highest standard while at the same time adding an extra layer of flexibility and cost-efficiency to our maintenance planning and execution.” Fabio Gervasio, Maintenance Manager, Sapura Brazil.
Wärtsilä was able to offer Sapura strong local support in Brazil backed by specialist know-how from all over the world with fast, competent service by people who know their business and equipment. Sapura now have a better understanding of their equipment’s condition and can more accurately predict and efficiently carry out necessary maintenance.
Find out how your operations can benefit from a Lifecycle agreement with Wärtsilä.