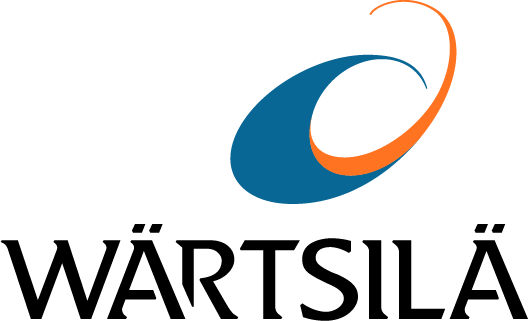
Wärtsilä has developed a modular installation system for sulphur oxide exhaust cleaning equipment that allows ship owners to continue to use same fuel as before 2020 when new sulphur regulations need to be complied – without spending time on a dry dock. This saves time and money and helps avoid a growing shortage of dry dock slots.
Originally, Wärtsilä’s modular exhaust gas cleaning system was developed for a container ship which lacked space in its engine room for the pumps and pipes required for a standard hybrid system. However, soon it was understood that fitting
the equipment in an auxiliary module on deck had more wide-ranging advantages: the system can be standardised, factory-produced, and rapidly installed without the need to enter dry dock.
As a result, Wärtsilä’s modular system
will allow ship owners to avoid the expected shortage of dry docking slots following 1 January 2020. This is the date on which the International Maritime Organization has ruled that the sulphur content of fuels used in shipping cannot exceed 0.5%.
There are an estimated 15,000 ships under the age of 10, and so suitable for being retrofitted with exhaust gas cleaning systems. Their owners are all now deciding whether to install a cleaning system and convert their engines to LNG, or pay
a premium for low sulphur fuel, making time in dry docks hard to find, particularly for large vessels.
Wärtsilä’s modular system allows customers to retrofit cleaning systems without having to secure dry dock slots or even
significantly interrupting their normal commercial operations.
The first generation of marine exhaust gas cleaning systems was installed on ferries and cruise ships, mostly operating in the Baltic Sea and North America. For these ships, inline systems used to replace the ship’s silencer were a good option,
as most had sufficient space in the engine rooms for the required pumps and piping.
These ships also often opted for open loop systems, which spray seawater into the exhaust and use the water’s natural alkalinity to strip out the
sulphur dioxide. However, open loop systems are not appropriate for vessels which need to operate in waters, such as rivers or estuaries, where there is insufficient alkalinity to strip out sulphur, or in areas where environmental regulations forbid
the discharge of acidic water.
Such vessels require a closed loop or hybrid system, where the same water can be used in a cycle, with an alkali added to keep the PH sufficiently high. As a hybrid system has various components, including
an alkali tank, several settling tanks, a residence tank, a process tank, a buffer tank, and additional pumps and piping, retrofits can be complicated.
In a traditional retrofit, this equipment is crammed into the engine
room wherever there is sufficient space, leading to a mess of pipes and cables. Wärtsilä’s system moves most of the equipment into two steel frames which can be mounted on deck. Depending on the exhaust gas cleaning equipment size
the footprint varies between 3-10 TEU.
Because Wärtsilä uses TEU-based dimensions and the same twist lock system standard for shipping containers, the prefabricated modules can be taken to where they will be installed on container
vessels or a specialised truck, and often mounted using existing container cranes at ports.
First, the owner must decide which engines in the vessel will continue to use standard heavy fuel oil, so that Wärtsilä can determine how much exhaust gas will need to have sulphur removed from it, and thus select the correct size of the cleaning
system.
Next, Wärtsilä’s audit team will define the areas that need to be 3D laser-scanned. This allows the audit team to check that there is sufficient space for the necessary equipment, which includes pumps, pipes, electrical
cabinets, connections to the ship’s main electrical switch board, and modules monitoring the quality of water taken in and discharged.
All this is necessary, because few ships can provide up-to-date drawings showing the location of
each piece of equipment in the engine room. Wärtsilä engineers use the scan to decide the layout and design the piping, which is then prefabricated and sent to the ship.
If the equipment is installed without dry-docking, the next
step is to mount the auxiliary module. A steel frame module containing pipes, pumps and tanks is lifted into place at port, and then secured in place using twist locks.
At the next port, a second module containing the exhaust gas cleaning
system itself is mounted on top of the first module, and again secured in place with twist locks.
These two module installations can be carried out with minimal off-hire time, using a riding team of installation engineers boarding the vessel
and welding the equipment to the deck while at sea, and also beginning the preparation for the pipe installation in the engine room.
The next stage is the installation of the by-pass damper and manifold, which connects the final portion of the funnel to the cleaning unit via an exhaust gas manifold. The engines cannot be operating while this is done, so this stage must be done during
loading or offloading of cargo at port.
The only part of the installation which may involve significant time off-hire is cutting a new sea chest and discharge valves into the vessel’s hull. The sea chest is needed to take in sufficient
seawater to run the system, and, depending on the size of the installation, the vessel will be fitted with between one and five discharge valves aft from all other water inlets.
This can be done either in drydock or by divers from Trident,
the Dutch company Wärtsilä acquired in December. Trident’s divers first cover the area where the sea chest is to be cut with a watertight dome, which is then inflated, allowing the necessary welds to be carried out against air, as
required by classification society rules.
To overcome hull corrosion issues caused by acid in the discharge water, Wärtsilä has developed a prefabricated safe discharge valve. This is an insert plate consisting of a collar made
of corrosion-resistant, high-quality steel, which is welded to a black steel support bracket in a workshop.
The insert plate allows a technically challenging weld, which would be very difficult to perform by divers or even in a shipyard,
to be done in laboratory conditions in a specialised workshop. Trident’s divers then weld the insert plates to the hull.
The final task is to take the water intake pipe through the engine room to its place next to the existing funnel
and connect it to the exhaust gas cleaning system. A riding team will then board the vessel to start up and commission the system.
The final design and installation concept has been completed for the ‘large’ cleaning system, which is two 20-feet containers long and four wide and has a capacity of 40MW to 60MW. It is soon to be completed for ‘small’ (1x3),
‘medium’ (2x3), and ‘extra-large’ (2x5) sizes.
As some pieces of equipment, such as electrical cabinets, are the same scale in all systems, the ‘small’ and ‘medium’ systems are more challenging.
Even with its reduced footprint, the modular system requires deck space which could otherwise carry between 21 (small) and 100 20-feet containers (extra large). However, the loss of cargo capacity is cut to a minimum, because Wärtsilä
installs the modules in cargo spaces next to the funnel, where there is often no cargo anyway as the area is so close to the main engine.
An advantage for container ships is that their decks are built to withstand loads of a similar weight
to that of the exhaust cleaning modules, and thus require no additional strengthening. The modular system also has no impact on the vessel’s wind profile or stability.
Avoiding dry-docking is particularly advantageous for large container ships, which are so large that it is difficult to book slots in suitable facilities. Avoiding dry-docking also removes the need to empty the vessel of containers, an operation that
takes several days and comes with a heavy cost.
The modular system also brings safety improvements. A conventional exhaust gas cleaning system is normally installed in the ship’s funnel, meaning the engine room is directly connected
and risks being flooded and damaged by seawater or acidic water in the event of a leakage. In the modular system, water leaks harmlessly onto the deck.
Standardising the equipment and using TEU-based dimensions and twist locks means reduced
cost and much faster delivery time.
Wärtsilä has now signed up its two first customers, the European owners of a bulk carrier and oil tanker, and there are ongoing discussions with several major container ship operators.
With Wärtsilä offering a full equipment and assembly contract, ship owners will benefit from having a single contact point and warranty.