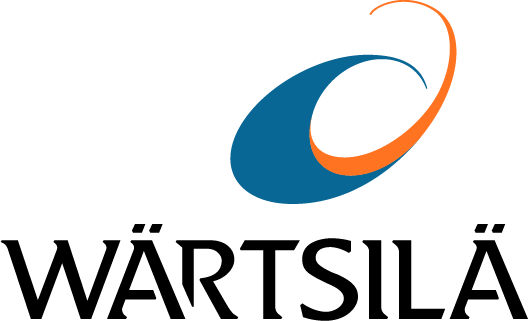
Over the course of the last century, the trend in the electric power industry had been towards increasingly larger unit sizes and plant capacities. However, due to the growing penetration of wind and solar, this “bigger is better” approach is no longer relevant. This is because of the need for more flexible on-demand power that can quickly start, ramp to full load and operate at part load.
Market experience also demonstrates that flexible gas power plants operate on varying loads for economic reasons. Interconnecting different and smaller modules offers design flexibility to meet a variety of project needs. Because generating units are incrementally sized, a wide range of plant capacities and fuel options can be created.
Modular design has been implemented for a range of generating sources, from solar farms to gas engines. Even aeroderivative gas turbines have been designed with modular architectures ranging in size from about 20 to 60 MW. However, modularity in architecture provides only limited operational modularity for aeroderivatives due to the size of the units, and the efficiency trade-offs between simple cycle and combined cycle gas turbine power plants. Popular aeroderivative models for power generation may range from 30 to 60 MW each and have high limits on the lower operating range output. This minimum load, or “turndown” percentage, is determined by emissions limit.
Reciprocating internal combustion engines are ideally suited to modular use as sets of 4–20 MW units can provide a range of incremental part-load power without sacrificing efficiency. For example, a Wärtsilä engine power plant that has 10 modular 31SG combustion engines of approximately 10 MW can deliver an output ranging from just a few MW to close to 100 MW. Operating a subset of the engines at full load to produce the desired output maintains high efficiency.
To demonstrate the benefits of a modular power plant with multiple independent units, the efficiency of an aeroderivative gas turbine plant was assessed using data from GT PRO® and an internal tool for a Wärtsilä engine power plant. Figure 4 presents the efficiency of a power plant with a maximum plant output of approximately 100 MW at varying load levels, operating at an ambient temperature of 25°C (77°F). The multi-unit plant can operate on a wide load range of 1 to 100 per cent, maintaining high plant net efficiency. In contrast, aeroderivative gas turbines are not as flexible, with a narrower load range and much lower efficiency.
Figure 4: Plant net efficiency at varying load levels.
In practical terms combustion engine power plants do not have minimum load limitations and can maintain high efficiency at partial load due to the modularity of their design, which allows a subset of the engines to be operated at full load. When plant efficiency must be optimised while load is decreased, individual engines within the generating set are quickly shut down to reduce output. The engines that remain operating can generate at full load, retaining high efficiency of the generating set. As a result, engine power plants provide a much wider range of output flexibility than gas turbine plants without the constraints of turndown limitations or efficiency impacts.
Modular engine technology also enables plants to be sited in such a way that they complement distributed renewable energy sources in areas that lack transmission infrastructure to support large power stations. This provides better matching to changing grid needs. Expanding power needs in the future can be met by adding more engine units and ancillary modules instead of constructing an entirely new plant. Combustion engine technology provides the necessary versatility and load flexibility to compensate for variable, smaller, distributed scaling of renewable sources that may only be a few megawatts.