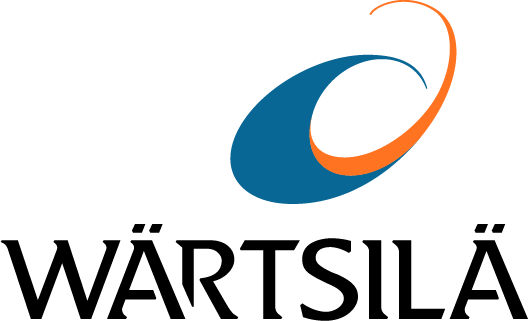
When weighing up 3D printing’s contribution to mitigating climate change, it is the stories about restoring coral ecosystems with artificial reefs or conserving honeybees with printed beehives that grab the headlines. While these are virtuous applications, there are other dimensions to consider that will have a greater impact on the environment.
It’s important to note that additive manufacturing (AM) is just a technology, not a drop-in solution that simply lightweights all products. However, substantive change will depend on optimising designs for functionality and sustainability, as well as instilling a different mindset in the next generation of design engineers.
The next step for AM, particularly from an engine perspective to support new fuels, is to embrace the freedom to design new geometries that can create products that normally can’t be achieved with castings or foundry solutions.
“In 2003, before sustainability, carbon footprints, and reaching net zero were in the mainstream, I saw that AM required less material and energy and could reach a point where products are teleported via the internet. However, most discussions were ignored then because there were more fundamental problems to solve like cost, speed, and material availability,” recalls 3D printing pioneer Avi Reichental.
Reichental, the founder, chair and CEO of Nexa3D, adds that since then, the industry has made significant progress but is still far from finished: “At Nexa3D, we consider ourselves to be on a journey. While we have integrated sustainability into our design thinking and have taken steps to minimise the use of plastics in our products, our ambitions are much greater.”
Additive printing can potentially decrease energy consumption and material content per part versus traditional approaches like Computerised Numerical Control (CNC) machining, and support the hyper-localisation of manufacturing.
“By removing the energy generated via mass production, mass transportation, mass warehousing and mass redistribution from manufacturing to the point of sale, you can significantly reduce carbon footprint generation. But there is the risk of greenwashing,” he warns, pointing to claims that a part made with additives could save X percent in energy and materials compared to a traditional approach.
“There’s still a lack of independent benchmarking with statistically meaningful data over meaningful periods. The Additive Manufacturing Green Trade Association (AMGTA) is organising benchmark studies and is unifying the way the industry acts, measures and reports, so a true picture of its environmental contributions can be gauged,” he says.
Wärtsilä’s first notable contribution to AM occurred in 2019 when a lifting tool for heavy engine parts was successfully 3D printed, replacing steel with a printed carbon fibre composite. More recently, the company opened a Sustainable Technology Hub to accelerate marine and energy decarbonisation, which is supported by a FAME (Finnish Additive Manufacturing Ecosystem) campus to further share knowledge and accelerate growth.
The last thing that manufacturing engineers and factory managers want to do is to increase risk and exposure or potentially jeopardise their yields and throughput. Therefore, it will take a few generations to fully embrace this required change in design philosophy.
Thanks to this ‘knowledge-focused’ approach, Wärtsilä has produced more than 1,500 parts printed annually for its internal manufacturing. “The next step for AM, particularly from an engine perspective to support new fuels, is to embrace the freedom to design new geometries that can create products that normally can’t be achieved with castings or foundry solutions,” explains Giuseppe Saragò, the Hub’s Director of Manufacturing Excellence.
“For example, if you simply replicate a fuel collector, which is generally a block of iron with some internal holes, using 3D printing then it probably consumed more energy than the traditional carbon-intensive approach. With AM, you can create smooth geometries that are just a spider of pipes. Focus on the design and how to produce products that are less impacting from an environmental point of view,” he underlines.
Saragò encourages Wärtsilä’s partners to bring problems that the Hub can solve, explaining that the more progress made, the better these technologies can be leveraged to make them sustainable, economically viable and affect the environment. He adds that while customers are enthusiastic about AM, some remain sceptical.
“The scepticism is mainly fed by the belief that 3D printing will reduce cost, but this is not automatic, or at least might not be the primary benefit. Customers are also concerned about whether the technology is as long-lasting as the traditional approach. In that respect, we can prove that the running hours with AM are not just comparable, but in some cases might even be more than traditional technologies,” he says.
“Manufacturing is a very conservative discipline. The last thing that manufacturing engineers and factory managers want to do is to increase risk and exposure or potentially jeopardise their yields and throughput. Therefore, it will take a few generations to fully embrace this required change in design philosophy,” observes Reichental.
Teaching future designers, engineers, and manufacturing professionals how to design for optimal sustainability and not just for optimal structural integrity is key. He notes that AM gives unlimited design complexity, such as biomimicry, for free and opens the aperture on how to improve design thinking and manufacturing execution.
“We’ve been teaching maths and science for many years, but now students must graduate with digital literacy as a basic skill and competency. Bringing it back to ‘how do you make a better planet?’, none of this happens without broadly available and transactional digital literacy skills – I would almost argue that it’s a human right.”