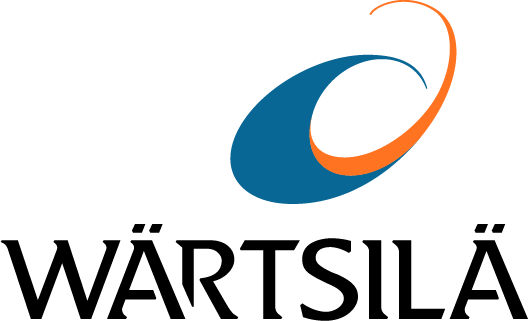
As the world faces up to growing environmental concerns and the urgent need to mitigate climate change, reducing carbon footprints and greenhouse gas (GHG) emissions has become paramount. A major energy transition is underway, and countries and regions are decarbonising their power systems.
Large amounts of renewable energy sources are being added to power systems worldwide because wind and solar do not have direct emissions and are the most affordable energy sources in most countries. Due to the intermittent nature of renewable energy sources, however, they do not provide constant power and cannot meet demand alone. To fully overcome renewable intermittency, energy systems must employ flexible solutions – from energy storage to thermal balancing – to ensure a stable and reliable power supply.
To limit global warming to 1.5 °C, global CO2 emissions should decline by 45% by 2030 in comparison to 2010 and reach net zero by 2050.
Because the energy sector plays a significant role in global GHG emissions, it is under increasing pressure to adopt technologies that can effectively reduce GHG emissions. To achieve a global net-zero energy sector, we must rethink and transform how energy is produced, transported, stored and used globally. It is obvious that this change cannot happen overnight, and the transition is a stepwise process where coal is gradually replaced by cleaner fuels like natural gas. Later, when sustainable and carbon-neutral fuels, for example hydrogen, become locally available and, crucially, affordable, they will replace natural gas.
The harmful GHGs generated by the energy sector are carbon dioxide, methane and nitrous oxide. Their environmental impact is expressed in the CO2 equivalent (CO2eq) unit, which measures the environmental impact of one tonne of these GHGs in comparison to the impact of one tonne of CO2. The direct GHG emissions of a popular aeroderivative gas turbine model and a Wärtsilä reciprocating internal combustion engine were assessed and compared using data from GT PRO®. Figure 12 presents the total CO2 equivalent emissions for an aeroderivative gas turbine and Wärtsilä engines operating at full load in simple cycle, assuming a GWP100 (Global Warming Potential with 100-year factors) scenario.
Figure 12: Greenhouse gas emissions according to GWP100 (full load at 25°and 30% relative humidity).
Direct GHG emissions from combustion engines are lower compared to aeroderivative gas turbines. Even though gas engines suffer from a small volume of fuel (methane) slip, the total GHG emissions are lower due to their significantly higher net efficiency. Wärtsilä has made significant progress in reducing methane slip, achieving an 83 per cent reduction over the past 20 years. Regardless, reducing methane slip continues to be a key focus area in Wärtsilä’s engine development programmes. Currently, the best Wärtsilä SG engines have methane emissions of 1g/kWh and Wärtsilä dual-fuel engines operating in gas mode emit 2g/kWh of methane at full load.
Figure 13: Load-dependant GHG emissions according to GWP100.
A powerplant’s carbon footprint when operating on fossil fuels consists mainly of the direct emissions from combustion and the upstream GHG emissions of the fuel. Upstream GHG emissions vary a lot based on the fuel source as they depend on how the fuel has been extracted, processed and transported to the powerplant. Reducing energy use and minimising flaring are important to lower CO2 emissions, while preventing venting and leaks is crucial for reducing upstream methane emissions.
When demonstrating life cycle GHG emissions for a powerplant in Figure 14, typical upstream GHG emissions of 10 CO2eq/MJ for natural gas and 25 CO2eq/MJ for LNG (liquified natural gas) have been used. The typical methane content of upstream GHG emissions is 30%.
Figure 14: Power plant’s lifecycle GHG emissions (carbon footprint) for natural gas and LNG.
The upstream methane emissions from well to power plant currently pose a much greater challenge than direct methane emissions from gas engine power. The upstream emissions area shared concern for all natural gas-powered power plants. However, the oil and gas sector has committed to achieving significant reductions in global anthropogenic methane emissions through initiatives like the Global Methane Pledge. By addressing upstream methane emissions, the industry aims to mitigate the environmental impact of natural gas use in power generation and other industries.
Combustion engines have higher net efficiency and better dynamic operation capabilities, and their performance is less sensitive to ambient conditions. All of these are essential factors in reducing the overall GHG burden of a balancing power plant.