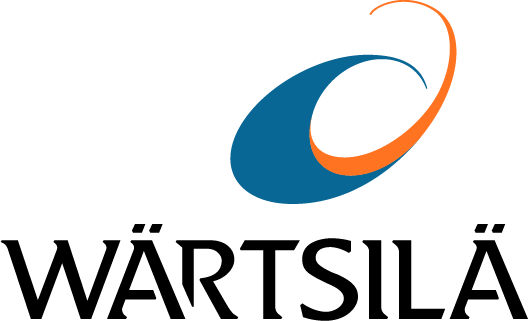
Wärtsilä Gas Solutions’ Operim has been monitoring its LNG cargo and reliquefaction plants on LNG carriers since 2011, but its new automated system is taking analysis to a new level of speed and accuracy.
Wärtsilä Gas Solutions (WGS) has introduced a technologically advanced model of its Operim solution to monitor the performance of its liquefied natural gas (LNG) cargo and reliquefaction plants on ships carrying liquefied petroleum gas (LPG) and LNG. The process captures data from the components of a ship’s plant every five minutes and sends off a file to WGS’ home base near Oslo, in Norway, for automated analysis.
With previous versions, Operim has demonstrated its usefulness in optimising plant performance with simple calculation methods and manual data sampling methods. WGS is now working with key customers to develop and implement the next version of Operim, which uses the advanced steady-state process simulators - normally used as an engineering tool to design the plant – to analyse the plant’s operations.
“Process simulators, have been used for decades in the marine industry, but the novelty is to use this engineering tool to verify the sound operation of the plant. This is done by connecting the simulator to the data feed, allowing proprietary knowledge to be applied also in the operational phase,” says Torgeir Paulsen, WGS General Manager, Aftermarket Business Unit.
Monitoring assets is vital for ships carrying liquid gas. The complex array of piping, processes, valves, compressors, and instruments in a WGS plant keeps the liquid gas at the right temperature and pressure. For LNG this is minus 161°C and for LPG it is minus 43.8°C for propane, and between -0.5 and -104 for other types of gas. The plants capture the boiled-off gas that inevitably escapes when heat comes in from the outside and re-condenses it into liquid. Without this safeguard, a large LNG carrier would lose up to six tonnes an hour of cargo on a journey from Qatar to Japan.
Using a process simulator is a more sophisticated method than the Operim version it replaces. “With the process simulator we can even obtain virtual readings from non-existing instruments, or help the operator assess whether the on board readings are within the correct range for current operating conditions. Recent improvements to technology make it much easier now to automate the process of capturing data, either by connecting to the ship’s integrated control system (IAS) through the ship’s computer, or through a small WGS computer. It’s being trialled on LPG, but will be equally relevant for LNG and most of our other products.”
The more basic ‘manual approach’ for LNG plants meant engineers at the WGS home base near Oslo had to stop work on developing new plants to cast an eye over Operim data. Now they need to be called in only when data flags up a pressure point. And there are many advantages for WGS customers, too, Paulsen says. “Automation is cost-effective and provides a lot more data than before. The biggest advantage is the speed - customers get close to real-time feedback on their processes.”
Automated analysis can help customers improve the efficiency of their organisations by uncovering the requirement for more training. The crew could even use data from their own ship as part of the training, which would be more like an interactive workshop than old-fashioned classroom tutoring. “The shorter your feedback loop is, the faster you learn,” Paulsen points out.
Ideally, data flags up issues before they even arise and ship owners take preventative measures. “The feedback loop is much faster and more instructive so it’s more likely to result in deep-rooted changes to the entire structure of the organisation. Ship operators become aware of how to run a plant more economically, more efficiently, and in an environmentally friendly way,” he adds.
The next stage in the refinement of the Operim solution is asking customers how they want the WGS data analysis to be presented to them as well as how best WGS can help them raise performance standards. WGS is in close discussions with key customers to develop Operim monitoring procedures that best serve their needs. One trial project underway with a major LPG operator, for example, assesses the data on the cargo and the reliquefaction plants to give early warnings of technical issues, in addition to improving training procedures and developing more precise fleet maintenance goals.
Operim promises to set new benchmarks.