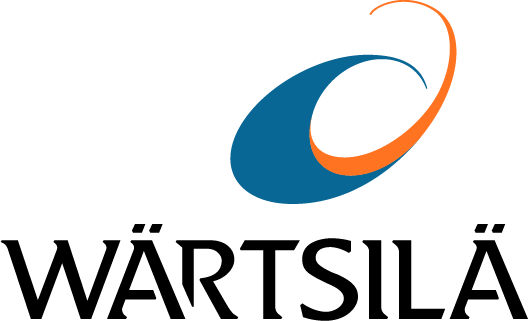
The first sailing ships that cruised along the coasts of ancient Egypt and Mesopotamia in 3,500 BC were humble affairs, typically constructed using planks of wood, tar and rope. Fast-forward to the current day and age, and there is no denying that shipbuilding has become a monumental feat, using exotic materials, cutting-edge technologies and involving numerous suppliers, sub-suppliers, engineering companies, classification societies, equipment providers and, of course, the ship owners themselves.
This is especially true of the cruise ship and passenger ferry sector. Construction here often involves multi-continental projects with, in a typical scenario, vessel owners being based in one continent, for example, America, the technology providers in another, usually Europe, while the shipyard labour and finance costs are controlled from Asia.
There are a number of reasons for this trend. While extended delivery times from the established yards, due to full order books, are causing cruise and ferry operators to seek new project partners, Asian yards are stepping in with lower costs and attractive financing. But these yards have only limited experience in this segment. In addition, a plethora of stringent regulations on emissions, ballast water management and wastewater handling procedures that are particularly relevant to ferries and cruise ships (since they operate close to coastlines and in protected waters), complicates matters even further. Since sophisticated technologies are required to ensure compliance with these regulations, sourcing these from multiple suppliers will only make the new-build process more complex.
The combination of numerous project partners and stakeholders, extended technology requirements, shipyards with limited experience, and multi-continental ecosystems inevitably raises the risk levels for new-build projects. The risks include:
Modern cruise ships require a multitude of complex systems and sub-systems, all of which need to exchange information correctly, efficiently and optimally. However, the sheer volume of signals, standards and systems involved means that a harmonious systems interface can be difficult to achieve.
As ship designers, suppliers and engineering specialists, with varying levels of experience (and varied work cultures), are located in different countries, the chances of communication failures leading to delays and increased costs are high.
New-build projects are broken down into systems and ultimately products that are defined by specification documents. The specifications relate to individual items, for example, the performance of equipment provided in a supplier, and not to the overall performance of systems. This means the performance verification of a full system cannot be guaranteed until the ship is built.
Considering the various elements and building blocks in a new build, there is a risk that the various systems will not have been integrated properly, which will lead to a deterioration in performance. This is something that may not be immediately apparent upon commissioning of the vessel but can have unfortunate consequences that emerge only after the vessel is delivered.
Maintenance and repairs of installed equipment and systems are required throughout the life cycle of a ship. However, due to equipment and systems being sourced from different suppliers, the availability of trained personnel and original spare parts cannot always be guaranteed. This, in turn, increases the risks of systems breaking down and significant downtime in cruise ship operations.
Systems that involve significant integration, such as those on cruise and large passenger vessels, are only as good as the weakest part. A system or part that looks fine on its own may, when working in synchronisation with other parts of the system, not function properly. This can lead to a snowball effect of failures throughout the system and last well into the life cycle of the vessel.
Table 1 - Estimated correction costs during multi supplier new-build stage.
But what do these challenges mean in terms of costs for a new-build project? Let’s break it down on and use a small size cruise ship of EUR 100 million value for an American owner and a Chinese yard.
Often during the procurement phase of new-build projects, more attention is given to CAPEX than to the value delivered by the equipment or system over the life cycle of the vessel. This results in situations where the systems integration is often underestimated – requiring additional time, resources and cost during the construction phase and operational issues that impact the vessel once it is commissioned. (Table 1)
With numerous suppliers involved, considerable time is required to manage all the communications and meet their deadlines. The financing costs alone can add several percentage points to the building price when delays occur. For a EUR 100 million cruise ship, a 6 months delay can easily lead to an extra 2 million* due to problems trying to integrate different systems from different suppliers. In addition, the cost of lost or cancelled cruise bookings or having to charter other ships in order to cover contractual route obligations makes a further dent to the budget.
