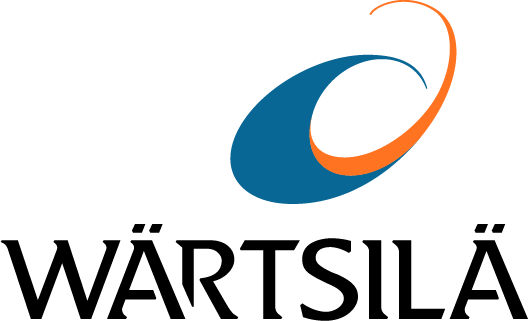
Digitalisation and data offer great opportunities to improve power plant efficiency. But what if you could also predict your power plant performance? With the right tools, expertise and data you can. This trio can help you to spot anomalies, foresee potential problems and react to them faster. In addition, it can give you guidelines on how to improve your power plant efficiency and optimise your operating costs.
I get asked a lot whether optimising efficiency could be done at an operational level as a do-it-yourself kind of solution. In my experience, problems can be addressed using the right technology, but getting to the root cause of the problems requires vast expertise.
Knowing what to monitor and how to analyse data helps you to get to the bottom of things. Real-time data enables you to foresee potential problems and react to them faster as well as to predict how to improve efficiency.
The amount of data you can get from an engine is massive. However, it’s not all usable and necessary. As you see, you need to use certain parameters to collect certain data, analyse it properly and understand it thoroughly. Only then you can locate the components that are causing performance issues and decreasing efficiency. If you need help with choosing the right parameters, we are happy to help you.
Monitoring and analysing the data gives you a chance to view your power plant performance from three time perspectives: past, present and future. It works as a sort of rear-view mirror giving you visibility to what’s already happened and the situation on hand, but it also gives you the power to look ahead and predict things based on data and artificial intelligence.
As you start using data more, the artificial intelligence component starts to become smarter. By this I mean that when we can connect the former and present data coming from the same engine, the predictability increases as the algorithm develops — that’s also called the trend analysis. Currently, we do anomaly detection and asset diagnostics pretty much the same way a doctor would inspect a patient. With the help of algorithms and artificial intelligence, we can tell what’s wrong with the engine.
Optimising power plant operation is a demanding task and requires a deep understanding of the engines — the kind of expertise you can only get from years of hands-on experience, continuous learning and a full understanding of the engine performance. Therefore, it’s very crucial who analyses your data and what kind of expertise they have on the subject.
Let me briefly elaborate on the data analysis process. Firstly, the data is analysed with the help of tools and processes that are complicated to master. Secondly, the experts who are involved with the engines use their analytical skills and years of experience to zero in on areas of concerns and look at them in detail. Thirdly, they need to pick up on trends.
To put this into perspective, imagine a case where a client depends on a baseload of 90 % usage of all engines. With limited artificial intelligence, picking up on trends can be like looking for a needle in a haystack. The person responsible for availability and reliability needs to know what to monitor and how to analyse the data to be able to connect the different dots and come up with recommendations on what could be the problem and the possible solutions. As I mentioned earlier, understanding the root cause and identifying possible solutions is crucial and requires vast experience.
To cut a long story short, any kind of improvement in efficiency equals money saved. Monitoring requires time, but in the best-case scenario you’ll see significant results. In some cases, it takes longer to see the improvements while sometimes they can happen fast — it’s a matter of what is being measured. Measuring heat rate, for example, doesn’t give you noticeable results overnight. Instead, you need to build up a trendline to see in which direction things are going.
Sometimes, you will be pleasantly surprised to see a noticeable improvement in efficiency at a rapid pace, let’s say within weeks. This is what actually happened to one of our customers a while ago. We set new tuning parameters and applied real-time monitoring of heat rate, for example, which enabled collecting and analysing data. Thanks to our continuous measurements, we could see that the engines weren’t running optimally and re-tuned them. In just a few weeks we could see one percent improvement in efficiency which in turn resulted in remarkable savings. In this case, not only real-time monitoring was required, but also expertise to analyse the data and understand what measures to take.
Another great example of real-time monitoring and managing data accurately involves another customer of ours. As the power plant was aging, the engines weren’t being upgraded resulting in expensive engine stoppages and increased fuel consumption. As we started monitoring the plant performance continuously and organised regular performance checks, we were able to do continuous improvements based on the data. As a result, the power plant efficiency level changed to a stable level resulting in noticeable savings.
Digitalisation is the wagon that everyone is trying to hop on right now. As the world is changing, it’s inevitable that those who don’t follow the change will be left behind and miss out on business opportunities — that’s also the case in the energy industry. That being said, I see my colleagues’ and my role as being in the driver’s seat of the wagon: Rather than resisting it, it’s our job to help our customers embrace it – and make the most of it.
Writer Edwin Magesh, General Manager Operations MEA at Wärtsilä Energy Business, has over 20 plus years of experience in supporting energy and marine customers in the field. He is currently involved in expanding ongoing offerings at Wärtsilä through digital platforms enabling profitable business for our customers.