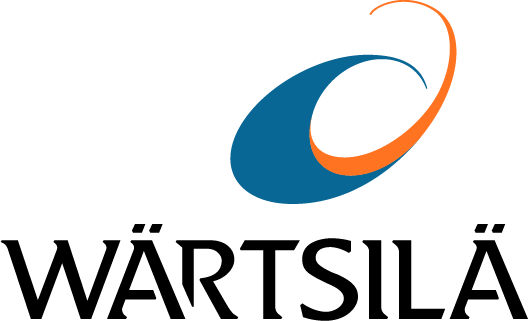
Amidst multiple downward pressures, including Covid-19 and a global increase in the oil supply, the offshore drilling industry must squeeze its existing operations for efficiency in order to compete.
With global oil prices crashing under the pressure of multiple events, including the impact of the Covid-19 outbreak, decreasing demand, and excess of supply, it is becoming more important than ever for offshore drilling owners and operators to run efficient operations. In an increasingly uncertain market, deriving value from tight operations is one way for offshore drilling companies to squeeze more value — and therefore profit — out of their rigs.
Joel Thigpen, General Manager, Global New Build Sales at Wärtsilä, defines smart drilling as the process of “making the rigs more efficient and moving people off the rig.”
In practice, these goals are realised through a few key Wärtsilä technologies, including the unmanned engine room, remote/dynamic positioning (DP), fleet operation systems, and just-in-time arrival. As a whole, these technologies can be thought of as falling into two categories: streamlining operations and removing people from operations.
Jeroen van Keep, General Manager, Business Development, Wärtsilä, points out that smart drilling is, to some extent, simply about drilling at the right spots, which is not under Wärtsilä’s control.
However, there are still ways in which Wärtsilä technologies can help make offshore drilling vessels more efficient. As an example, van Keep suggests the use of Wärtsilä technologies to “optimise the DP system in such a way that we can drill a more efficient well,” which would be useful in bring down operators’ drilling costs.
Onboard energy usage is another potential area where operators can increase savings through more efficient operations using Wärtsilä technology. According to IPIECA estimates, a diesel generator powering an offshore drilling rig can use over 20-30 m3 of diesel fuel a day, so keeping energy consumption in check is key to controlling costs on the charterer side. From the rig owner’s perspective, keeping fuel costs in check may be an important consideration in projects where higher fuel consumption would increase rig owner revenue due to owners charging handling fees over consumed fuel.
For some operators, the desire to reduce onboard energy consumption may lead to the decision to retrofit their vessels with batteries, which improve both safety and efficiency (it should be noted, however, that operators make retrofit and upgrade decisions on a case-by-case basis, so there is no universal standard as to whether or when an operator may make this decision). As more alternative fuels — such as biodiesel, ammonia, liquefied natural gas (LNG), liquefied biogas (LBG), methanol, or hydrogen — become viable, owners and operators will evaluate the cost efficiency of these new fuels and switch if it makes sense to do so.
Longevity of equipment and high-quality maintenance are two more areas where owners and operators can seek to improve operations. Ulrik Friis, Senior Business Innovation Manager, Wärtsilä, notes that with regard to OPEX costs, Wärtsilä is “getting a push on maintenance and extending the interval of our engines in general to reduce OPEX costs.”
Friis specifically notes that the Wärtsilä monitoring solution and Dynamic Maintenance Planning provide tools for operators to optimise both OPEX costs and general onboard maintenance. “It is well known that performing optimal maintenance on engines is a must to reach the lowest-possible OPEX costs and best fuel efficiency,” he says.
Traditionally, the focus has been on reducing maintenance costs by extending service intervals and reducing fuel consumption and emissions; however, these objectives aren’t necessarily aligned, as extending service intervals may increase fuel consumption due to more wear on components. Therefore, Friis observes, it is “vital to find the right solutions for customers and the drilling industry” to maintain focus on optimal operation of power generation on rigs.
In addition to cutting costs through tightened operations, offshore drilling vessel operators may also seek greater efficiency — as well as improved safety, fewer crew changes, reduced crews on global travels, and lower long-term costs — through investments that result in having fewer people on their rigs.
Reducing reliance on humans’ presence on rigs has a few key benefits for offshore drilling owners and operators: One, it reduces payroll pressure associated with having a large number of employees who must be paid on a regular basis regardless of the broader economic environment. Two, it reduces pressure to hire and retain people in the industry. This point is particularly urgent in light of the offshore drilling industry’s recent challenges with regard to attracting younger workers who are turned off by its poor image and high volatility. Three, reducing human crews improves onboard safety, as having fewer people onboard means fewer opportunities for human error and accident-related safety risks
Thigpen observes, “The [offshore drilling] industry as a whole is especially, from the latest downturn, going to be hurting for people, particularly highly skilled employees with specialized skills for advanced rigs. It has a viewpoint, from a lot of groups, as a dirty business, so younger generations don’t want to get into it. It also has volatility. When times are good, they’re really good; and when they’re bad, they’re really ugly.”
As offshore drilling vessel owners and operators plan for an increasingly uncertain future, running their rigs as efficiently as possible will become increasingly important as a means of competing in a tightening market. Keeping the operational costs of the vessels themselves and the people on them under control will be essential to navigating a stormy future for not only the oil and gas industry, but also the global economy as a whole.