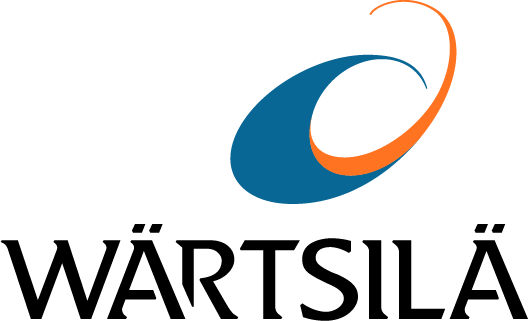
RPA is known to eliminate human error, save time, and increase speed of service. At Wärtsilä, it is based on in-house resources and involves the employees in creating the RPAs. Wärtsilä’s in-house RPA talent consists of some 30 people globally.
We met up with Hannes Hudd and Mats Holmberg to put the finger on the pulse of the RPA team. “We train employees to become what we call Citizen Developers that can do a first version of the RPA. Most of our RPA developers do not have an IT-background,” says Hudd, Development Manager at Wärtsilä Marine Solutions.
Wärtsilä makes substantial savings by not using external consultants for RPA development and avoiding custom-made features in applications where the same process can be done with RPA.
The beauty with RPA is that Wärtsilä’s RPA specialists can help anybody with a passion for efficiency and ordinary computer proficiency to create the first RPA versions of their own. It is mostly learning by doing. The most important thing is that you know the working process inside and out. Wärtsilä uses the concept of MVP, Minimum Viable Product, and also a model for the step-by-step process descriptions.
“This means that the process must be described in such detail that you can hand it over to a person that is not familiar with the process and he or she can perform the tasks without asking any questions. Then we can automate the process based on that,” explains Holmberg, Development Engineer at Wärtsilä Energy Solutions.
Wärtsilä’s approach is to decentralise RPA development and bring it down in the organisation. Involving the employees in the development work is vital for a good result. They are the ones who know how the work is actually done.
Even though no specific skills are needed, both Hudd and Holmberg emphasise the importance of a thorough quality assurance. “Before we set the RPA robot to run, centralised, skilled programmers check every sequence and run several tests outside the live environment to avoid errors and achieve a stable RPA,” says Hudd.
Mats Holmberg, Development Engineer at Wärtsilä Energy Solutions and Hannes Hudd, Development Manager at Wärtsilä Marine Solutions.
The teams at Wärtsilä’s businesses and functions have automated more than 100 processes and counting. They range from simple RPAs to more complex ones – RPA has become quite a helping hand.
By freeing up time, RPA helps Wärtsilä achieve one of its core values – customer centricity. After the employees have seen the results from the RPAs, they are convinced that RPA will benefit both themselves and the customer. What it all boils down to in the end is getting more time to spend serving the customer. “People have been grateful for not having to do the same tedious routines anymore and focus instead on things that add more value to the business,” says Hudd.
Holmberg adds that RPA can also enable whole new processes. “Let’s say there are certain time-consuming, manual steps required for a new, value-adding process, but there is no time to do it. Then you can use RPA to perform those steps to create the new process without increasing the headcount.”
The RPA team talents, Hannes and Mats, see a future where Artificial Intelligence (AI) becomes part of RPA development; where AI is the thinker and RPA is the doer. AI is, however, much more complex and requires heftier investments, which affects its return on investment (ROI).
Today, we can establish the fact that RPA can be extremely valuable in any business and any function. It is just a matter of identifying the right areas. Boring, repetitive tasks can be found everywhere. RPA has very low investment costs, the ROI is very fast, and the benefits and savings are high. “Let the people do what they are good at and let the robot do what it is good at,” Hudd and Holmberg conclude.