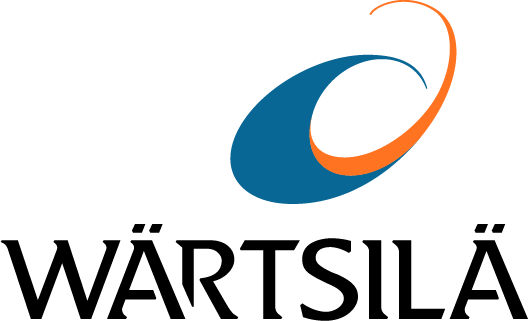
German research icebreaker finally receives new shaft generator systems – the old systems offered stellar performance for 35 years. Twentyfour7. traces its journey so far and tells you what the future holds for this beauty.
RV Polarstern is a German research icebreaker that has been braving the Arctic seas for over three decades – but the venerable “Ice Queen” is now due for a beauty treatment of sorts. The ship’s original, Wärtsilä-manufactured shaft generator systems are being upgraded – again by Wärtsilä – to feature cutting-edge PWM technology.
Owned and operated by the Alfred Wegener Institute for Polar and Marine Research (AWI) in Bremerhaven, RV Polarstern is mainly used for research in the Artic and Antarctica. It also runs supplies to the permanent manned research facilities Koldeway Station in the Arctic and Neumayer Station III in the Antarctic.
The ship has a storied past: commissioned in 1982, Polarstern was built by Howaldtswerke-Deutsche Werft in Kiel and Nobiskrug in Rendsburg. In 1991, Polarstern – assisted by the Swedish arctic icebreaker Oden – reached the North Pole as the first conventionally powered vessel. Polarstern repeated the feat exactly 10 years later, this time with USCGC Healy. She returned for a third time in 2011.
Furthermore, in October 2008, Polarstern became the first research ship ever to travel through both the Northeast Passage and the Northwest Passage in one cruise, thus circumnavigating the North Pole.
Fritz-Werner Bergmann, Senior Manager (Drives Systems) for Wärtsilä SAM Electronics GmbH, says it is quite something to operate a vessel and the installed shaft generator systems for more than 30 years – especially, as that said vessel has 310 days at sea every year, with full system operations.
“Such operation times can only be realized by using a high-quality standard for the installed components and materials,” Bergmann says. Also, for a research vessel of this type, the near-miraculous lifetime endurance is based on the high technical education of the operators on board, as well as the consistent, top-notch maintenance performed by Wärtsilä service technicians and engineers.
However, around three years ago, as the Wärtsilä technicians were performing an annual inspection of the installed components of the two shaft generator systems (port and starboard), they ran into a problem. New spare parts were needed for the shaft generator systems, but there was a very short supply of appropriate parts. The problem concentrated on spares for the control electronics (analogues technology) and for the power electronics. Wärtsilä technicians took this information to the owner, AWI, and the Institute started investigating its options: what to do next?
The role of Fritz-Werner Bergmann was to look into the different technical possibilities and present them to the owner. There were a lot of investigations carried out during the planning phase to see if the existing shaft generator can still be used or whether a technical upgrade for the new system is in the cards.
“The main problem was the 30-year-old stator winding isolation system which was not designed to withstand the higher du/dt level of the new Isolated Gate Bipolar Transistor (IGBT) converter technology,” Bergmann explains.
The owner was pleased with the performance and durability of Wärtsilä’s shaft generator systems and was interested in an upgrade. This made sense also economically, since the old thyristor technology on board didn’t feature optimal efficiency: the proposed new technology, the Pulse Width Modulated (PWM) shaft generator system, really shined in this department.
“The PWM technology has a much better efficiency factor compared with the existing thyristor technology. A typical efficiency factor for fast running PWM systems is 91%, while for a thyristor based system the efficiency is in the area of 86%,” Bergmann offers a comparison.
Bergmann’s team fully familiarised itself with the technical specifications for the selected solution and prepared a commercial calculation and the technical/ commercial offer to the owner. All this hard work materialized as a new contract to deliver the new shaft generator systems.
During all the project discussions, there was only one fixed date. “The new installed shaft generator systems must be ready for operation for the next trip to the Antarctica in the middle of December 2017,” says Bergmann