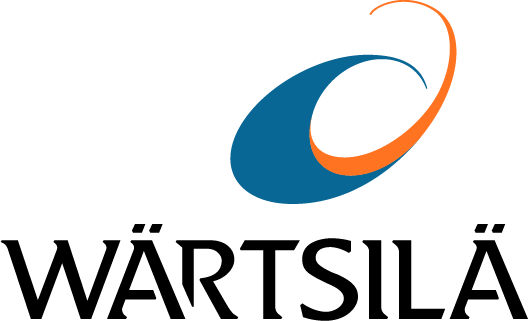
Wärtsilä Corporation has received considerable interest for retrofitting of the new, electronically-controlled Pulse Lubricating System (PLS) to RTA and RT-flex low-speed marine diesel engines. Orders have already been received for 25 complete engine installations, amounting to 284 cylinders, and the first retrofit was completed in September 2006.
The Pulse Lubricating System delivers reduced cylinder oil consumption without compromising piston-running reliability. This is made possible through an improved distribution of cylinder lubricating oil to the cylinder liner, and the fully flexible, precise timing of oil delivery.
The Pulse Lubricating System is available now for retrofitting to RT-flex96C and RTA96C engines, and will be available from January 2007 for RT-flex84T-D and RTA84T-D engines. Additional engine types will be added to these in 2007.
The first full retrofit is to the 12-cylinder RTA96C main engine of the 7500 TEU container ship “Cosco Shenzhen” managed by E.R. Schiffahrt GmbH & Cie KG of Hamburg. The retrofit was completed by Wärtsilä service engineers in Long Beach, California, USA, early in September 2006 without any delay to the ship’s sailing schedule. E.R. Schiffahrt has contracted Wärtsilä to retrofit the Pulse Lubricating System to all nine RTA96C engines in its fleet.
“With its improved capability and considerable cost savings, this new cylinder lubricating system is a notable performance improvement to the Wärtsilä engines and we look forward to rapid completion of the series of nine retrofits”, says Willem Dekker, Chief Operating Officer, of E.R. Schiffahrt.
The guide feed rate for RTA and RT-flex engines retrofitted with the Pulse Lubricating System is 0.8 g/kWh of cylinder lubricating oil.
Thus the cost savings achievable by a retrofit with the Pulse Lubrication System are significant. In the case of a 12-cylinder RTA96C engine of 68,640 kW maximum continuous output, running at 85 per cent load for 7000 hours a year with cylinder oil costing US$ 1700/tonne, the reduction from the guide feed rate of 1.1 g/kWh (0.8 g/bhph) with the existing accumulator system to the new guide feed rate of 0.8 g/kWh (0.6 g/bhph) can generate cost savings of well over US$ 200,000 a year. This corresponds to a cost saving of about 27 per cent for cylinder lubricating oil.
The key feature of the Pulse Lubricating System is that it delivers accurately metered, load-dependent quantities of lubricating oil to the cylinder liner running surface at the precise timing required. Electronic control ensures the accurate dosage and timing, with full flexibility in settings.
The cylinder lubricating oil is fed as a pressurised pulse through lubricators exactly into the piston ring package and on to the piston skirt from where it is evenly distributed around the circumference of the liner.
The lubricators (formerly known as quills) are fitted in the lower quill openings in the existing cylinder liners. Cylinder oil is delivered under pressure to these lubricators by a newly-developed dosage pump which is powered by pressurised servo oil drawn from the engine’s system oil. The feed rate and timing are electronically controlled through a solenoid valve at the lubricator pump. There is full flexibility in the setting of the lubricator timing point, and volumetric metering ensures constant spray patterns across the engine’s load range. The dosage is precisely regulated even for low feed rates.
Service experience
Service experience with the Pulse Lubricating System has been very successful with excellent liner and piston ring conditions. Trials have been carried out both on the Wärtsilä research engine in Winterthur and on shipboard engines.
The first Retrofit PLS test started on the research engine in June 2003. Shipboard testing began with an RTA58T engine in September 2004, and later with an RT-flex96C engine. Shipboard testing has accumulated more than 14,000 running hours. Throughout the outstanding performance of the Retrofit Pulse Lubricating System was confirmed, with all testing being at or below the guide feed rate of 0.8 g/kWh.
Retrofit installation
The Pulse Lubricating System can be retrofitted during commercial operation of the vessel. It is an independent system with only few connections or interfaces to other systems, and utilises the engine’s existing cylinder liners. Thus preparation and installation are easy and fast. All equipment including prefabricated piping is supplied, with installation and commissioning being undertaken by Wärtsilä service engineers.
To a substantial extent this material can be installed during the voyage considerably reducing port time required for final installation and commissioning. Installation of controls, pumps, wiring and interface connections to remote and alarm monitoring systems is executed during the voyage as well. Ample attention is paid to commissioning, fine adjustment and running-in of the Retrofit PLS in port and during a confirmation voyage.
Shipowners can obtain further information on retrofitting the Pulse Lubricating System at rpls@wartsila.com.
Media contact:
Marit Holmlund-Sund
Public Relations Manager
Wärtsilä Corporation
Direct tel: +358 10 709 1439
Direct fax: +358 10 709 1425
e-mail: marit.holmlund-sund@wartsila.com
Internet: www.wartsila.com
Notes to the editor:
Wärtsilä Corporation
Wärtsilä enhances the business of its customers by providing them with complete lifecycle power solutions. When creating better and environmentally compatible technologies, Wärtsilä focuses on the marine and energy markets with products and solutions as well as services. Through innovative products and services, Wärtsilä sets out to be the most valued business partner of all its customers. This is achieved by the dedication of more than 12.000 professionals manning 130 Wärtsilä offices in over 60 countries around the world.
E.R. Schiffahrt.
The shipping company E.R. Schiffahrt GmbH & Cie KG was founded in 1998 and is responsible for project development and commercial and technical management of shipping funds. At present, it has 76 container ships in operation and under construction with a capacity of some 350,000 TEU. Thus, this Nordcapital subsidiary is one of the world’s largest charter shipping companies for container ships.