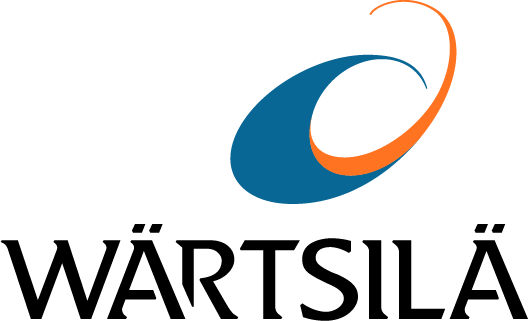
In our fourth tech talk in this series, Rune Knott, General Manager, Sales & Marketing, talks to four industry experts about gas solutions for LNG carriers. Lasse Bergerud-Wichstrøm, Sales Manager for re-liquefaction solutions at Wärtsilä,
Terje Steingrimsen, Sales Manager for inert gas systems at Wärtsilä, Karsten Kroschel, Head of Sales Marine Systems at SAACKE, and Saman Siahpoush, Business Development Manager, Wärtsilä Gas Solutions Services, share the benefits
of Wärtsilä’s Compact Reliq™ reliquefaction system, inert gas systems, boiler system and gas combustion units, and gas solutions services.
“Wärtsilä is a leading designer, developer and supplier of energy-efficient LNG boil-off gas (BOG) re-liquefaction plants, all designed to be efficient, reliable, safe, robust and flexible. Compact Reliq is one of our reliquefaction solutions.
- Lasse Wichstrøm, Sales Manager, Wärtsilä Gas Solutions
“When vessels are travelling, they generate BOG due to the heat ingress in the tanks. This compressed gas is de-superheated and reliquefied in the cryogenic heat exchanger, allowing proper BOG handling during all ship operations. The reliquefied gas is then returned to the bottom of the cargo tanks using our reversed nitrogen Brayton cycle refrigeration technology. Compact Reliq is next-generation technology that works well in all operating scenarios and, in our opinion, gives the best available flexibility.”
The main benefit is that leakages will not affect performance, and refrigerant is readily available and easy to fill correctly. It’s also easy to store onboard and is safe and non-flammable.
Reliquefaction systems aim to improve vessel performance. If auxiliary engines use less BOG to power the reliquefaction unit, more LNG will remain in the cargo tanks.
It’s about flexibility and being able to utilise the system in all operating conditions. In addition, tank pressure control can be achieved during tank cool-down, saving time and money.
“Inert gas systems made with a minimal number of rotating parts are the traditional Inert Gas System. By adding gas inlet gives the system gas combustion unit (GCU) functionality, allowing us to utilise four different modes: (1)standard inert gas (IG), (2)GCU, (3)free-flow, and (4)gas-freeing mode, which creates inert gas while burning BOG.
- Terje Steingrimsen, Sales Manager, Wärtsilä Gas Solutions
We use the same burner-scrubber, slightly larger for GCU, and when we are running the free-flow we have capacity regulation of approximately 35–100%. and Free-flow can be utilised down to 0.06barg at the gas valve. In gas-freeing mode we can also use the marine gas oil (MGO) pilot flame when burning BOG with low methane content, which reduces the methane emissions to the atmosphere. The system can run the GCU and dry-air modes in parallel. Having seawater cooling of the GCU gives the benefit of low exhaust gas temperature, approximately 15°C above seawater temperature.”
Traditional separate systems have a vertical burner, flexible to install and are delivered together with a cooler and dryer. We have also minimised the rotating parts. Traditional IG systems are seldom used, so it’s essential they work when needed.
Consequently, we have developed a self-diagnostic system with reporting to the IAS for early warning/maintenance.
If you look at it from a market perspective, you can see that yards and owners have different preferences. The cooperation allows us to deliver both separate and combined systems, reducing the number of vendors for individual vessels and giving a single
point of contact. The cooperation will also add value for the marketplace as it will encourage technical developments.
“SAACKE Marine Systems has developed a new gas combustion unit that combines a combustion unit with a modified surface burner. The GCU Evo is an evolution of our classic GCU.
