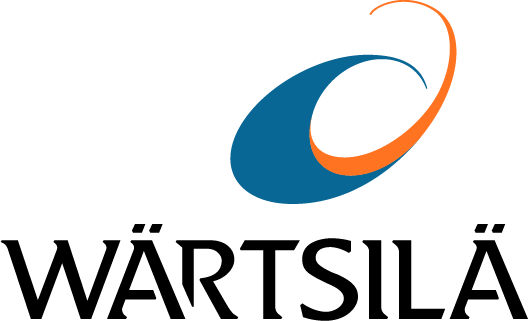
The availability of natural gas is increasing, due to the global expansion of LNG supply infrastructure, but an inflexible supply chain and fluctuating prices are causing uncertainty. Fuel shortages, supply interruptions and price constraints – even if only temporary – pose considerable risks, both economically and in terms of power supply reliability. To mitigate fuel risk, fuel flexibility is vital for ensuring a dependable source of electricity.
Temporary supply disruptions typically cause abnormal pressure drops that can result in immediate shutdowns in the worst case. A sufficient flow rate and pressure of gas fuel are necessary, and both must remain sufficiently high at all times to keep power plants in operation. Additional gas compressors can be installed to boost the gas pressure, but this increases both capital and operating expenditures. However, as Figure 10 shows, gas pressure requirements vary depending on the technology in question, so resilience to undesired changes is not equal.
Power plants that can reliably operate on a variety of gaseous or liquid fuels provide energy security in the event of fuel supply disruptions. In addition to low gas pressure requirements, Wärtsilä reciprocating internal combustion engines can instantaneously switch fuels while maintaining full output and high efficiency. This flexibility provides a key advantage over gas turbines, which have reduced availability and output when running on fuel oils, allowing engine power plants to meet evolving dispatch needs and respond quickly to changes in fuel availability.
Figure 10: Gas pressure requirements for different technologies.
Wärtsilä combustion engines are able to operate at full power with a low gas pressure of just 6 bar (87 PSI). This capability helps to mitigate the problem of gas supply disruption and facilitates flexible plant location even where the pipeline gas pressure is normally low. In contrast, aeroderivative gas turbines require significantly higher gas pressure of nearly 50 bar (725 PSI), resulting in low gas pressure-related operational issues at a much earlier stage. Due to this, aeroderivative gas turbines must be connected to the main gas pipeline to provide full output.
Gas supply may be interrupted or gas may not be available when fuel flexibility is truly needed. Liquid fuels and alternative gaseous fuels that can be used for electric power generation include liquefied petroleum gas (LPG), crude oil, residual fuel oils (RFO) and distillate fuels including light fuel oils (LFO), naphtha and diesel.
However, not all power plants are designed to run on liquid fuels for extended periods of time. When natural gas shortages result in gas turbines having to burn fuel oil as backup, the turbines require about 10 minutes to switch from baseload gas to fuel oil and additional inspection and maintenance are required, resulting in more frequent outages. Gas turbines are often advertised as having fuel flexibility, but the majority of the installed capacity operates on natural gas or LNG because of its purity and ease of combustion.
A number of Wärtsilä engine power plants were designed to operate on liquid fuels while natural gas infrastructure was being built or expanded, leveraging multi-fuel capability to meet both short-term and long-term power needs. Wärtsilä combustion engines are also designed to burn a variety of gaseous and liquid fuels without incurring increased maintenance or reducing availability.
Wärtsilä dual-fuel engines use lean-burn combustion technology when operating on gas and a normal diesel process when operating on fuel oil. Multi-fuel engines can also switch from natural gas to fuel oil instantaneously and automatically, providing an efficient reliable power supply 24/7/365. Dual-fuel capability is particularly important for island nations and areas with an insecure gas supply.
Wärtsilä is currently exploring various sustainable fuels, and an engine power plant concept running on 100 per cent hydrogen is under development. In October 2022, Wärtsilä successfully tested the capabilities of an unmodified Wärtsilä engine running on 25 per cent by volume hydrogen-blended fuel. The first engine and power plant concept operating on 100 per cent hydrogen is expected to be ready by 2026.