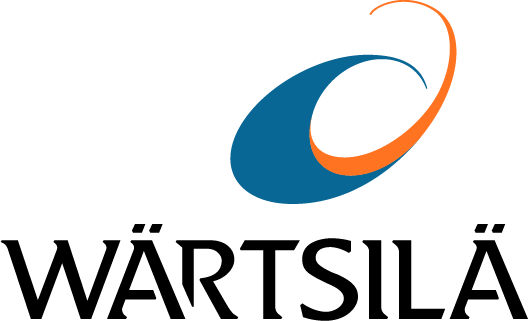
This article was original published by Bunkerspot in May 2023.
Exhaust gas abatement systems have moved beyond SOx, modernising into a platform from which multiple technologies work in tandem in the stack, including tackling CO2 with CCS-Ready Scrubbers and fully integrated carbon capture and storage (CCS) units in future. Wärtsilä Exhaust Treatment’s Director, Sales Kashif Javaid, shares insight on current the scrubber retrofit landscape and its position in shipping’s decarbonisation trajectory.
As the shipping industry continues to strive to balance compliance with profitability – while, at the same time as intensified pressure on improving sustainability - it is critical to also ensure that existing ships are dealt with properly on the path to decarbonisation.
It will be too expensive and logistically unfeasible to recycle and replace the current merchant fleet wholesale, and many vessels built 10 years ago may have to last through to 2035 or possibly beyond, dealing with considerable regulatory change in the interim period.
Instead of replacing these vessels, adopting proven technology makes it possible for the existing fleet to avoid an early grave and remain seaborne for years. Yet, to remain competitive, now is the time to invest as hesitation could be costly.
Favourable economics towards scrubbers create a strong case for implementing a retrofit strategy. As has been well documented, ship owners who invested in scrubbers prior to the 2020 Global Sulphur Cap are enjoying a competitive advantage. There are few signs that this will abate, with payback models demonstrating currently that returns can be made in months, which creates a huge driver for continual uptake of exhaust gas abatement solutions.
Given the ongoing macroeconomic volatility and widening spread between prices of high and low sulphur fuels, the financial benefits are here to stay for the foreseeable future. Add to the mix the cost of new, reduced density, low-carbon, alternative fuels and the benefits of scrubbing look set to remains for decades.
Beyond tackling SOx, scrubbers have now become a platform from which multiple technologies are working together in the stack and throughout the exhaust chain. This includes tackling NOx emissions by adding selective catalytic reduction systems (SCR) or exhaust gas recirculation systems (EGR) to ensure compliance with MARPOL Tier III requirements. In addition, scrubbers can reduce Particulate Matter (PM) 2.5 levels below even standard land-based requirements and a filter can be applied to capture microplastics.
Most excitingly, scrubbers can now provide the basis of carbon capture and storage systems – underlining the modern scrubber’s position as a multi-use technology platform. With the International Maritime Organisation’s (IMO) CO2 reduction timelines set for 2030 and 2050, and the European Union’s (EU) ETS putting a price on CO2 from ships from 2024, low-carbon, alternative fuels will represent only a small single digit fraction of the global fleet’s fuel of choice over the next decade.
As these future fuels come online, ‘CCS- ready’ scrubbers offer the first building block as they allow for an efficient retrofit of a CCS system once the technology has matured further. Retrofitting a CCS-ready scrubber today will require space to be reserved above it and the funnel to be raised a few metres, and in most cases, it is better to do this as early as possible.
Optimising the scrubber retrofit timeline
For scrubber retrofits, its common practise for ship owners to work with experienced engineering partners to make critical decisions around design and integration in a time period as short as only four weeks after contract signing. This is when the equipment, piping and possible tanks are modelled, and decisions around preferences, such as tank locations, to ensure the design process is straightforward, are made.
Minimising off-hire time at this stage of the retrofit process is critical; matching design time with the production of equipment will optimise the timing and location of the retrofit to minimise vessel downtime. A first 2D layout-drawing provides owners with an understanding of the scope of the installation and enables space to be reserved. A full technical feasibility study can then be undertaken before or after contract signing.
In our experience, best practise is having the shipyard do the detailed design to ensure a smooth and fast process that avoids confusion during installation at drydock. Co-operation between the basic and detailed designer is important though, and a good scrubber manufacturer will act as a link between all parties. In some cases, it is personal relationships and prudent communication skills more than the contract that can ensure positive, timely outcomes.
If an owner opts for our CCS-ready scrubber, we can perform additional design and engineering work to ensure that future retrofits for a full CCS system on the vessels have already been accounted for either during the newbuilding or scrubber retrofitting stage.
Additional measures are taken to ensure adequate space for the future installation of CCS system, such as minimising idle load, optimising utilities, and preparing the control and automation system accordingly.
By adopting our CCS-Ready module, ship owners can be assured that they will have continued regulatory compliance for SOx emissions and a enable smooth CCS-system adoption in the future. We have already received our first order for CCS-Ready Scrubbers, which reinforces the technical and commercial viability of CCS.
As a mature technology with a strong return on investment, scrubbers – with the possibility to be CCS-ready today – will enable ship owners to futureproof their assets and meet compliance. All this should give the industry optimism that existing solutions can help sup- port the latest regulations, including carbon intensity indicator (CII) and energy efficiency existing ship index (EEXI), and prepare for carbon pricing further down the road towards 2030 and 2050. Embracing proven technology that can bridge the gap between current and future environmental regulations will enable the industry to move forward optimistically.