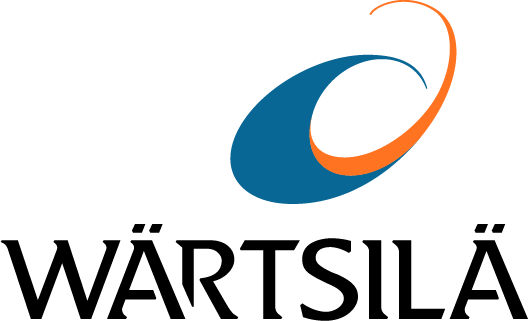
Imagine a factory where sensors talk to each other, where operations like production, logistics and distribution are handled by robots, and where the entire value chain is vertically and horizontally connected through digital technologies like the internet-of-things, big data analytics, artificial intelligence and advanced robotics. This is not a scene from a science fiction film. It’s reality.
Welcome to the age of smart factories or digital manufacturing facilities that are highly automated and designed to help improve industrial productivity, profitability, security, accuracy, and flexibility.
According to Capgemini Digital Transformation Institute’s Smart Factory survey covering 1000 senior executives of large companies across key sectors and countries spanning eight geographies across the world, in a conservative scenario, the added output to the global economy from smart factories is estimated to reach USD 500 billion annually over the next five years.
In an optimistic scenario where manufacturers accelerate their smart factory efforts and deploy or transform more than 50% of their plant base into smart factories, this number could well add up to USD 1,500 billion or 2% of the world GDP.
“Nearly half of the manufacturers in the US, France, Germany, and UK have an ongoing smart factory initiative and industrial manufacturing (67%) and aerospace and defence (62%) lead in terms of launching smart factories,” explains Amol Khadikar, Manager - Digital Transformation Institute, Capgemini.
This also means companies around the world are investing big time in ‘Industry 4.0’ or end-to-end digitisation of all physical assets and integration into digital ecosystems with value chain partners versus Industry 3.0 where they focused
on automation of single machines and processes.
According to PWC’s 2016 Global Industry 4.0 survey of over 2000 participants from nine industrial sectors, across 26 countries, industrial sectors are planning to commit USD 907 billion per annum to Industry 4.0.
A major focus of these investments will be on digital technologies like sensors or connectivity devices, and on software and applications like manufacturing execution systems. In addition, companies are investing in training employees and driving required organisational change.
According to the report, if even half of these expectations are met, Industry 4.0 will fundamentally reshape the competitive landscape and bring fundamental change to established industries.
“In general, manufacturing will become more data-driven. Increased information sharing and collaboration within the overall value chain will improve efficiency and add more value for customers. This is just the beginning of a journey and the opportunities are infinite,” says Erik Gustafsson, Business Controller at CSSC Wärtsilä Engine Co., Shanghai.
Take for instance the case of Siemens’ plant in Amberg, Germany where machines and computers handle 75% of the value chain on their own to manufacture 12 million products of the Siemens’ Simatic product line per year at a quality of 99.99885%.
Or the case of America’s largest electric power holding company, Duke Energy that deployed an asset-health monitoring and alerting system involving over 30,000 sensors and is reported to have saved nearly USD 31 million in maintenance costs in three
years’ time.
While many manufacturers take a pure ‘technology’ approach to become digital, companies like Wärtsilä are redefining ‘smart’ with its dual approach. On one hand Wärtsilä is making significant investments in future technologies like artificial intelligence, data analytics, open platforms, and block chains to create new business models and digital customer experiences. And on the other hand it is ensuring that automation and innovation are people-driven.
“Digitalisation is an opportunity to involve more people in improving the manufacturing process, and I think that smart factories of the future are those factories where the employees have together created the digital and smart solutions they use. Technologies are changing constantly, so to me digitalisation is much more about a mind-set developed in the people than about any technology itself,” explains Gustafsson.
There’s merit in that approach. According to experts, going forward, a smart factory will only be as smart as its workers. So employees working in factories of the future will need to think and act like digital natives, willing to experiment with new technologies and learn new ways of operating. Manufacturers on their part, will have to move away from being fixated on particular technologies or a fixed number of workers and instead focus on aligning productivity, profitability and innovation with higher quality of people, training & skill development.