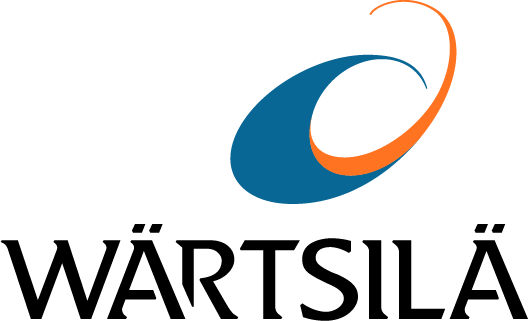
Keeping your turbochargers in prime condition and up to date is essential for the overall performance of your engines. A well maintained turbocharger ensures maximum fuel efficiency and prevents unexpected operational costs.
Turbocharger maintenance, combined with engine maintenance or separately, can be provided as a long term maintenance solution, extending the lifetime of all types of equipment for your installations. Learn more about Wärtsilä Turbocharger services.
In Middle East & Asia (MEA), there is an installed base of over 3300 turbochargers. Today, a total of over 1800 operating land based engines in MEA trust Wärtsilä’s high quality maintenance.
When it comes to keeping the turbochargers running efficiently and preventing unexpected failures, Wärtsilä stands at your service. With over 2000 dedicated professionals in the Middle East & Asia, we are ready to serve you in the best possible way.
Turbocharger maintenance is essential for the overall performance of the engine.
As an engine manufacturer Wärtsilä has extensive experience and expertise in turbocharging technology and is the only true global service provider in the market licensed to service ABB, Napier and KBB turbochargers.
A wide range of genuine spare parts for the complete installation and auxiliary systems are available thanks to our worldwide strategic agreements. Regularly auditing our supply chain ensures that our customers receive high quality, cost-efficiently, on time.
New Caledonian company, ENERCAL, wanted to optimise the operational cost and performance of their power plant. The solution was a Wärtsilä 46 Performance optimisation, consisting of engine tuning by means of a camshaft modification to Miller timing and an upgrade to ABB-TPL76C turbochargers. Two years of operation has established a 5g/kWh improvement for each engine, which enabled savings of about $400,000 in 2016.
SUCCESSFUL UPGRADE PROJECT
Before the performance optimisation, the specific consumption of the power plant was about 218g/kWh with a utilisation rate of 52%, totalling the average annual consumption of fuel to about 55,000tons/year. In 2014, the price of the fuel amounted to approximately 73% of the global plant operational costs.
– The management of ENERCAL wanted to optimise the operational costs of the plant and decided in favour of a Wärtsilä 46 Performance optimisation, consisting of engine tuning by means of a unique camshaft modification to Miller timing and an upgrade to ABB-TPL76C turbochargers on two engines in September 2014, says Mr. Theodore.
Installation and commissioning took place during a scheduled major engine overhaul, which minimised the overall downtime. Performance tests were carried out before and after the modification.
– The two efficient Wärtsilä teams were well organised and were fully supported by Wärtsilä managers, which – to a great extent – helped to make the project a full success. The upgrade went as planned and the minor challenges only concerned the different pieces of equipment that needed to be changed for the upgrade, says Mr. Theodore.
EXCEEDING PERFORMANCE EXPECTATIONS
According to Mr. Theodore, the results of the performance optimisation have been very clear and rewarding. Both the performance due to the overhaul of the engine and the performance due to the upgrade of the turbochargers were separated. Wärtsilä’s performance warranty stated a SFOC saving of 4g/kWh. However, the performance tests managed to record savings of more than 8g/kWh. These high savings results were partly due to the engine overhaul.
– After two years of operation, and comparing to the two unmodified engines, we have been able to establish a 5g/kWh improvement for each engine, which exceeds the promised saving. So, the performance improvement due to this upgrade of the power plant is real, says a satisfied Mr. Theodore. What does this performance improvement mean for ENERCAL as a company?
– In 2016, our company saved about $400,000. We could have had even greater savings if the modified engine had been in baseload operation, says Mr. Theodore. Now a couple of years after the performance improvement, ENERCAL continues to enjoy the benefits of the upgrade and Wärtsilä’s services. Mr. Theodore also appreciates the high quality of assistance from Wärtsilä and says that it is one of the reasons why he wants to continue cooperation with Wärtsilä.
– Today, we are very satisfied with this modification in terms of fuel consumption. If you have a Wärtsilä power plant running in baseload mode, I recommend doing a performance optimisation upgrade. Even for us, operating the plant as a peak load plant, it is very beneficial and fuel prices will surely rise again during the coming years, concludes Mr. Theodore.
Installation of a Wärtsilä 46 performance optimisation package consisting of engine tuning by means of unique camshaft modification to Miller timing and an upgrade to ABB-TPL76C turbochargers and other engine components & settings.