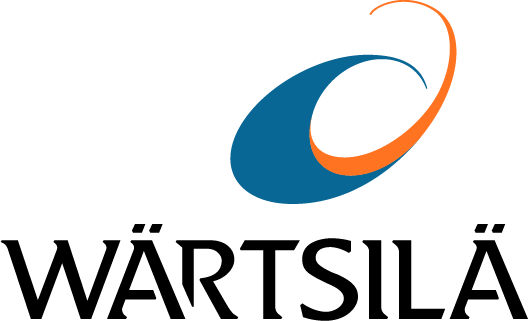
What is lightweighting and can it be used as a force for good? We take a deep dive into the subject to find out.
Lightweighting – the use of innovative lightweight materials – is proving invaluable in helping the shipping, automotive and airline industries reduce fuel consumption and lower their collective carbon footprint.
But materials like high-strength steel, carbon fibre composites, aluminium, plastic, and foam are difficult to separate at end-of-life and pose significant recycling challenges.
According to the International Energy Research Agency (IEA), the transportation sector accounts for around 20% (7.6 billion tonnes) of global carbon emissions annually.
Innovations in engine efficiency and aerodynamic design are helping reduce fuel consumption, and manufacturers are also looking at lightweighting to reduce greenhouse emissions further.
A 2004 report by Helms and Lambrecht found that a widespread move to using lightweight materials in transport manufacture could result in a global net reduction of between 660-870 million tonnes of greenhouse gases annually.
As vehicle manufacturers compete to bring end-users improved fuel economy, it is no surprise that lightweighting is a priority for the transport sector, and interest in materials like titanium, magnesium and natural bamboo is at an all-time high.
While lightweighting is lowering vehicle emissions, recycling new lightweight materials poses challenges of its own. For example, magnesium die-casting typically results in only half of the initial material going into the new part while the remainder ends up as unusable waste.
Cast and wrought aluminium can also be inefficient, yielding low-grade alloys suitable for low-performance use when recycled. However, like magnesium, they can be effectively remelted and reused. The issue here is that often they are unable to be separated from other alloys.
Recovering and separating materials is tricky, explains vehicle systems analyst engineer at Argonne National Laboratory, Jarod C Kelly: “Many lightweight materials are combined with other materials for performance reasons. So, disassembling and separation are a challenge. This can lead to contamination of each individual material’s recycling or collection stream.”
“Multi-material design creates additional challenges in several ways,” says Richard Roth, director of MIT’s Materials Systems Laboratory says. “The separation of shredded materials becomes more difficult. This is particularly true if the recycling facility can’t use simple separation techniques like magnetic separation (for steel) or flotation or other density-based solutions,” he adds.
To preserve the environmental gains from lightweighting, experts suggest looking to the circular economy – a set of design-driven principles intended to cut pollution and waste by optimising resources and keeping materials and products in use.
Kelly says more consideration could be given to circular processes much earlier in a vehicle’s lifecycle. “Knowledge of downstream challenges must be considered upfront and ideas about end-of-life and disposal considered in the initial product design. So, maybe exterior packaging is designed such that it is more easily removed via an automated process, or perhaps certain materials that present major contamination problems with each other are identified and avoided as a pairing.”
Roth adds that “some thoughts on improving materials recovery and recycling involve making it easier to separate the materials in an end-of-life vehicle, perhaps by removing more items before shredding.”
He says new markets could stimulate circular thinking in both transport manufacture and the wider economy.
“End-use markets for recycled materials vary. The secondary market for aluminium is very strong so if lightweighting involves using aluminium, there is less market concern. However, some plastics have limited secondary markets. The creation of markets for secondary materials might help offset some of the challenges with polymers, but the clean separation of materials is still a challenge,” he explains.
Measuring the environmental impact of vehicles across their lifespan involves assessing complex ecological and economic consequences and trade-offs. The lifecycle assessment (LCA) standardised in 1998 measures ecological impact across a product’s lifetime. It showed stakeholders that the environmental costs of material production and recycling were just some of the factors manufacturers needed to weigh against benefits like using lighter materials.
“Goals about circularity should address if, and by how much, circularity will improve the situation. This has become even more complicated in electric vehicles where the vehicle design and lightweighting impact the size of the battery, range of the vehicle and all of the associated challenges with securing materials for battery manufacturing,” says Roth.
“This is a complicated systems problem,” he adds, “you could inadvertently disturb the economic viability of individual players in the recycling value chain. Remove too much material prior to shredding, and the existing vehicle shredders will no longer have enough product to sell to cover their costs and might be driven out of business, resulting in a reduction of materials recovery.”
Tamara Veldboer, senior consultant, B2B circularity, Circle Economy says, “We must keep in mind potentially negative rebounds. For example, a move towards electric driving might lead to net more cars on the roads because drivers think it is a better alternative.
“We must shift our mindset towards fulfilling a need or use instead of ownership. The most important thing to keep in mind for any stakeholder working on or using circularity is that it is a means to an end – to get us back within the planetary boundaries,” Veldboer concludes.