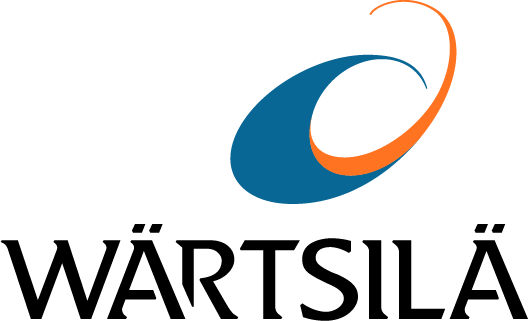
The development of the new Wärtsilä 31 engine provided the perfect opportunity to exploit the benefits of modularisation and put the concept of Design for Manufacturability into practice.
The design and development of the Wärtsilä 31 engine have presented a great opportunity to implement a design process model based on a high level of modularisation. The wide range of benefits in doing so include maintained operational excellence during manufacturing, reductions in lead time and guaranteed reliability.
“Wärtsilä 31 is a product of modularisation, which means it is based on a different architecture from previous engine platforms,” says Patrik Wägar, Product Director, Medium Bore Engines, Marine Solutions. “This enables a lot of benefits, although we need to be prepared to exploit and maintain them. This is key to enable a more flexible and less complex portfolio going forward.”
Modular product architecture means breaking down the product into property-driven building blocks – modules – with defined interfaces. “It’s a representation of a product family which consists of modules and its variants,” explains Mika Yli-Salomäki, Senior Manager Platform Architecture, Technology, Engines, Marine Solutions.
“In addition to facilitating shorter lead times from configuration to order, modular product architecture makes it easier to fit customer needs and provide high-quality, accurately validated solutions, a faster introduction of new features, and easier upgrades and conversions.”
“During the Wärtsilä 31 engine development project we secured the involvement of manufacturing experts in the design process,” says Juho Mäenpää, General Manager, Delivery Centre Vaasa Pilot Delivery Unit. “This model is what we now refer to as Design for Manufacturability (DFM), which in turn is part of our New Product Introduction process (NPI). In practice, DFM means that specific assembly and component manufacturing experts join the product development project at an early phase. They start to design how the product will be produced at the same time as the product designers are getting to work.”
Work is done at a component level by instructing the product designer to make component features in such a way that the parts are easy to produce, explains Mäenpää, eliminating the need to make technical compromises in production. If such compromises are necessary, they can be identified during the design phase. DFM also means the engine assembly structure is also developed in parallel and makes possible more extensive product preparation in the sub-assembly phase, thus speeding up the overall production process and increasing quality.
“From the point of view of DFM, when manufacturing structure and process are designed in parallel with the product, we can then also design and develop related production tooling,” says Mäenpää. “The result is faster product ramp-up and fewer changes after production has started. All this is coordinated within the NPI process for each product development. DFM allows manufacturing experts to play a part in prototype production as well as in developing the manufacturing process.”
When describing product design modularity in the context of DFM, Mäenpää likens the process to providing Lego bricks for manufacturing experts at an early stage. “First drafts for the assembly structure were made using these modules, even before the details were known of what parts each module would contain. While design modules were developed and product design was progressing, we also had the chance to influence what those details might be, up to a point.”
In general, products have traditionally been designed on the basis of performance and cost, with less focus on the manufacturing process, says Wägar. Modularisation combined with DFM makes Wärtsilä an industry leader.
“With the Wärtsilä 31 we have developed a product architecture that allows for smart modularisation whereby we can achieve more combinations using fewer variants or modules,” says Wägar. “With modularisation, you can also proceed quite far with the assembly of an engine before deciding the fuel type or specific customer needs. You can add those modules that are relevant for the project towards the end of the assembly. This approach has many benefits, but it does require close cooperation with assembly line operators and suppliers.”
The Wärtsilä 31 is the most extensively validated engine ever released by Wärtsilä.
This combined approach also passes on direct customer benefits in terms of shorter lead time, faster maintenance and fewer components. Wägar expresses satisfaction both at this potential and the fact that the same approach will be taken in developing future new products. Room for improvement still exists, he believes, in improving external modularisation, in which engine interfaces with other products can be managed.
“Fewer component variants means volume synergies, while for the assembly process it means reduced risk and shortened lead time,” says Wägar. “The core team around the new Wärtsilä 31 product has been accountable for enabling the concept, and we have also had external consultants included in the process. From any turnkey builder’s point of view, it is a benefit to have pre-engineered and pre-validated components with standardised interfaces. It moves the installation and commission risk earlier into the supply chain and increases the chances for successful commissioning trials.”
The supply chain will focus more and more on the entire process from design to user experience, and not just on the connection between companies. Wärtsilä’s focus on operational excellence will also be sharpened, eliminating process waste and strengthening connectivity between the company and its suppliers.
“From sourcing to sales, everyone needs to understand the reasons for adopting modularisation and how to utilise the benefits with this knowledge,” says Wägar. “Suppliers need to take more responsibility for delivering module variants instead of loose components, while quality processes need to be more closely aligned as well. It calls for stronger incorporation of sub-supplier processes into our own.
“We needed a new platform for further development,” he says. “The Wärtsilä 32 engine has been with us for some time, and the previous latest output stage was introduced in 2012. The new Wärtsilä 31 broke the Guinness World Record in efficiency for any 4-stroke engine, in competition with much larger engines.”
All in all, he says, it’s the engine for the digital era, in the context of self-tuning engines, self-trouble-shooting and self-adaptation. Nine engines had been sold to marine installations as of September 2017, with references ranging from icebreakers to fishing vessels. The first delivery has been made, and the first engine is scheduled to become operational in spring 2018.
Speed of innovation and technology development will only accelerate in the future, Wägar believes. Past limitations to development have been largely eliminated, while Wärtsilä’s success has always been in proportion to its focus on and investment in R&D, a factor that has delivered highly competitive products. Efficiency is always a top priority for the company, and energy efficiency has always been a key driver. The DFM approach will only serve to underline these factors.
Accuracy of simulations in design is another asset, says Wägar. “As recently as five years ago, we were still surprised at the discrepancy between simulations and reality. These days we are surprised at how accurate our simulations have become. The capacity for accurate simulations is a major value for a company.” Validation, to check that specifications meet customer needs, is also enhanced by DFM, and Wägar insists that the Wärtsilä 31 is the most extensively validated engine ever released by Wärtsilä. He sees the next step as creating a “digital twin” – a virtual engine that can be used to analyse and evaluate design and performance, without the need to construct a physical engine for these purposes.
“For other engine products on the drawing board, our DFM experiences with the Wärtsilä 31 help us develop our approach and processes to make sure we capture the synergies,” Wägar continues. “We can upgrade existing products partly using concepts from the Wärtsilä 31 development, but the main gain is for the future. For other products in our portfolio apart from engines, the journey has started, and we see great benefits for ship builders and customers for having modularised products with fixed interfaces, offering shorter lead times, reduced risk and a higher degree of pre-engineering and testing before installation.”
“This development has involved great co-operation across the organisational borders,” says Mäenpää. “Many different segments of the company have been working together to develop and introduce a great engine – in fact, the best of its kind. This way of working will increase the level of information for all parties. Of course we need to continue this work and adhere closely to the new rules we have been creating, so that we can look back on many more projects with pride at this clear product modularity.”