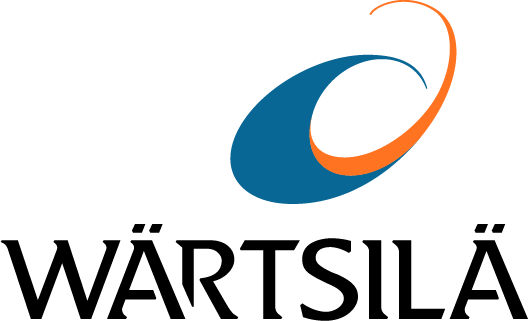
Stringent environmental legislation is starting to hit the shipping industry. The International Maritime Organization’s (IMO) Tier III regulations require ships to cut NOx emissions by 80% from the Tier I level within Emission Control Areas (ECAs) and follow a 0.5% cap on the sulphur content in fuel from 2020. These requirements will force ship owners to look beyond today’s standard solutions.
Conventional heavy fuel oil (HFO) used by marine vessels contains 3.5% sulphur, meaning ship owners must either buy expensive low sulphur fuel or install SOx scrubbers to meet the cap.
Currently, the only way for ships with diesel engines to meet the 80% reduction in NOx in emissions is to install selective catalytic reduction (SCR) units. These units will now be required in all ships with keel laying in the North American Emission Control Areas (ECA) in 2016 and in the North European ECA in 2021.
But scrubbers and SCRs increase the cost of both building and operating ships. For instance, pumps require electricity, and sludge needs to be removed in port. In addition, SCR units require maintenance.
Interest in alternative fuels is growing because of the rising cost of diesel fuel, with liquefied natural gas (LNG) looking most promising, with production increasing by 6% to 8% a year, no sulphur and low emissions.
Gas or dual-fuel engines running on gas have 25% lower CO2 emissions, while NOx emissions are 85% lower than for a diesel engine. This enables compliance with the IMO Tier III levels without the need for an SCR.
The two bottlenecks for LNG use have been bunkering availability and price. There are barely more than 100 LNG-fuelled vessels, most operating in northern Europe.
However, numbers are predicted to increase to more than 200 by 2019, and ports worldwide are showing an increased interest, which will lead to better bunkering infrastructure.
It is not easy to guess which marine fuel will dominate in the future, as it is difficult to predict fuel prices.
According to a recent report, (IMO MEPC 70/INF.6), the price spread between 0.5% sulphur fuel and 3% sulphur fuel is USD 130 per tonne, indicating that the payback time for SOx scrubbers will be short compared with running on 0.5% sulphur fuel.
SOx scrubbers or LNG are likely to be more economical in new builds than running on low sulphur fuel, even though the building costs will be higher. LNG-fuelled ships will be the most expensive to build, although costs continue to decrease as the technology becomes more mature.
We conducted a cost comparison between SOx scrubbers and LNG machinery on Kamsarmax bulk carriers (or bulkers). It showed that the initial investment cost of an LNG system is significantly higher, mainly due to the cost of the fuel system.
For the investment to be viable, operational costs must be lower than for SOx scrubbers. According to our calculations for an HFO price of 500 USD per tonne, it would be cheaper to operate on LNG given that the price is lower than USD 12.3 /mmBTU, assuming a payback period of ten years.
The corresponding LNG price for 12.3 USD/mmBTU in tonnes is approximately USD 575 tonne, but the energy content of LNG is more than 20% greater than for conventional HFO. Taking the projected fuel prices into consideration, operation on LNG looks very
attractive on a long-term basis.
Standard bulk carrier designs have a single two-stroke main engine directly connected to a fixed pitch propeller with three auxiliary gensets. Until now, the idea has been to change the two-stroke main engine and auxiliary gensets to operate on LNG.
Two-stroke engines are very static, with only one optimisation point – fully laden at service speed, although in actual operation this is often not the case. The redundancy level is not optimal with only one main engine. Gas-fuelled two-stroke engines have only been in operation since 2016, meaning they are new technology.
An optimised LNG-fuelled Kamsarmax bulker would have two four-stroke main engines for both propulsion and hotel load. Both engines are connected to a reduction gearbox, which connects to a controllable pitch propeller. Instead of auxiliary gen-sets, power take offs (PTOs) – generators connected to the gearbox – would provide electricity while sailing and in port. Each PTO is connected to a frequency converter, making it possible to run the main engines at variable speeds, lowering fuel consumption at part loads and increasing the propeller efficiency.
The main advantages of four-stroke engines are:
Proven gas engine technology. Four-stroke dual-fuel engines from Wärtsilä have been in operation since 1996 and have accumulated more than 16 million running hours.
Increased flexibility. If the larger four-stroke engine is out of operation, the vessel will still be able to keep a service speed of more than 11 km/h, which also allows for overhaul during sailing. Today´s two-stroke engines vessels would go out of operation in case of failure.
The four-stroke engines have CPP installed instead of an FPP, improving manoeuvrability. It is also possible to optimise efficiency of the engine and propeller according to the actual conditions. At variable speed, a CPP has a comparable open water efficiency to an FPP.
With the newly developed active combinator of the CPP, there is no need to apply margins, as with an FPP. This reduces fuel consumption during transit sailing because equal thrust can be achieved at more fuel-optimised propeller pitch and engine speeds. The 4-S main engines communicate with the smart propulsion control system, allowing the propeller and engine to operate in the most efficient and safe way. This is not possible with an FPP as the design is fixed and margins for worst-case scenarios have to be applied.
Cost optimisation. The four-stroke engine is more cost-efficient than a two-stroke engine, because it has lower power and is less expensive to install.
Fuel contributes a major share of the total operating expenses for a Kamsarmax bulker. The specific fuel oil consumption for a two-stroke engine is generally better than for a four-stroke engine because of the reduction gear and the CPP, but only if the hotel load is not taken into account. The use of the main engines at variable speeds to produce electricity onboard is superior to the use of small auxiliary gen-sets running at a constant speed.
It helps that the four-stroke machinery weighs about a third as much as a two-stroke engine and is significantly smaller in size. Replacing the two-stroke engine with four-stroke engines will provide a large empty space above the engines. This empty space
can be utilised for increasing the cargo capacity.
For new builds today, emissions legislation is a game changer. As the price of low sulphur fuels will most likely be high, LNG and after-treatment are both attractive options. New builds with after-treatment units are less expensive than LNG-fuelled ships, and therefore also seem to be the more attractive of the two options. The increase in LNG supply will most likely mean lower prices and few availability problems. Therefore the use of LNG as fuel is appealing in the long term, even with the higher investment costs considered.
Proven technology, increased flexibility and cost optimisation are very strong arguments for choosing four-stroke machinery over two-stroke engines for LNG-fuelled ships. The shipping industry has always been conservative as massive capital investment is required. Those who adapt will have the opportunity to earn large profits.