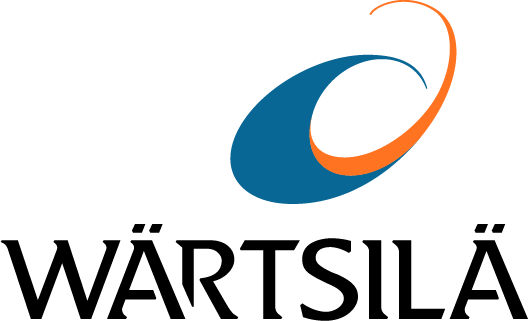
The performance of power plants at partial load has become a significant operational consideration for electric power grids worldwide, especially since operating regimes of thermal power plants are changing from pure baseload to balancing variable renewable energy. Thermal power plants are called upon to become cycling units with constantly varying load profiles that increasingly operate at part load. Thus, the part-load performance of a balancing power plant becomes a key consideration for minimising fuel cost and emissions and maximising operational flexibility. This technical comparison examines the range of output and the part-load efficiency of reciprocating internal combustion engines and aeroderivative gas turbines, and how Wärtsilä engine power plants deliver enhanced flexibility.
Part-load limitations and efficiency performance
Simple cycle gas turbines have traditionally served as peaking units because they can be started within minutes and ramped up and down relatively quickly to meet spikes in demand or changes in power system loads. However, they have lower efficiencies than combustion engines – typically less than 40 per cent even at full load – so they operate only when electricity demand peaks and the price of electricity is profitable.
With the growing need for more flexible power, continuous load-following capability becomes essential and all six of the elements of dispatchability mentioned in chapter 3 are required. Therefore, the part-load limitations and efficiency performance of combustion engines compared to aeroderivative gas turbines should be explored.
A technical constraint for part-load operation of gas turbine power plants is the minimum environmental load, also called the minimum emissions-compliant stable load. This is the lowest output at which the generating unit can operate and still meet environmental limits for nitrogen oxides (NOx) and carbon monoxide (CO) emissions. The minimum emissions-compliant stable load for most gas turbines is approximately 40 to 50 per cent of full output because operation at lower loads can result in reduced combustion temperature, less conversion of CO to CO2 and potential emissions permit violations.
To facilitate a wider gas turbine output range, turbine manufacturers have introduced control systems designed to extend emissions-compliant turndown while minimising efficiency impacts at part load. While the exact methods for turndown optimisation vary between manufacturers, the control systems typically use variable guide vanes to decrease compressor mass flow and sequential firing (reheat) to produce higher combustion temperatures at low loads. As a result, some turbine models can achieve an emissions-compliant turndown of about 40 per cent of baseload power. Site-specific conditions, including environmental permit requirements, plant configuration and post-combustion emission control systems will ultimately dictate the exact emissions-compliant turndown limit.
Aeroderivative gas turbine manufacturers boast efficiencies of approximately 40 per cent for simple cycle plants, but this is the efficiency at full, or baseload, power and under favourable conditions. However, operation at partial load and turndown limitations can restrict the flexibility of gas turbine plants. To compare the performance of a simple cycle aeroderivative gas turbine and Wärtsilä combustion engines at varying load, Figure 5 shows efficiency curves for plants operating at an ambient temperature of 25°C (77°F).
Figure 5: Single unit net efficiency at varying load level.
In simple cycle mode, the efficiency degradation of aeroderivative gas turbines is pronounced, dropping to nearly 30 per cent at 50 per cent load. Unlike gas turbines, Wärtsilä combustion engines have emissions-compliant turndown across almost the full range. The minimum load per engine can be as low as 10 per cent, making them feasible for spinning reserve markets. Engines also have an exceptional efficiency at part load as they can maintain over 40 per cent efficiency at 50 per cent load.
The discrepancy in efficiency becomes more evident when focusing on the entire plant level. When plant efficiency must be optimised while load is decreased, individual engines within the generating set are shut down to reduce output. The engines that remain operating can generate at full load, retaining high efficiency across the generating set. As a result, engine power plants provide a much wider range of output flexibility than gas turbines without the constraints of turndown limitations or an impact on efficiency.