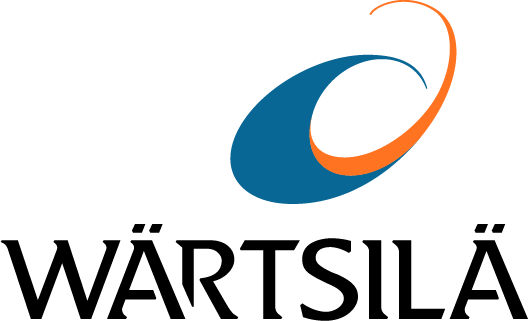
Gas-powered plants are the most responsive and flexible power generating assets in electricity markets. They are dispatchable and can adjust their load daily, ramping up and down with demand and balancing the intermittent production of renewable energy sources. However, aeroderivatives struggle with low total net efficiency during the short-duration pulse loads needed to balance solar and wind output. Wärtsilä reciprocating internal combustion engines offer significant advantages over gas turbines in this regard, with higher pulse load efficiency and the capability to provide ultra-flexible and cost-efficient output. The pulse efficiency is the net efficiency for the duration of the operating period, including start-up, shutdown and part-load operation.
Gas-powered plants are often ramped up and down, or cycled, in response to changes in demand and load. The time required to ramp up and down, efficiency at part load, and overall duration or plant output determine the fuel consumption and economic performance of the plant.
Unlike baseload plants that operate continuously, flexible power plants can provide short-duration load, or pulse load. Pulsed loads are produced in response to the sudden loss of a power generator, reduced output from wind and solar sources or spikes in demand. Pulse generation improves reliability and power quality by stabilising the electricity grid. Figure 6 shows data obtained from Australia’s National Electricity Market (NEM), showing how engine technology can flexibly adjust the load when needed.
Figure 6: Electricity Market data demonstrating how engine technology can flexibly adjust load as required.
Power plant owners want to optimise operation in order to minimise fuel consumption and maximise revenue. The start-up time, time to ramp up output to full load, operation at a minimum load and the efficiency at part load determine the amount of fuel consumed (energy input) and the length of time the plant operates each day. By producing output during peak demand times, the power plant earns revenue from high electricity tariffs. Ramping up and down should be as fast as possible without risking damage to the power plant equipment.
As discussed above, the efficiency of a plant producing pulse loads can be dramatically different from the efficiency at baseload. Combustion engines can reach full load and curtail output to zero within minutes. Because they are based on modular architecture, Wärtsilä engine power plants offer the additional advantage of being able to operate at part load by running only a subset of the engines at full load, maintaining full efficiency.
The efficiency of aeroderivative gas turbines is lower compared to combustion engines and it degrades at part load. Gas turbines reduce power output by reducing the flow through the turbine, which also reduces the combustion temperature and thus the efficiency. Frequent starts and stops will further reduce the overall pulse efficiency of turbines.
Figure 7 shows a double pulse load profile for an aeroderivative gas turbine power plant compared with a Wärtsilä engine power plant. Firstly, there is a start-up phase where equipment is ramped up to full load, taking into account the start-up times of the different technologies. During the first pulse, full load operations are maintained. After a short shutdown period following the first pulse, the equipment is ramped back up to full load for the second pulse. The duration of each pulse is 60 minutes, with a 60-minute curtailment between pulses.
Figure 7: Load profiles over a double pulse.
As the figure depicts, the start-up and shutdown times increase the total time the aeroderivative gas turbine plant operates, leading to higher overall fuel consumption and operating expenses. Conversely, the fast start-up and shutdown of Wärtsilä power plants reduces fuel consumption and minimises non-productive operating hours. From a performance perspective, the differences between the technologies become even more evident as the achieved pulse efficiency of Wärtsilä power plants is over 46 per cent compared to less than 36 per cent for aeroderivative gas turbine plants. In terms of fuel consumption, an engine power plant can use up to 25 per cent less fuel compared to an aeroderivative plant.