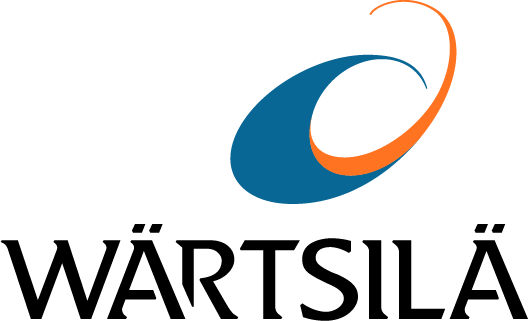
As nearly everyone knows, marine and power are highly competitive and cost-conscious businesses. Overcapacity, fluctuating energy prices, combined with an uncertain world economy, means that ship owners and power operators are looking for anything that can drive business efficiency improvements and increase profits.
If an owner/operator has a ship or power plant with an engine and a turbocharger, both will need servicing every 12,000 hours, or about every two years, which is known as Time Between Overhauls (TBOs). There are many variables, such as type of fuel burned, contamination, weather patterns and speed, which affect the engine and turbocharger performance. So how can owners and operators juggle all these factors?
“Everyone is looking to save money,” explains Arnold Feber, Business Development Manager of Turbocharger for Wärtsilä Northern Europe and Senior Account Manager for the Benelux countries. “Times between overhauls are getting longer, and owners are looking to slim down the number of vendors. In these changing market conditions, trusted and reliable partners are the best to turn to for engineering know-how, accurate performance calculations, upgrades and maintenance services. In the past, we were vendors of machinery. Now there is a very clear business case for partnering with customers.”
Wärtsilä Turbocharger Services is a case in point. As of January 2, 2017, four new, dedicated turbocharger maintenance workshops were added to its portfolio of around 70 service points around the world, of which 20 currently have special turbocharger capabilities. The new workshops in northern Europe – Murmansk, Russia; Rubbestadneset, Norway; Gdansk, Poland; and Schiedam, Holland – will handle turbocharger repairs and overhauls coming from the global Wärtsilä engine fleet and, in addition, will support other engine brand turbochargers as well.
“The primary mission is to make sure we support the Wärtsilä fleet globally. The secondary mission is to extend the offering to other engine brands,” says Broznic.
“We have now included turbocharger services into our global service portfolio and want to engage with customers worldwide with our certified competence, tools, and spare parts wherever the customers actually are, and with the different engines types and makers they are running,” says Marko Broznic, global Senior Product Manager, Wärtsilä Turbocharger Services, in Trieste, Italy. “Global services for turbocharger maintenance is our new mind-set, the keyword being global.”
Each of Wärtsilä’s 20 Turbocharger Services workshops is certified by the turbocharger manufacturer and will employ several certified engineers, who will have the capability to dismantle, overhaul, perform nozzle checks, clean and balance the units – a process which takes approximately 24 hours – during a port stay, for example. The final refurbished turbocharger, though sometimes up to two meters in length, also can be forwarded anywhere in the world as a fleet spare.
“Some of these workshops already had turbocharger capabilities. The difference is that we are now investing in training, specific tool sets and spare parts for approximately 30 different turbocharger models, and certification. This was more of a one-off thing previously. Now, it is a global service certified by the turbocharger manufacturers themselves,” says Broznic.
Plans are to increase efficiencies even further to gradually develop a so-called cartridge exchange program whereby turbocharger units in need of service would be exchanged with reconditioned ones. This would cut overhaul times by half, says Feber.
“Approximately 58,000 vessels visit our region [northern Europe] regularly, and if you do a rough calculation, 18,000 of these vessels are equipped with our engines and at least one turbocharger. So, obviously, there is plenty of work and fierce competition for services. But we are confident that the owners want to give the maintenance work to the partners, who can do the whole job and have the engineering know-how. As of March 2017, a full one-third of our service and maintenance orders were for turbochargers from other engine brands in the Schiedam workshop. My feeling is that the market is liking this,” says Feber.
“We want to be the first choice in total care,” he continues, making the point that ship owners only want one point of contact for their engine and turbocharger maintenance needs, regardless of who made them.
“Earlier, there would be a chain of discussions between different manufacturers, which created confusion and a lot of unnecessary back and forth as to where the malfunction lay. By expanding our service offering and expertise to include all turbocharger brands installed on our engines, we reduce the work, complexity and costs for the owners. At the same time, we are introducing a new service routine in what is essentially our natural habitat – engine and propulsion systems – that we did not offer previously. This makes the package complete!”
But an additional long-term benefit of the new arrangement – a total-care turbocharger package regardless of the engine brand – is that Wärtsilä anchors its competence, know-how and goodwill in the minds of ship operators and owners.
“This lays the foundation for future orders, which is the icing on the cake,” concludes Feber.