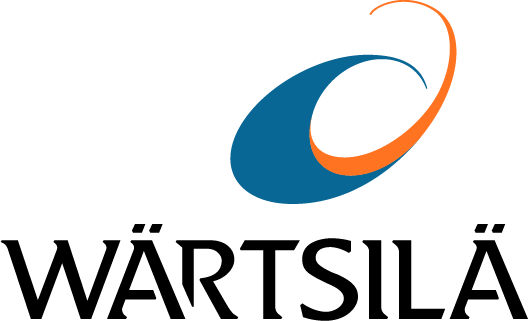
What does a remote supporter at Wärtsilä do? We give you a sneak peek into Petri Kortelainen’s day at work.
Petri Kortelainen, Superintendent, Remote Support at Wärtsilä’s Expertise Centre in Vaasa, Finland plays a vital role in Wärtsilä’s Maintenance agreements with customers which includes supporting them in operating vessels around the world – whether it be making proactive recommendations, troubleshooting or resolving problems if they occur. Thanks to his and seven other remote supporters’ analytics work, customers receive rapid, expert technical support that saves them money and keeps their vessels working at optimal condition.
“Remote support has grown because customers have been very satisfied with the fast support they get,” says Kortelainen. “The best thing to do is to work directly with customers. It gives a lot of satisfaction to be able to help the end users,” he adds.
As a remote supporter, Kortelainen’s duties are complex and versatile. Doing mechanical engineering jobs, Kortelainen has to understand all aspects of the engines being deployed on customers’ vessels. “You have to have at least a common understanding and good knowledge of ALL the items and equipment they have on board,” he says. Of course, the troubleshooting responsibility doesn’t rest on Kortelainen’s shoulders alone; he collaborates tightly with other people in his team specialising in different fields, from auxiliary equipment to control systems. “Good internal cooperation is essential for getting the exact data and solutions that we need.”
Kortelainen starts his day by taking a consultancy phone call with the remote support dejour function to check whether there are ongoing cases where he needs to jump in. Even when Kortelainen is off work, there is a dedicated remote supporter ready, 24/7, to take on any case if a customer calls. Like many other people, Kortelainen routinely checks his email to find out what else customers might have asked during the night in email management.
There, he’ll receive a message if there are any issues occurring on any of the LNG vessels owned by Wärtsilä’s customers. “If it’s an urgent case, they may call me,” he says. “I evaluate the situation and decide if urgent assistance is required. We have an online connection to engine automation system – WOIS (Wärtsilä Operators Interface System). The crew just has to switch the connection on and we can see the history trends of engines and analyse what has happened. There is also a chat messenger available for direct communication,” he says.
Kortelainen reviews the history of the data collected from the ship and proposes to the technicians on board what he thinks is causing the electrical, automation, mechanical or operational problem. “They will check the sensors and adjustments, and we re-evaluate the situation if further actions are required or it is safe to operate engines,” he says. “We can analyse the performance values of the engines and connect directly to the vessels, helping the crew troubleshoot the situation. Mainly the issues relate to electrical system or automation, which today is of advanced level.”
The electrical system can have 200 or so sensors that measure temperatures and pressures in the engines. “Let’s say one cable, one electrical wire, is broken, you can’t start the engine. It can be really challenging for the crew alone to find which cable it is. But with our knowledge we can help them solve it. And when you’ve seen the same situation many times, you gain experience and start to learn where it is.”
Looking ahead, Kortelainen says automation and electrical systems will become even more prevalent in vessel engines, and in the vessels, overall. This area requires expertise which the vessel’s crew does not necessarily have, so all kinds of remote support will be increasingly important. “Above all, remote supporters must be experts in automation.”
Before becoming a remote supporter, Kortelainen worked in a shipyard where he learned about all types of equipment used in a vessel’s engine room. At Wärtsilä, he started out commissioning, supervising, and building power plants. “I was working, hands-on, every day in the power plants, which gave me very good knowledge about how it all works. When it comes to the engines, basically it’s the same mechanical engine – let it be on shore or at sea,” he says.
Kortelainen eventually switched to Technical Customer Services providing support, troubleshooting and field testing, and mastered a variety of skills that prepared him for his job as a remote support specialist, including an expertise in automation.
“In Technical Customer Services, one really gets to know all equipment and its smallest parts in and out. When some kind of breakdown occurs in a power plant or on board, you go and analyse the cause,” he says. He suggests that remote supporters should first work in the field or on the factory floor to get the background they need. “The knowledge about engines, their parts and how they work should be very good, including automation. Then you can change to remote support.”
Still, Kortelainen’s job depends largely on his cooperation with others within Wärtsilä. “You have to have very good cooperation with different departments. We have expert technicians, and we make much effort in being proactive, in order to ensure smooth sailing for the vessels,” he says. Remote tuning is one of the latest developments. “We can have a connection to the engine control system where we modify and enhance features related to software, taking cyber security solutions into account. Customers have been very interested in this service.”
Kortelainen’s work also entails providing support to Wärtsilä’s salespeople who are selling maintenance agreements to customers. “It’s very important for the salespeople, when they visit customers, to have some technical support so they can explain and answer technically advanced questions. As I know the customers they are negotiating with, it helps me to clarify technical details for them.”
In a typical week, Kortelainen supports around 40 vessels, at least one of which will have an engine that doesn’t start. “Sometimes the solution is easy, with one broken cable to be fixed, sometimes it is about automation, or it’s a mechanical issue. Other times, the remote supporters evaluate the fuel quality and find the root cause there,” he says.
“But in my work there are of course cases where remote assistance is not the solution. In such cases we try to get someone on board as quickly as possible to solve the concern for the customer.”
Depending how far out in the ocean the vessel is located, it can take up to a week for Wärtsilä service to arrive on board. “With power plants the situation is different, it takes maybe half a day before someone is there, or one hour. But with LNG tankers, they are in the middle of the ocean so they need all the support they can get, remotely.”