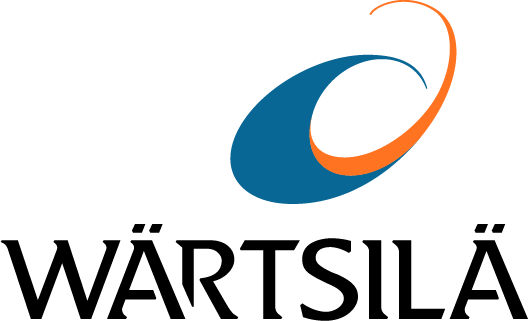
Massimo Zollia is a happy man. As a General Manager for Order Intake and Capacity Planning in Trieste, Italy, one would think he has a lot on his plate. Well, he does. This includes picking his kids from the football training and spending quality time with his family among other things. This, even as his team functions with maximum efficiency – meeting deadlines and deliveries well before time. Thanks to Operational Excellence.
"It all started in 2016," says Zollia remembering clearly his team's initial reaction of surprise when he introduced Operational Excellence within his department. Soon this new development was to become a way of life at Trieste.
While at the heart of this methodology is value for the customer, it is a holistic approach, which had a positive impact on the overall functioning and efficiency of the team. Moreover, this approach of continuous improvement, which started at Trieste, was soon extended to factories in other cities as well.
In addition, for good reason. Zollia reveals that being able to freeze the production plan three months in advance was a crucial breakthrough for his team. "This brought more stability in the production line which led to shorter delivery times," Zollia says adding that the pre-planning in production immediately bore results. "The delivery centre in Trieste is now able to deliver ten Wärtsilä 18V50 engines in only four months from the time an internal order is received."
Nevertheless, this was just the beginning. The initial success marked a resounding acceptance of Operational Excellence by the team that had sensed the opportunity to evolve organically within and beyond their work areas.
Putting things in perspective, Zollia elaborates how he, along with his team, now understand the importance of redistributing and delegating work. "It has not only helped the team enhance their technical knowledge and empowered them to be self-sufficient, but also given me more time and energy to take a broader view of the operations," beams Zollia further adding that he now has the time to think of new ideas to improve processes and team efficiency.
What also boosted team confidence and performance was the introduction of TAKT time (shift a wise distribution of work) methodology during production. Quantifying this crucial progress was the fact that punctuality went up from 60% in Q1 2016 to 90% in Q1 2017. "By reducing the lead time, their punctuality in the start of assembly and delivery date improved drastically," explains Zollia.
With the stability plan on track, it was time to work on reducing the impact of design modifications on customer projects.
"Thanks to the delegation approach along with production support from technical office (PME) in Italy, we introduced the Model Year – managing design modifications in March and September months," explains Zollia. "This approach created good support not only for the customers and suppliers but also for the purchase departments."
For Zollia, the success of Operational Excellence is no coincidence but a well thought out plan that started with the setting of improvement goals in personal and professional life. Considering the rising stress levels within his department, it was decided to enroll Zollia for mentoring program under Fredrik Nordström, Director, and Operational Excellence at Wärtsilä. While it worked wonders for Zollia, he, in turn, passed the benefits to his team. The positive results not only improved the overall efficiency of the team but the stress levels went down too, which was reflected in Wärtsilä's global employee satisfaction survey ‘My Voice'.
Ask Zollia about the future of Operational Excellence and his face immediately lights up. "We have three branches of Operational Excellence at Trieste. One is connected to test runs and software implementation, second to the newly built machine centre in Trieste and the third one is integrated production planning that takes into account the needs of suppliers and customers."
One of the learnings from the application of the Operational Excellence principles Zollia says is to start from the bottom of the organizational pyramid and work to the top.
However, for now, the initiative of Operational Excellence is only getting bigger and better. As for Zollia and his team at Trieste, it is all in a day's work.