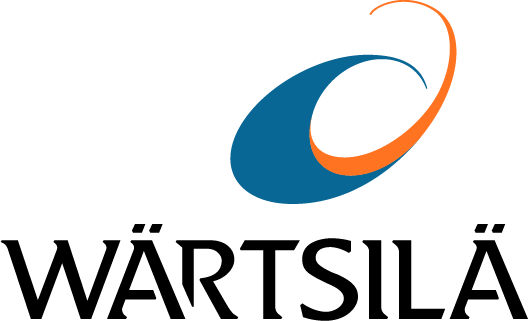
Volatile Organic Compounds (VOC) are light components of crude oil, which evaporate during loading operations or during the carriage of high-volatility crude oil cargoes. The cargo vapour needs to be vented to the atmosphere to prevent pressures in the tank reaching dangerous levels. Large quantities of VOC are also emitted to the atmosphere during loading of shuttle tankers in oil fields. It is estimated that annual VOC emissions in the Norwegian regime are almost 350,000t, of which around 200,000t are attributed to shuttle tankers and other crude oil carriers.
STATOIL has been investigating VOC emissions since the mid 1980s. A survey on two shuttle tankers in 1987-89 demonstrated that difference between cargo loaded on the field and the amount delivered into the receiving terminal ashore was almost 0.2% by weight. For a 100,000t load, the loss is thereby 200t.
The discharge of VOC creates environmental problem and represents a great loss of energy. Two solutions can be adopted: VOC re-absorption, whereby vapour is returned to the cargo, and VOC reliquefaction.
A pilot plant for VOC collection and re-absorption into the cargo was installed aboard the 113,000dwt shuttle tanker TOVE KNUTSEN in 1994, and achieved a recovery rate of roughly 75%.
On 19th May 1999, the 400m3 VOC fuel tank and the deckhouse with all main equipment for VOC recovery and fuel distribution were placed onboard the NAVION VIKING. It was the first plant engineered with twin objectives of minimising the release of VOC into the atmosphere and using the recovered, condensed vapour to fuel the propulsion machinery.
The plant designed by Wärtsilä Hamworthy comprises VOC compressor, which takes the feed gases from the cargo tanks. The compressed gas is then led into seawater cooler where the first phase of liquefaction and separation takes place. The gases are put through a gas drying process. Gases from the first stage are fed through a duplex molecular sieve dryer which takes the dew point down to around -50°C. One unit dries the gas while another is regenerated with heated surplus gas from the second stage.
In second stage liquefaction the dry gases enters a stack of six plate exchangers. Three exchangers use remaining gas (ethane and all methane), inert gas and cold VOC from the second stage separator as coolant. The other three use cold propylene produced from a separate cooling plant as coolant. The gas/liquid mix is then fed to a separate tank where half of the ethane and all the propane, butane and all higher hydrocarbons fall out as liquid.
Surplus gas is used for heating and regeneration of the dryer before it is vented.
VOC is pumped re-warmed in the plate exchangers before it mixes with liquid from the firststage separation and is led to the VOC storage tank on deck. VOC is used either as fuel for the main engines or is reinjected back into the cargo tanks.
Hitec Marine AS has developed a system for return of VOC emission gases from the shuttle tanker to the FPSO. The VOC recovery process is based on direct absorbtion of VOC in a side stream of loading oil. The oil containing absorbed VOC is then re-mixed with main oil loading stream. The equipment is assembled on a standard modular turnkey skid, which is supplied ready for hook-up to the applicable ship’s system.