Another ‘knock-on’ effect is when, during the procurement phase, the focus is primarily on products with low CAPEX often resulting in increased OPEX. For instance, having non-optimised equipment as part of the ship’s system can add 3% to OPEX = EUR 150,000 (based on annual fuel costs of EUR 5 million). This can add up to EUR 4.5 million over a 30-year life of the vessel.
The key to unravelling these complexities and minimising the risks involved in modern new-build projects lies in optimising the number of players involved. Companies, such as Wärtsilä, that have in-house capabilities in ship design, engineering, project management, performance insight and a broad portfolio of products, systems, and integrated solutions, can offer ‘end-to-end’ responsibility with services to support each element required, which delivers benefits throughout the life cycle of a vessel.
The benefits are as follows:
A single supplier is able to provide the complete scope of integrated systems and equipment required and ensure proper systems interface and coordination. Additionally, with deliveries made from the same source, the procurement process is significantly simplified, quality and progress can be monitored and controlled at every stage and the risk of building delays is greatly reduced, effectively guaranteeing the outcome.
When it comes to maintenance, companies are looking beyond short-term cost savings and investing in longer-lasting, safer and truly global solutions. A supplier like Wärtsilä can provide preventive maintenance to ensure day-to-day operations remain unaffected, and also assist with reactive maintenance for quick repairs that reduce downtime. A smart maintenance approach combining spare parts and field services from a reliable original equipment manufacturer (OEM) enables better maintenance planning and execution, supporting long-term business goals.
By reducing the number of suppliers and sub-suppliers involved, and taking a ‘one-stop-shop’ approach through having a qualified single provider with the right capabilities, solutions and experience, communication between the yard, the owners and the equipment provider is simplified. In addition, legal, finance and logistics can be dealt with in a unified way too. Advanced project and site management skills allow the overseeing and verifying of the project’s status, progress and quality every step of the way.
Environmental and Social Governance (ESG) must be taken very seriously today. For Wärtsilä, it is an embedded element in how the company sees its role in the developing marine ecosystem. This makes it the ideal partner for cruise ship operators who are keen on improving their environment and social governance goals.
That said, how exactly can Wärtsilä help cruise new-build projects save money? Procuring a complete and fully integrated system from a single OEM partner, such as Wärtsilä, who can deliver a ‘first-time-right’ proven solution removes these extra expenses, thereby optimising overall costs. It mainly adds up in two ways:
With numerous suppliers involved, considerable time is required to manage all the communications and to keep all on track and meeting their deadlines. Conversely, with a fully integrated system ordered from a single supplier, the work is handled by an experienced team of colleagues, working in unison, each with a complete understanding of the methods, standards and processes required. The engineering team is up and running quickly, and the entire operation from the design phase through to vessel launch is handled seamlessly.
The recommended approach for new-build projects is to employ a strategy of assessing the Total Cost of Ownership (TCO). Here, the aim is to achieve the highest possible overall output avoiding sub-optimisation and striving for uninterrupted operations. Having a complete and fully integrated system, designed and supplied by a single OEM provider who is prepared to undertake life-cycle management of that system through a service agreement can significantly reduce the TCO.
For instance, avoiding costs related to managing the maintenance of the equipment and handling downtime issues can save OPEX personnel costs of an estimated EUR 6,000,000* over 30 years. Based on 200k / year (1 shore side technical assistant and 1 administrative clerk) over a 30-year operational life cycle of a cruise ship.
The risks arising from a cruise new build can be alleviated by using a single supplier, like Wärtsilä, who has the experience to support and deliver new builds in line with the project requirements.
Wärtsilä’s expertise gives owners the option to select less experienced or newcomer shipyards for their new-build projects. After all, many of these yards have the ambition and the competitive edge to handle cruise and passenger ship construction but lack the necessary experience and supply base.
Choosing a single supplier and placing orders with the newer yards can potentially result in 20 percent cost savings, as evidenced by recent cases.
Additionally, the highly complex process of managing resources when building modern passenger and cruise vessels requires competent advisory support in order to overcome the various challenges outlined in this article.
This can only come from a reliable and strong partner with a global presence, a supplier like Wärtsilä.
*These are indicative estimates for illustration purposes only. They are based on standard industry hours and resources required for each element. Costs and values may vary depending on specific requirement.