- Karsten Kroschel, Head of Sales Marine Systems, Saacke
“On an LNG carrier, a GCU burns surplus boil-off gas for safety reasons. Our GCU Evo is available in six different sizes, from 0.4 to 4.5 t/h of methane, which is a burner capacity of 5.5 to 63 megawatts. The turndown ratio is 1:10, and of course
we can realize 100% free flow.
“Nowadays, vessel power consumption is a big topic. We use a burner with very low air pressure loss to reduce the number of fans, which of course also reduces the power consumption. The new GCU
Evo design has just one fan type for mixed air. There is also a failsafe control system and online diagnostics available. SAACKE also offers a typical boiler and economiser in various sizes and capacities for LNG carriers. We have a highly sophisticated
dual-fuel burner which is ready to burn alternative fuels as well.”
The GCU evo has a smaller dimension and lower power consumption than our previous classic GCU compact. We were able to change overthis by using a burner that produces a shorter flame with a lower flame temperature, which results in a reduced height of the GCU evo by several metres. Additionally, we were able to reduce the number of fans so the GCU is approximately 20% smaller and the electric power consumption is reduced by around 40%. The new design is also more modular, making installation very easy at the shipyard. Finally, 100% free flow is still possible.
Shipyards and owners are often conservative regarding new equipment, but the GCU evo is made using proven technology and systems that SAACKE has been continuously improving for many years. We delivered our first GCU for BOG applications in 2003; in 2019 we delivered our 100th GCU. We combined our experience in GCU systems with SAACKE burner systems from other applications.
SAACKE has delivered boiler systems for LNG carriers since 2004 and we already have a reasonable number of references in the market. Our burners are designed for today’s dual-fuel applications (GAS & MGO/ULSFO/MDO) as well as for alternative fuels (ammonia, methanol, etc.), which will play a big role in the future. We can proudly say our boiler systems are future proof.
“Wärtsilä Gas Solutions services has been the support partner for our product lines in the LNG business for a long time, and we have provided a number of lifecycle solutions for both inert gas generation and liquefaction systems.
- Saman Siahpoush, Business Development Manager, Wärtsilä Gas Solutions
“Our main services and packages can be divided into five main categories: maintenance management, parts supply and coordination, remote technical support, Operim® and real-time monitoring, and operator training.
“Our maintenance
management is carried out by our service delivery team in locations around the world. They support customers not only with maintenance or services onboard, but also with maintenance management and long-term maintenance planning. Parts supply and coordination
is carried out by our parts experts – they take care of the OEM spare parts supply and are also active in obsolescence management. Our technical experts take care of technical advisory, troubleshooting, process monitoring, and so on, and are
also quite active in lifecycle calculations, because they really understand our equipment from design to end of life.
“The fourth pillar of our services is digital solutions: Operim and real-time monitoring. Operim is our platform
for remote process and operation monitoring, advisory and optimisation, where we can support customers on LNG carriers on a real-time basis. Finally we have operator training, where our team of experts train and build competency with operators and
crew.”
Customers want high-performance equipment, so we design and optimise our systems to perfectly match operational demands. Customers also want availability, reliability and economic predictability. To achieve that we offer optimum lifecycle solutions with
preventive maintenance. We support our clients with equipment that is continuously served and supported by our technical experts. All equipment comes with OEM spare parts, but it also comes with something more: a detailed maintenance plan with calculations
showing what will happen in the coming years. Equipment also comes with remote process and operational monitoring, which can mean big savings for customers – we have had cases where energy consumption has been reduced by 20%. On top of this
comes our cooperation and partnership – we have always said we are sitting in the same boat as our customers; we help them to operate optimally, manage their assets smartly and build their competency with 24/7/365 availability of technical expertise.
Customers benefit from our services and solutions from day one, because the lifecycle of the product starts when we are designing the equipment. We always recommend our customers have one of our support agreements from the very beginning of their vessel’s
lifetime. This allows them to benefit from all our services, maintaining the equipment’s asset value while avoiding risks like off-hire. Together we can save fuel and maintenance costs, reduce the vessel’s environmental footprint and help
ensure smart, optimal operation.