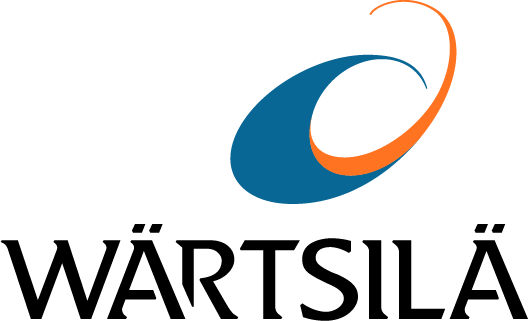
Over the last two years, unable to spend their disposable income on services, consumers have been ameliorating pandemic hardships by spending big on goods. Heightened demand has combined with Covid -related labour shortages and global unrest to create the perfect storm: a supply chain widely disrupted by congested ports, staggeringly slow offload and delivery times, and sky-high prices on freight of all kinds.
Steve Ferreira, CEO of shipping consultancy Ocean Audit, refers to it as “Containergeddon”, and he believes the heightened rate of consumer spending won’t abate any time soon.
“Major US ports like Los Angeles and Longbeach commonly have up to a six week wait to offload cargo, with trucker shortages adding further delays once goods are finally onshore,” says Ferreira. Air freight too, is completely overbooked and oversold.
Desperate to keep their goods moving, retailers are spending huge sums on freight, with some major players coming up with novel solutions to avoid congested ports.
Retail giant Amazon was one of the first to adapt. Faced with a tenfold rise in container prices in recent years, the retailer turned its hand to logistics, manufacturing its own containers in China, filling them with products, then shipping them to the US where they are then integrated into the domestic supply chain. Amazon is now self-shipping almost 75% of its packages.
“Amazon has effectively developed their own private supply chain, giving them complete flexibility,” says Ferreira.
It’s a symptom of the short-term thinking typical of the industry for decades – get from A to B as fast as possible and deal with the aftermath late.
Walmart, Ikea, Home Depot and other large, well-resourced retailers have also jumped on the self-sufficiency bandwagon, also chartering their own vessels and relying more heavily on private air freight. All this represents a paradigm shift in terms of how companies behave in the supply chain.
Yet, while these adaptations may be alleviating some stress for the major retailers and proving a windfall for freighters, such operations are massively expensive and bring their own set of problems. Smaller vessels don’t offer the same economy of scale as larger liners, and they still clog up ports. Plus, private charters often come with their own containers that can’t be easily re-integrated into the supply chain and are literally left littering the streets.
“It’s a symptom of the short-term thinking typical of the industry for decades – get from A to B as fast as possible and deal with the aftermath later,” says Ferreira. “There’s a lot of panic out there, but we need to find a way to breathe and to problem solve.”
This sentiment is echoed by Bruce Mills, Business Development Lead, Ports Global Sales Management at Wärtsilä Voyage. For him, the notoriously “pen and paper” shipping industry is changing at an unprecedented pace. With capacity issues no easy fix in the supply chain, the emphasis is on finding new ways of using data.
“There are still a lot of inefficiencies, but the past two years have shown companies that they need to digitalise, investing in new technology to be more flexible and proactive,” he says.
According to Mills, where previously companies had a ten-year plan to digitalize, even the more traditional operators have now cut that in half. Unexpected events can always impact networks, she points out, and companies are responding to global unrest and the challenges of the pandemic by building competence, hiring technical staff and engineers and a lot more analysts – a trend also noted by Ferreira.
We’re trying to make sure that the efficiencies we produce on board the vessel are also being used onshore. Without real time visibility, you can’t mitigate ripple effects that arise from supply chain disruption.
Both port and fleet technology, such as Wärtsilä Navi-Port and Fleet Optimisation Solution, are already there, working to connect a ship's navigation system to the port, enabling Just-in-time arrivals and integrating systems and communication between ships, shore offices and ports. Various other solutions are also available at different nodes in the supply chain, says Mills. However, all this can only pay dividends if the information is shared.
“We’re trying to make sure that the efficiencies we produce on board the vessel are also being used onshore. Without real time visibility, you can’t mitigate ripple effects that arise from supply chain disruption. Underlying technology will help close that gap,” he says.
While the global supply chain will always be vulnerable to upsets, both experts agree that technology and improved communication are already easing the most agile companies through such obstacles. In future, the companies that can utilise technology to communicate comprehensive real time knowledge at every step of the supply chain will be the ones that prove most resilient to pitfalls.
“There are a lot of options if importers or exporters are quick and reactive,” says Ferreira, who also emphasises internal communication as critical.
For Mills, while the adaptations made by the big players may not necessarily solve supply chain issues in the long term, they still mark a seismic shift in shipping.
“The sleeping giant is obviously much more agile than everybody used to think,” he says, “I think that’s a positive that should be recognised.”