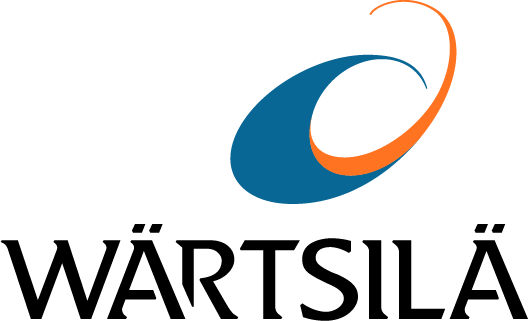
High-renewable power systems require flexible power generation capable of providing exactly the right amount of electricity output required at any given moment. Because solar and wind generation can fluctuate from minute to minute, electricity grid operators rely on power plants that can provide additional load or curtail load to mitigate the variations in renewable output. We need flexible and dispatchable balancing power plants that we can rely on.
Dispatchable energy focuses on the attributes needed to increase the flexibility and reliability of the power system. In particular, the five-minute dispatch instruction – which includes start, stop and restart – facilitates the efficient integration of larger quantities of renewables. Conversely, a slower dispatch time will result in delays to a market solution as well as market price distortions and limitations in addressing extreme voltage and frequency fluctuations.
Dispatchability can be determined by how fast a power plant can adjust its output: how fast it can start-up and reach full power, how rapidly it can ramp up, how short the minimum uptime and downtime are and how low the minimum stable load is.
The faster and more flexible attributes a technology has, the better it will be at enabling the integration of renewables into the grid. Therefore, the six elements of dispatchability are:
Table 2. The six elements of dispatchability.
Technology | Start-up time to full load (minutes) | Ramp rate (in spinning mode, %/min) | Min. uptime (minutes) | Min. downtime (minutes) | Min. stable load (emission compliant) | Plant net efficiency, LHV |
---|---|---|---|---|---|---|
Combustion engine | 2–5 | >100 | 0 | 0 | 10% | 45– 48% |
Aeroderivative gas turbine | 5–8 | 50 | 10–30 | 30–60 | 40% | 37–40% |
The chosen generating technology significantly affects the time required for a power plant to start-up and reach full load. Preheated Wärtsilä reciprocating internal combustion engine can be synchronized in 30 seconds and ramped up simultaneously to reach full output in two minutes.
In addition to a fast start-up time, engines can ramp down from 100% to 0% load within one minute. Aeroderivative gas turbines on the other hand have longer start-up times and take five to eight minutes to reach full output due to various thermomechanical constraints. Moreover, frequent start-ups may result in a maintenance penalty for aeroderivatives, and 10,000 cycle limits for key gas turbine components lead to additional maintenance when balancing renewables.
Plant net efficiency across a wide load range is an extremely important and relevant topic because load tends to vary. This topic is discussed separately in chapter 4.
Figure 3: Start-up times for different technologies.
Ramp rate is a significant parameter that determines the rate at which the power output can be changed over a specific period of time. Flexible generating units help provide stability to the electricity grid by ramping output up or down as demand, system load, and renewable output fluctuate. Aeroderivative gas turbines have a 50 per cent per minute ramp rate from spinning mode. In contrast, Wärtsilä combustion engines boast typical ramp rates of over 100 per cent per minute from spinning mode.
Minimum uptime refers to the minimum time that a power plant must operate after start-up before it can be safely shut down. Similarly, minimum downtime refers to the minimum time that must elapse after shutdown before the turbine can be safely restarted. Aeroderivative gas turbines require 10 to 30 minutes minimum uptime and 30 to 60 minutes minimum downtime, restricting their capability to react rapidly to constant balancing needs. Shorter uptime and downtime may lead to an additional maintenance penalty. Combustion engines on the other hand have no minimum uptime or downtime limitations and therefore do not incur any additional maintenance.
Lastly, a technical constraint for the partial load operation of gas turbine power plants is the minimum environmental load, also called the minimum emissions-compliant load. This is the lowest output at which the generating unit can operate stably while still meeting environmental limits for e.g. nitrogen oxide (NOx) and carbon monoxide (CO) emissions. The minimum emissions-compliant stable load for aeroderivative gas turbines is approximately 40 to 50 per cent of full output, although their technical minimum load is lower. The minimum emissions-compliant stable load for Wärtsilä combustion engines is just 10 percent.
Of the so-called flexible thermal power technologies presented above, only some megawatts are capable of addressing the variability of renewables. Combustion engine technology can perform multiple starts per day, ramping up and down quickly without any extra maintenance or degradation, making it perfect for balancing.